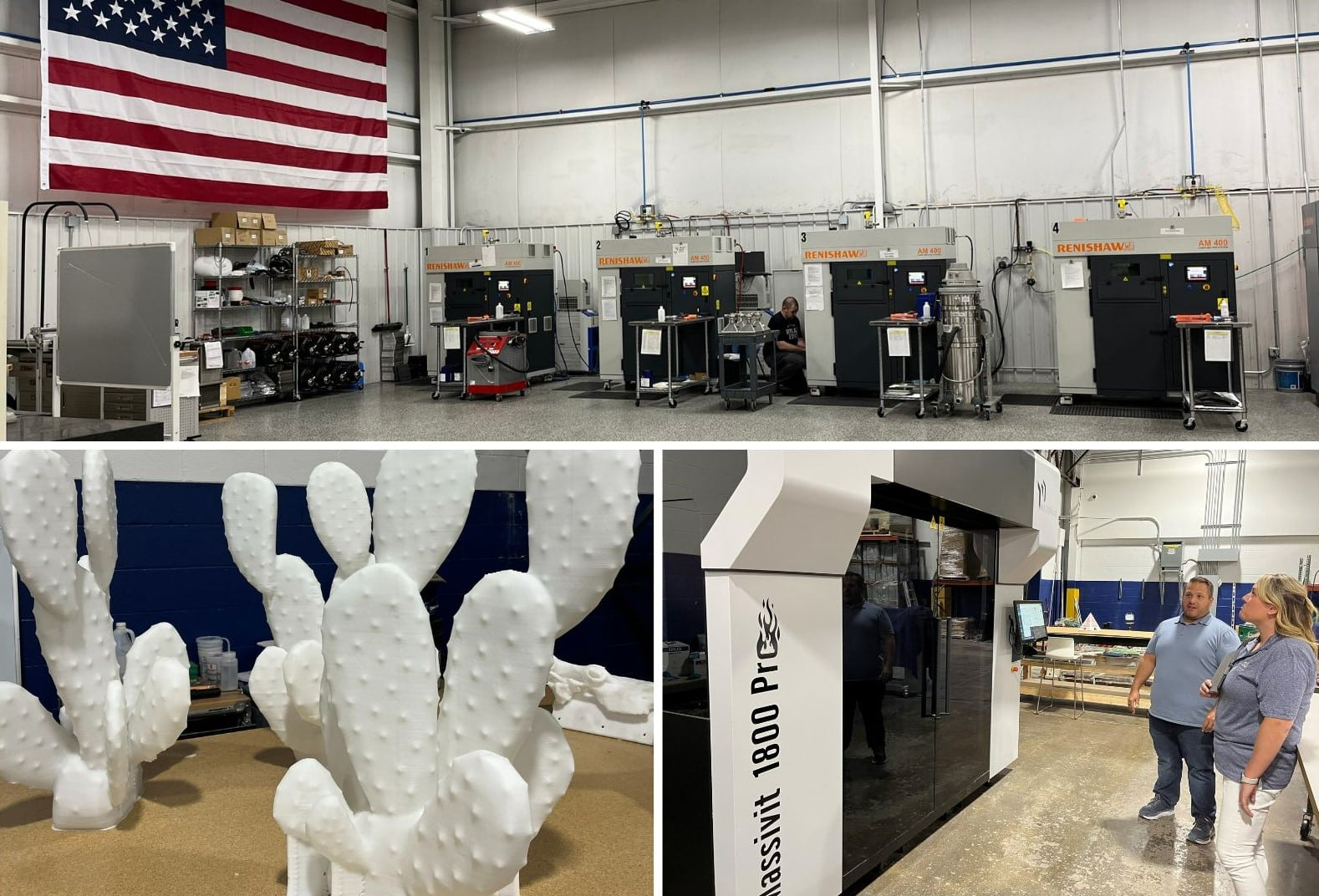
When our mid-August travels took us to a trio of Central Indiana businesses, we found they all share a drive for growth fueled by innovation and ingenuity.
In Madison County, a visit to Sirmax North America exposed us to a growing Italian firm that has adapted to a U.S. market that is quite different from other global markets. Anderson is home to two of the company’s 13 international production facilities, where they manufacture polypropylene compounds and recycle plastics.
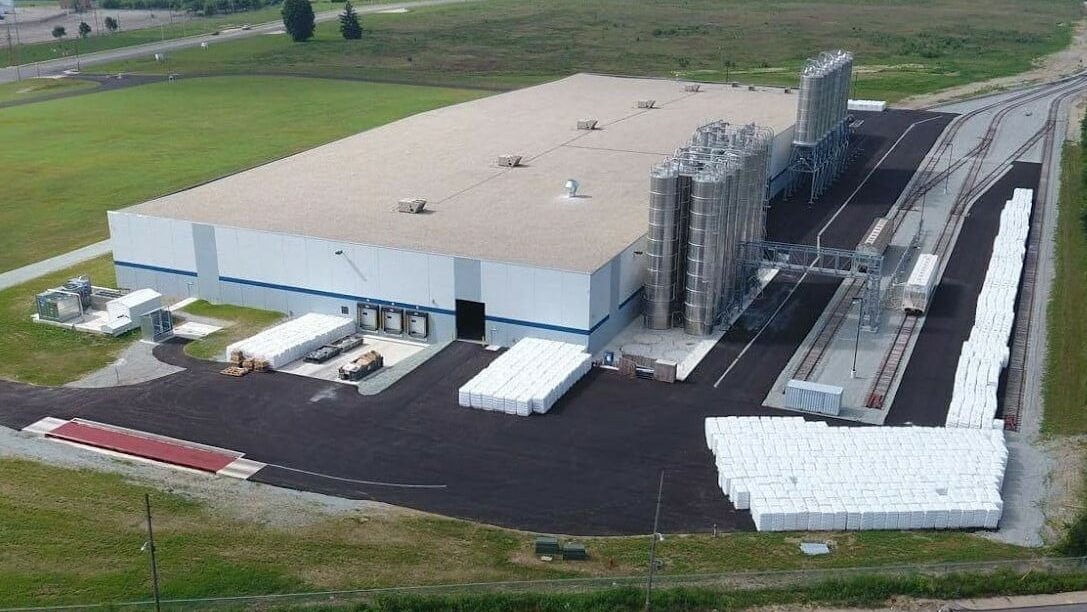
Because post-consumer recycling is not as viable in the U.S. as in Italy, Sirmax focuses on post-industrial plastics in Anderson, where the company occupies the site of a former GM plant. With about 100 employees, the company shared that it expects to hire more than a dozen more in coming months at the Anderson location. It is working with the City of Anderson on an advanced manufacturing training program and hires through INFAME (the Indiana Federation for Advanced Manufacturing Education).
Indianapolis’ Creative Works also occupies a reclaimed property, having taken over an old Mike Sells Potato Chips manufacturing facility. A creator of immersive décor and components for entertainment venues such as miniature golf courses, laser tag facilities and theme parks, the roughly 80-employee firm works with projects all over the world, and 95% of its clients are outside Indiana, allowing the company to bring those economic dollars back to the state.
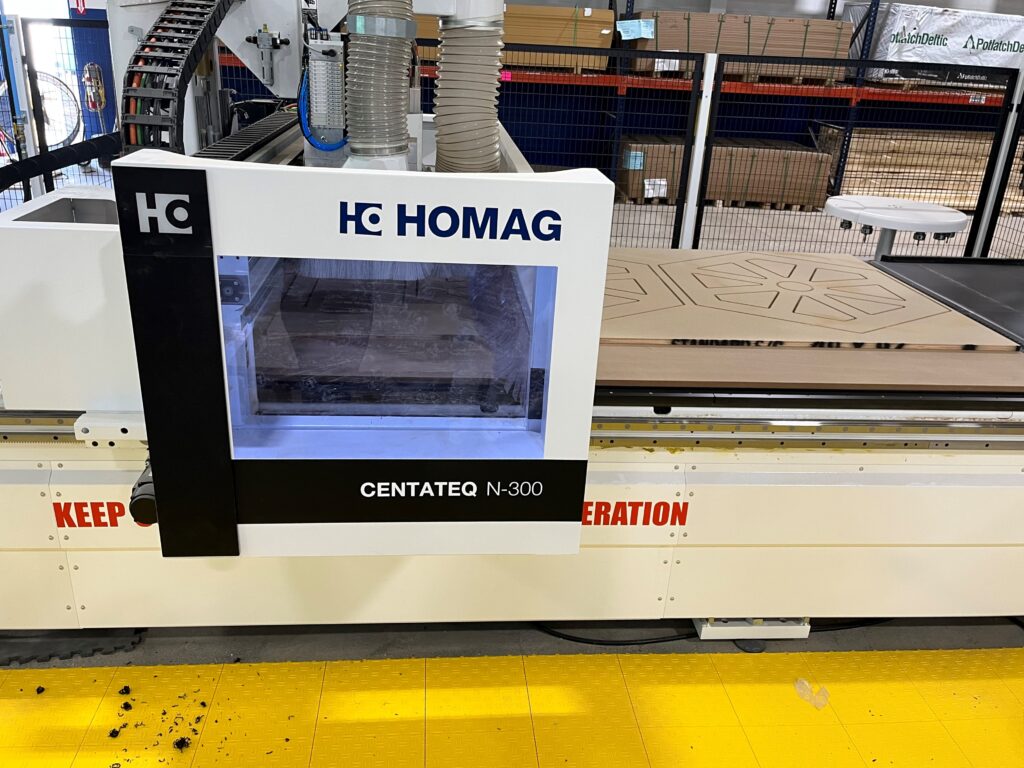
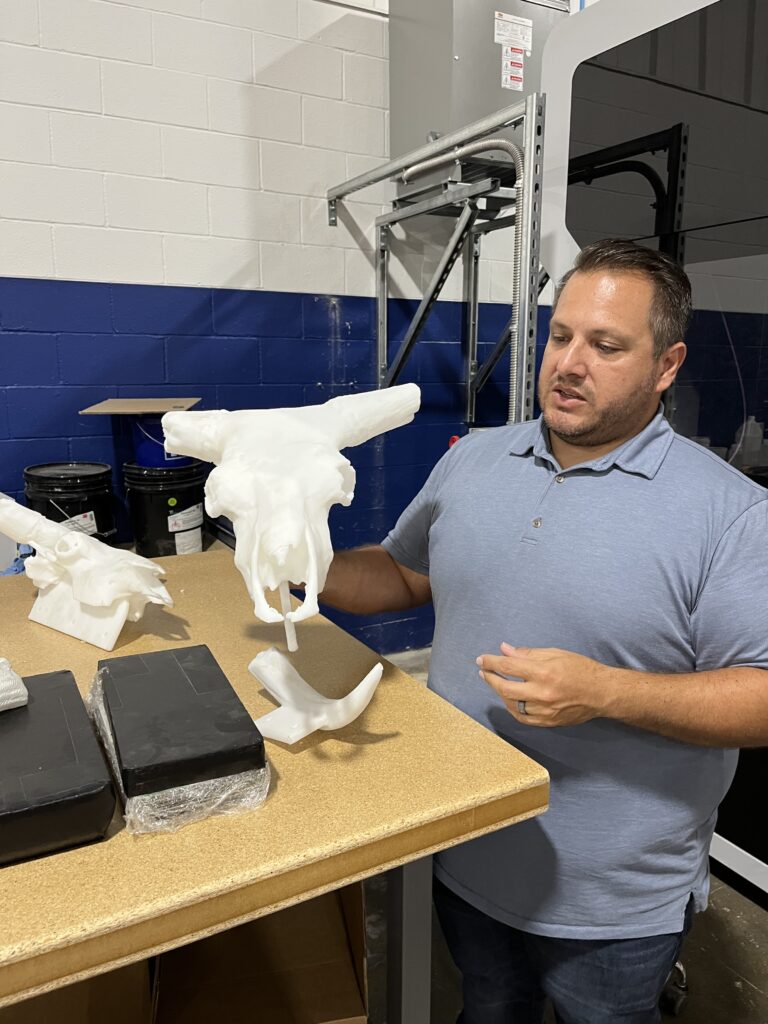
The firm has earned two Manufacturing Readiness Grants (MRG), which were used to purchase equipment that allowed them to increase efficiency and speed up production. In one example, the firm noted that a piece that used to require 25 to 30 hours to produce is now created in one hour thanks to a 3D printer purchased with the MRG.
In Johnson County, Franklin’s Innovative 3D Manufacturing also has made good use of 3D printing technology, as well as CNC machines, to serve its clients in the aerospace and defense industries. With fewer than 10 employees, the firm operates 24/7 to meet clients’ needs – and, during the pandemic, the needs of its community. When Johnson Memorial Health discovered that older equipment needed to protect health care professionals lacked a part that couldn’t be found in the supply chain, Innovative 3D fashioned a prototype and then manufactured the part.
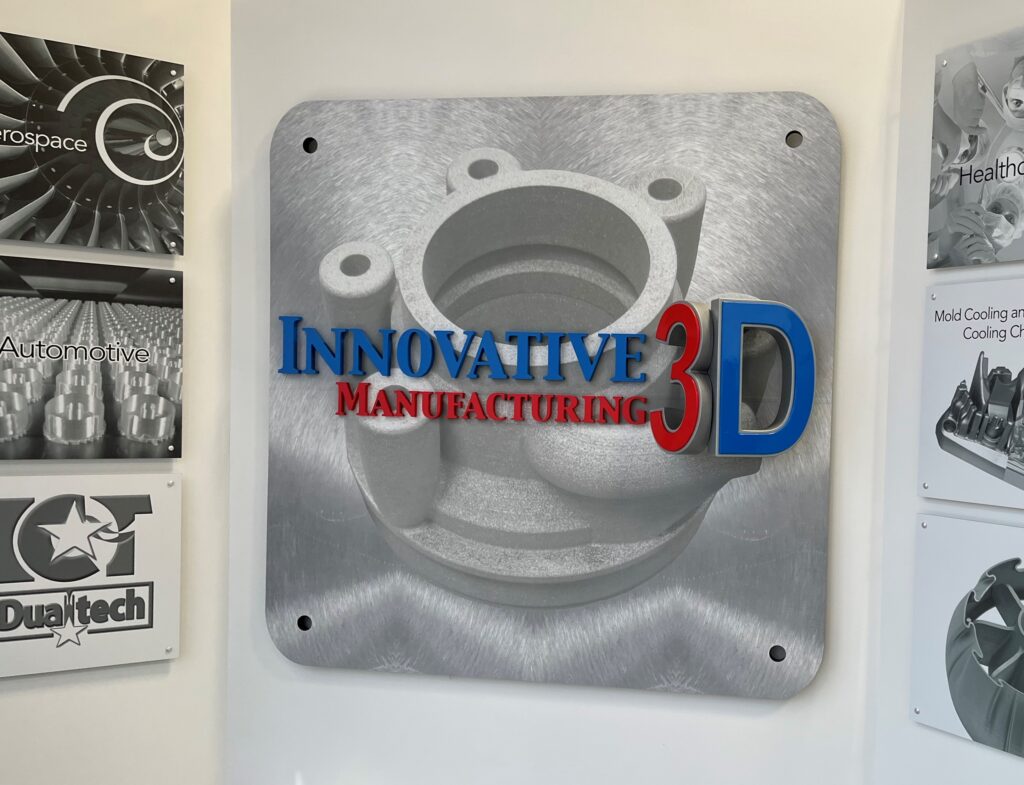
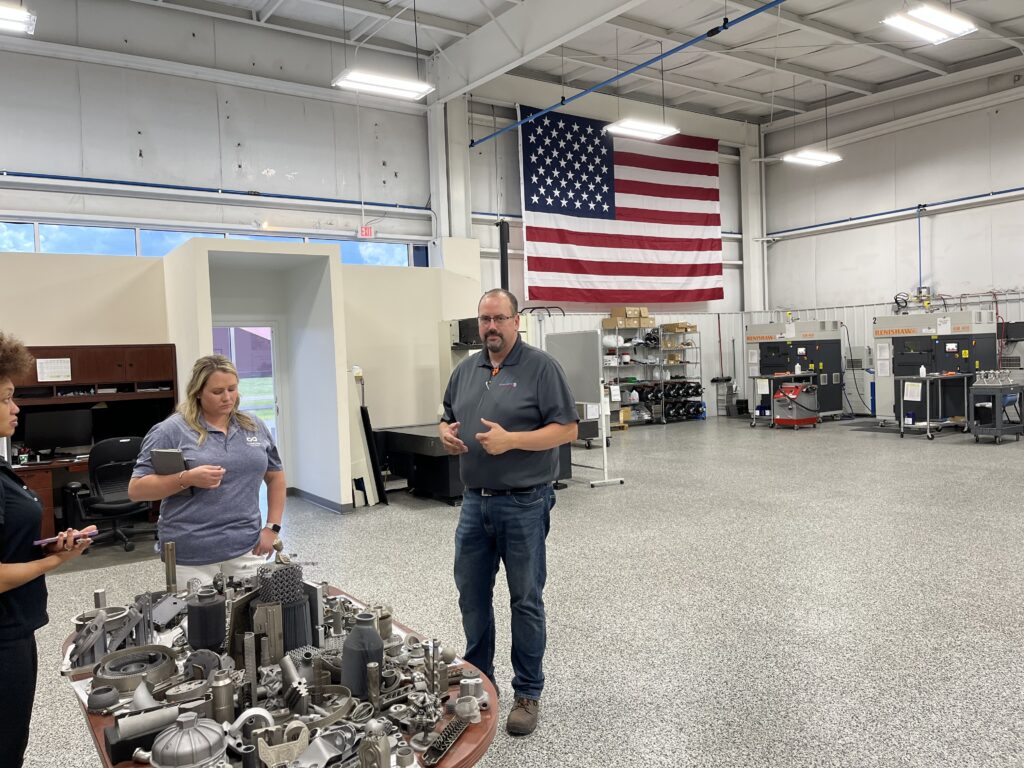
This post is a part of a series called 100 IN 100 – a look at Conexus Indiana’s staff visits to advanced manufacturing and logistics employers across the state. Conexus is visiting 100 companies in 100 days during the spring and summer of 2022.