Workforce Development Lessons from Greater Lafayette
Kara Webb of Greater Lafayette Commerce
How a dynamic dot-connector brought together schools, public officials and manufacturing leaders to create a vibrant program to expose kids to advanced manufacturing and logistics — and have fun along the way
Greater Lafayette Commerce (GLC) works with schools and local industry to create targeted educational programming, career coaching, stackable credentialing and employer tuition assistance programs. In the workforce development space, Kara Webb is the driving force behind her organization’s success. Under the umbrella of GLC, Webb, who serves as director of workforce development, has built four strong programs for K-12 students: Manufacturing Week, Manufacturing Month (an online program that gives teachers in nine counties free access), Robotics in Manufacturing Camp and CoderDojo, a kids’ coding club.

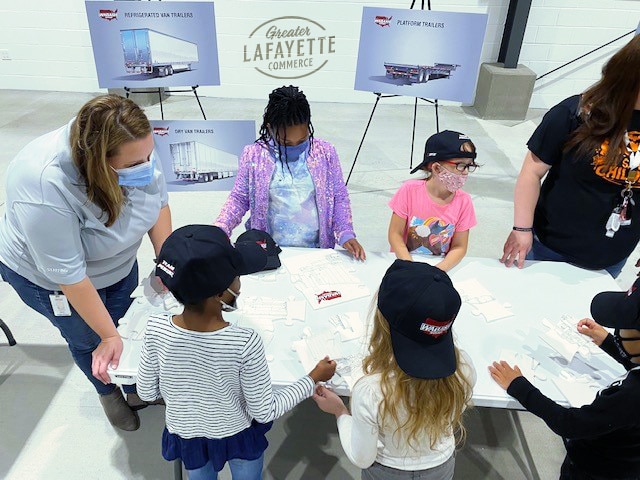
Last year, Webb and her team, including people from GLC, Ivy Tech and Skyepack, won a $4.9 million student learning recovery grant from the state of Indiana. “It’s pretty massive,” Webb said. “We’ll have 20 manufacturers in classrooms virtually in eight schools every week, telling their stories and teaching employability skills.” This year the same group of collaborators won a $3.6 million Explore, Engage & Experience grant.
Talking to Webb, you get the feeling that she could move the needle in the advanced manufacturing and logistics (AML) workforce in any region. Clearly, her enthusiastic approach is part of the equation. “My whole life has been built on connections,” Webb said. Her gift of bringing people together — along with charisma and a lot of heart — drives her success. “It’s true that it’s a very unique role I’ve created, and I’ve been fortunate to work in this region, where people work together to solve problems and collaborate on solutions,” Webb said. “But there are opportunities for people in other places to serve in the way I do.”
As you work to build stronger workforce connections in your region, consider these suggestions gleaned from Webb’s example.
It takes time … and the right person.
You could say that, in the context of boosting student and community engagement in advanced manufacturing and logistics, Webb is exactly the kind of person every community needs, and the program she helped develop is the ideal kind of program. But Webb’s success didn’t happen overnight. “I’ve been in this role in workforce development for 20 years,” she said. “It takes time, but it’s so worth it for the community.”
Webb got her start in workforce development after a layoff. Hours after she filed for unemployment at WorkOne, she was invited to meet with her future boss at the state unemployment office. A few years into working at the Department of Workforce Development, unemployment was at 10.6%, and Webb helped employers sift through applications. She also tested applicants. “I got familiar with needs and opportunities in manufacturing,” she said. “I got to know manufacturers and HR departments. Sometimes I talked with CEOs — that’s where I met Andrew Ball (Chairman of the Advanced Manufacturing Council at Conexus Indiana). And I kept those connections going.”
It takes creativity … and personal initiative.
By 2014, the pendulum had swung the other way, and Webb started to build awareness of opportunities in manufacturing. “The term ‘talent pipeline’ wasn’t used back then,” she said. Her boss challenged her to start a new program for Manufacturing Day. “Traditionally, students show up and it’s all on the shoulders of the employer.” Webb had a different take: “I served employers by doing the project myself.”
Webb gathered employers together, scheduled tours and took 300 students on facility tours. After that, she joined GLC and added middle-school students to the program. A few years later it expanded to the K-12 space.
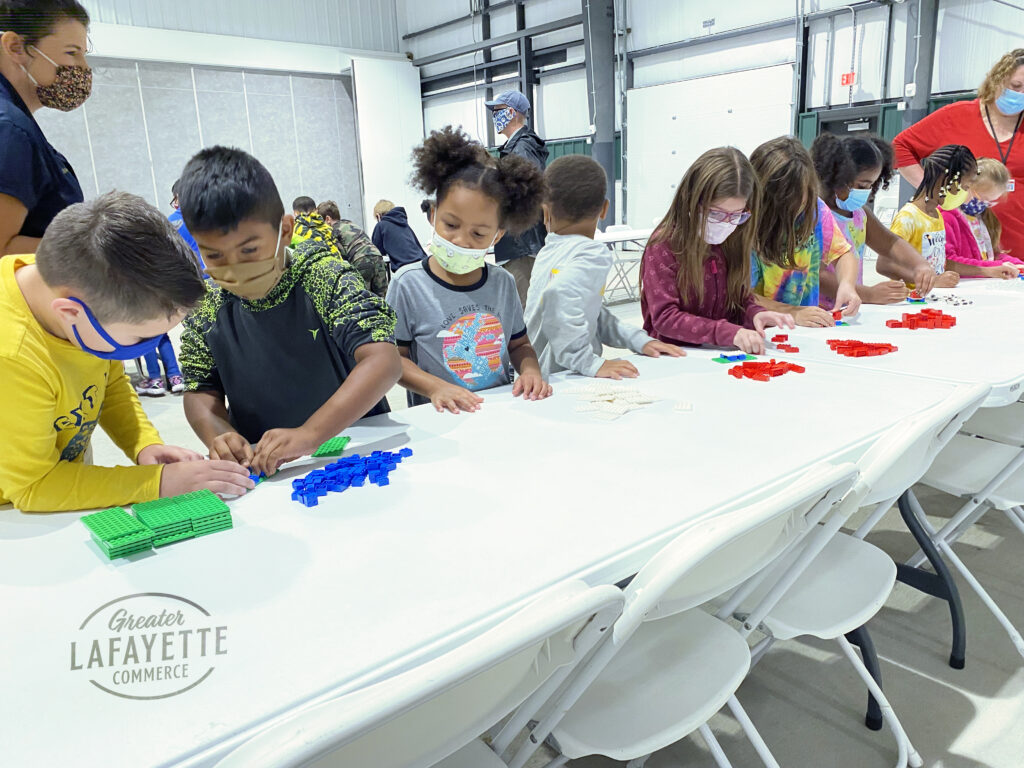
“In schools, people ask kids, ‘Do you want to be a firefighter, a doctor, a nurse?’ Webb said. “Nobody talks about manufacturing. There’s a stigma that it’s in a dirty place and there’s no room for improvement or success.” To combat those negative perceptions, Webb began asking questions that led to a revamp of Manufacturing Day, which evolved into a five-day program: Manufacturing Week.
Working hand-in-hand with local manufacturers, Webb tackled tough questions students might ask, like “How do I see myself in manufacturing?” How did Webb build such strong collaborative connections? “We really do work together here in Greater Lafayette,” she said. “We build relationships, and people know where our heart is.”
To reach young people, Webb and her team designed Manufacturing Week to include a themed tour. The program’s easy-to-understand format covers four distinct areas in manufacturing: design it, produce it, move it and support it, and careers associated with each area. In 2019, the program reached over 4,000 students in the Greater Lafayette region.
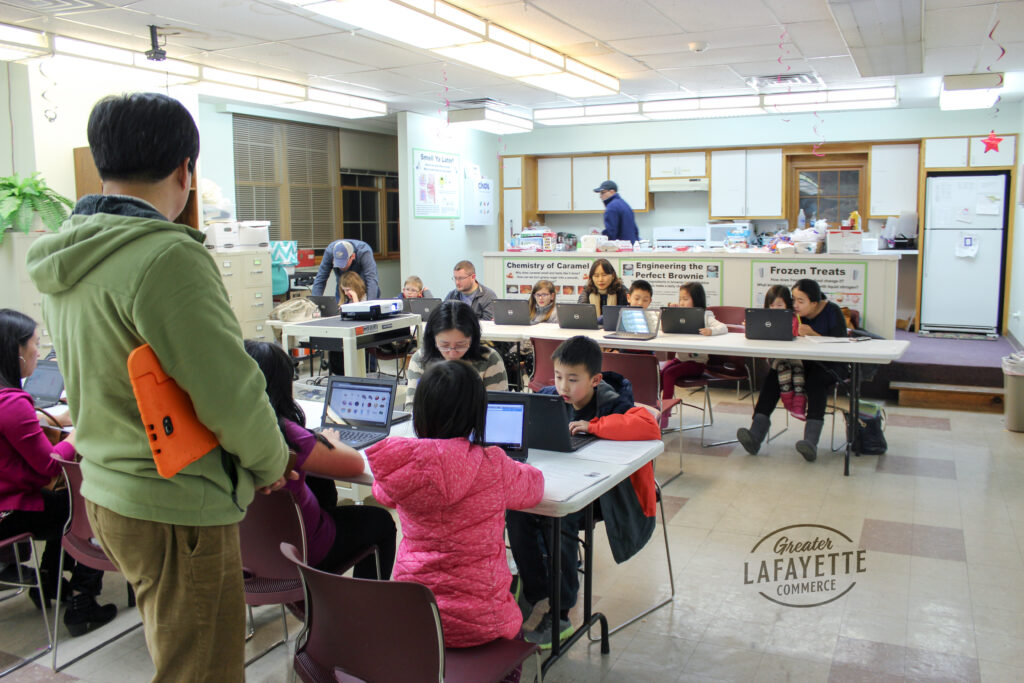
It takes partnerships with strong programs.
When COVID hit in 2020, Webb and the team of manufacturers flipped the Manufacturing Week program to a virtual experience. “It was a good idea for the time, but it wasn’t a great idea,” she said. “We put pressure on educators to find information here and there instead of presenting it in a concise format.”
To solve that problem, in 2021 Greater Lafayette Commerce partnered with Skyepack, a Lafayette tech startup, to create an online manufacturing education program. “It’s a beautiful product,” Webb said. The virtual program has evolved into Manufacturing Month, which is offered on a single digital platform. It contains activities, lessons, videos and content for educators to expose students at appropriate age levels to manufacturing careers.
Webb also built a partnership with Eleven Fifty Academy, an Indianapolis-based nonprofit code academy and coding bootcamp, to form local coding clubs. “We know coding is going to be really in demand, especially in manufacturing,” she said. “People will need to know coding and computer programming to work with robots and different technologies in manufacturing and logistics facilities.”
Later, she partnered with Brad Rhorer, chief talent programs officer at Conexus, who also served as workforce council chair for GLC, to take the tech angle a step further. “Brad challenged or our taskforce to marry Manufacturing Week with CoderDojo,” Webb said. The result? Incorporating CoderDojo’s community-based computer programming clubs into a free five-week summer camp for kids in five counties. “Kids go through five different technology stations, and one of those stations is manufacturing and industry,” Webb said.
It takes beginning with the end in mind.
Webb proudly explained that GLC’s workforce development programming aligns with 18 employability skills from the state of Indiana. They focus on stackable credentials, a sequence of credentials that can be accumulated over time and move learners along a career pathway or up a career ladder. Working closely with employers in manufacturing, GLC builds programs around those key skills.
For example, collaboration is an employability skill. Working closely with Primient, which produces food and industrial ingredients made from plant-based, renewable sources, Webb learned that the company’s interview process is really a teamwork interview. “If they’re hiring pools of people, they bring in a team of people, give them a project and see how they work through it. Then they critique them and give feedback, and then they give them a second project and see how well they work the second time through a project. So collaboration is one of the concepts we’re embedding,” she said.
This focus on stackable credentials and employability skills inspired Webb and the team to pursue the student learner recovery grant. The state’s $8.5 million investment in GLC’s programs proves they’re on the right track.
See What Could Be
Watch a video about Greater Lafayette’s Manufacturing Week and other K-12 programs.