Addman Engineering Leverages Manufacturing Readiness Grant to Secure Next Generation Metal Additive Manufacturing Equipment for Production
Addman Engineering
Case Study
Key Stats
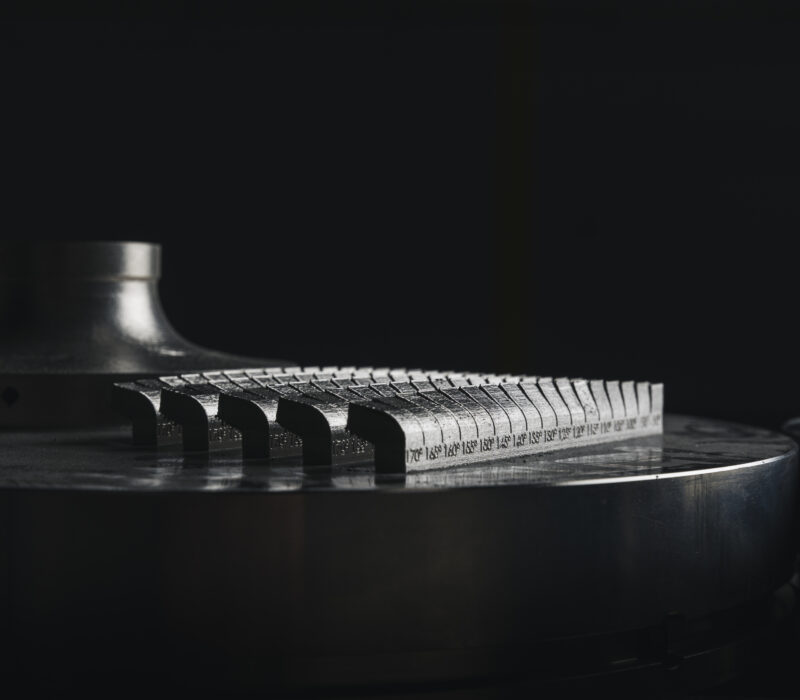
Company History
From a one-man start-up to leadership at a national corporation, Bob Markey oversees the Central Indiana plant that embraces cutting edge 3D printing technology.
Bob Markey founded 3rd Dimension in 2013 in what he describes as “the classic entrepreneur story: house on the line, family financing, brought in one machine and it was just me and that one machine for a while.” As that one-man company grew, Bob hired a lead engineer and the company kept growing and landing new clients. When it outgrew its initial small space in Indianapolis, Bob leased additional space. Soon 3rd Dimension spread beyond those 4,500 square feet and the plant moved to its current 27,000-square-foot facility in nearby Westfield.
In March 2021, 3rd Dimension was acquired by Addman Group, a division of American Industrial Partners headquartered in Bonita Springs, Florida, where its capacity, capability, expertise and customer base were a natural fit for Addman’s work with commercial space, defense, automotive and general industries. Today Bob is still on the job at the Westfield production facility, now as Executive Vice President of Addman Engineering.
3D printing pushes the art of the possible for part design, quality, and performance.
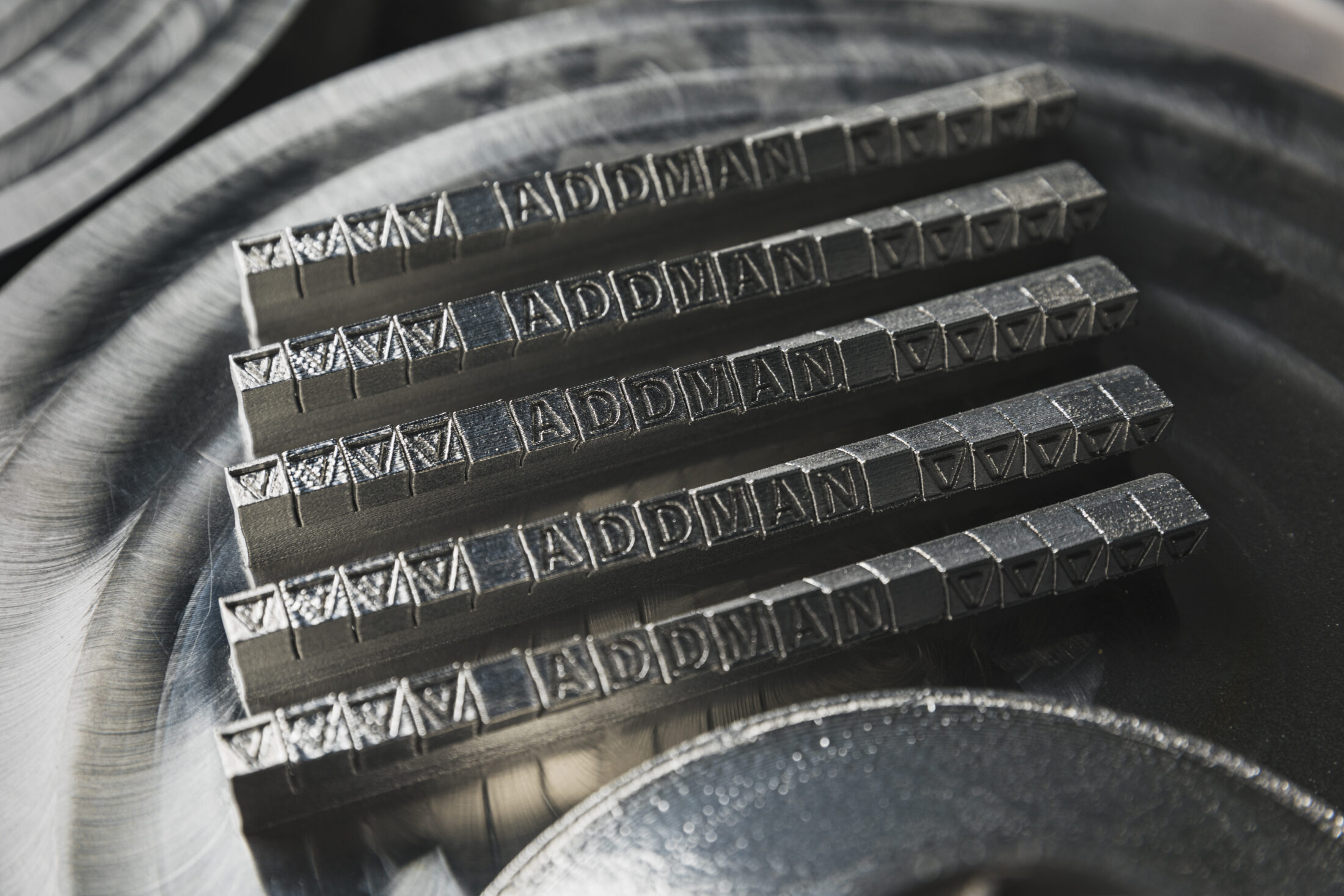
The company now uses additive manufacturing, or 3D printing, to produce high-end, complex metal parts for aerospace and defense, automotive, and other use cases. Additive manufacturing is very common for prototyping but using additive for production parts is not yet mainstream because it requires a great deal of expertise to operate a sophisticated, end-to-end additive process. Materials science, application engineering, design, material handling and environmental, health and safety expertise are needed to implement a complete and safe process. Putting one or more parts into full production via additive is no easy feat, and Addman is a national leader in this elite field of expertise.
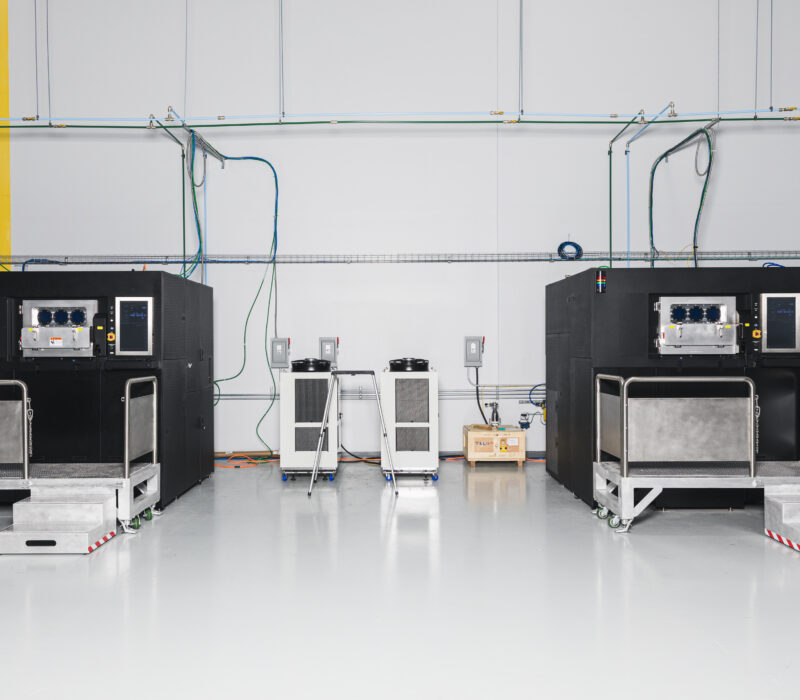
The Project
Addman invests in one of the most advanced 3D metal printers with next-gen quality control software.
Addman used the grant funding to purchase a VELO3D laser powder bed printer that came on-line in 2021 and can manufacture virtually any metal or polymer part, a move that company executives say “pushes the boundaries of possibility.” Simply put, the machine can manufacture parts that other machines can’t. The integrated AssureTM software builds on that by providing unparalleled quality control. The system improves value, produces large format tooling parts and components and minimizes lead times. Already it has been such a success, that Addman is planning to purchase two more.
“With this equipment, we can create parts out of metals including steel, nickel alloy, cobalt chrome, aluminum and stainless steel, among many others,” Bob said. “This isn’t just a matter of a local shop serving local customers. These are customers from well outside Indiana, and it’s some of the most complex and most high value parts. We’re now a very specialized shop serving global entities.”
Innovative and cutting-edge technology lures top talent.
The VELO3D printing equipment is a talent attractor, too. “We’ve put together creative and innovative culture and that is attracting the best engineers,” Bob said. Recent hires include an engineer from North Carolina and another from San Diego, California, with others interested in joining from Colorado and other states.
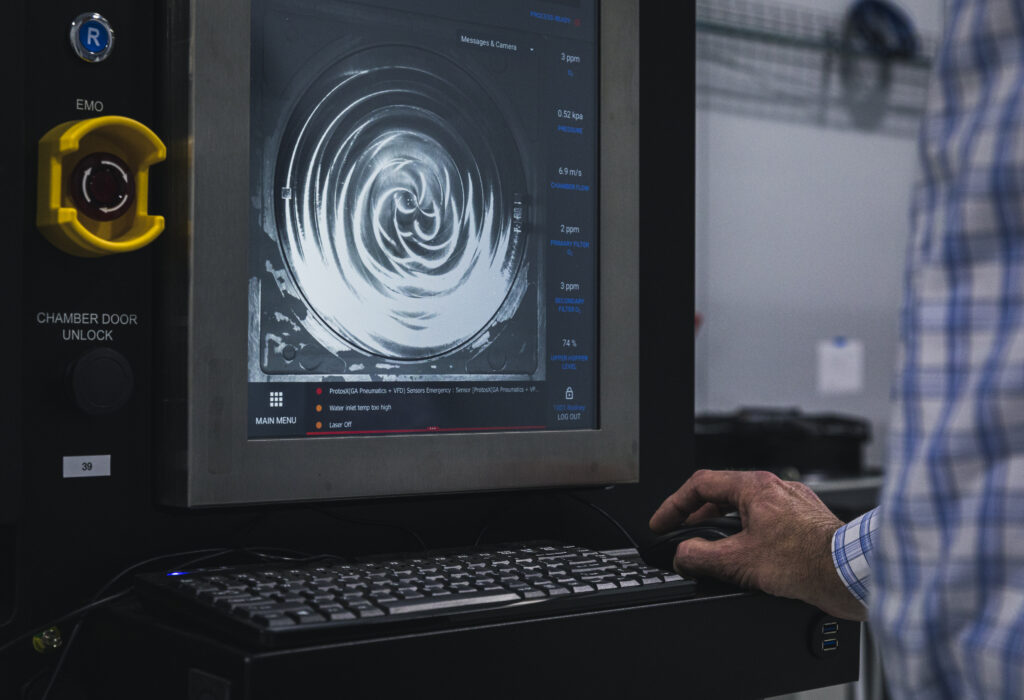
“It’s not just a one-off, either,” Bob said. “At the end of the day, it’s the latest and greatest, but there’s always going to be another one. You can’t outrun physics, and so we’re qualifying our oldest 3D printing machine from 2013. Parts coming off that machine will be involved in some of the next moon landings.”
“When those new customers and young professionals come to Indiana to see how we’re doing it, the impact reaches beyond the local community and Addman’s bottom line”, he added. It increases business for flights, rental cars, restaurants and other service providers, and it showcases Central Indiana to new audiences.
Manufacturing Readiness Grants (MRG) provided by the Indiana Economic Development Corporation and administered by Conexus Indiana are available to Indiana manufacturers willing to make capital investments to integrate smart technologies and processes that improve capacity. Addman Engineering was awarded grant funding to increase capacity and remain in the forefront of production grade, metal additive manufacturing solutions by investing in the latest and most innovative 3D printing technology.
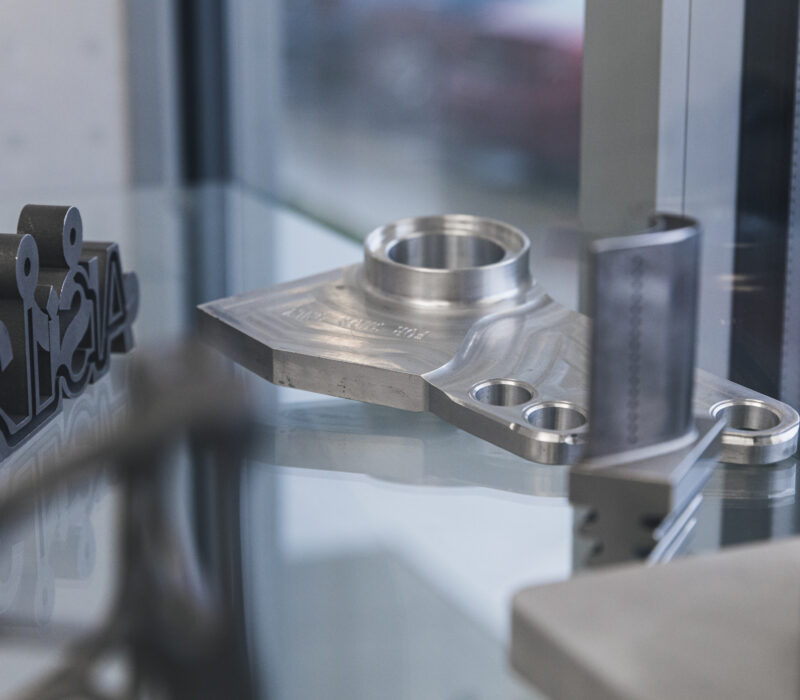
Key Learnings
Appreciate the unique opportunity in additive but don’t under-estimate the unknowns.
The real value of additive, he said, is when you start designing for it, you are “designing parts that can’t be made any other way and that approach really harnesses the power of what’s available.” He recalled a customer coming to Addman with a specific question: the customer said it had a part designed for additive and wanted to know the cost. “We looked at it and said it couldn’t be printed, but the customer insisted it was designed for additive. They were told it was.” But that’s not quite the way it works, Bob said.
“Additive is still an emerging technology, and almost everyone in the industry wants to lift all boats. We might not tell you all of the secrets, but we want to help those that are new to it.” When you’re considering a major capital expense in an emerging technology, “there’s always a risk that the business won’t materialize,” Bob advised. So, Addman seeks to intricately understand their customers’ needs before deciding if additive is the right route for a production part or component.
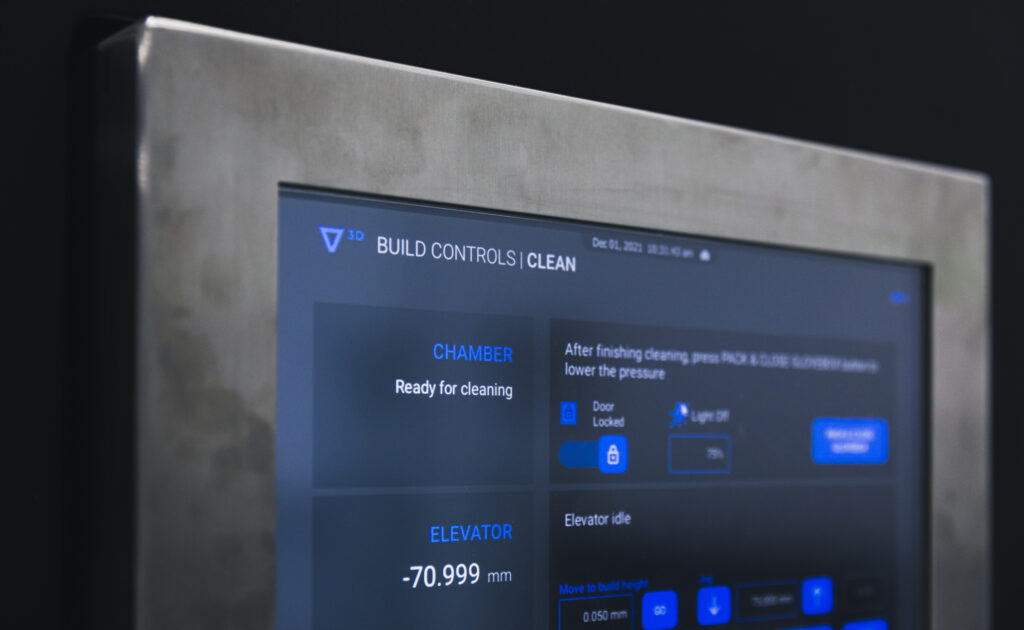
“On the metal side of things, we’re still working on specs, on proving that the material we say we’re getting is what we’re getting,” he shared. “We’re trying to understand the statistical significance and sharing our findings industry-wide. These new part geometries create many performance advantages, but also create some unknowns as the technology is still maturing. Hence, Bob’s team is not only working toward significantly improved part performance and quality but also obtaining new knowledge to build industry standards.
An end-to-end additive process for production parts brings together several areas of domain expertise under one roof, so collaborating with external partners is key to success.
Additive manufacturing reaches far beyond the engineering team. “When you implement 3D printing technology, you must purchase everything else that goes with it,” Bob shared. “And if you need to attract talent from outside Indiana, the engineers have to understand what they’re working with.”
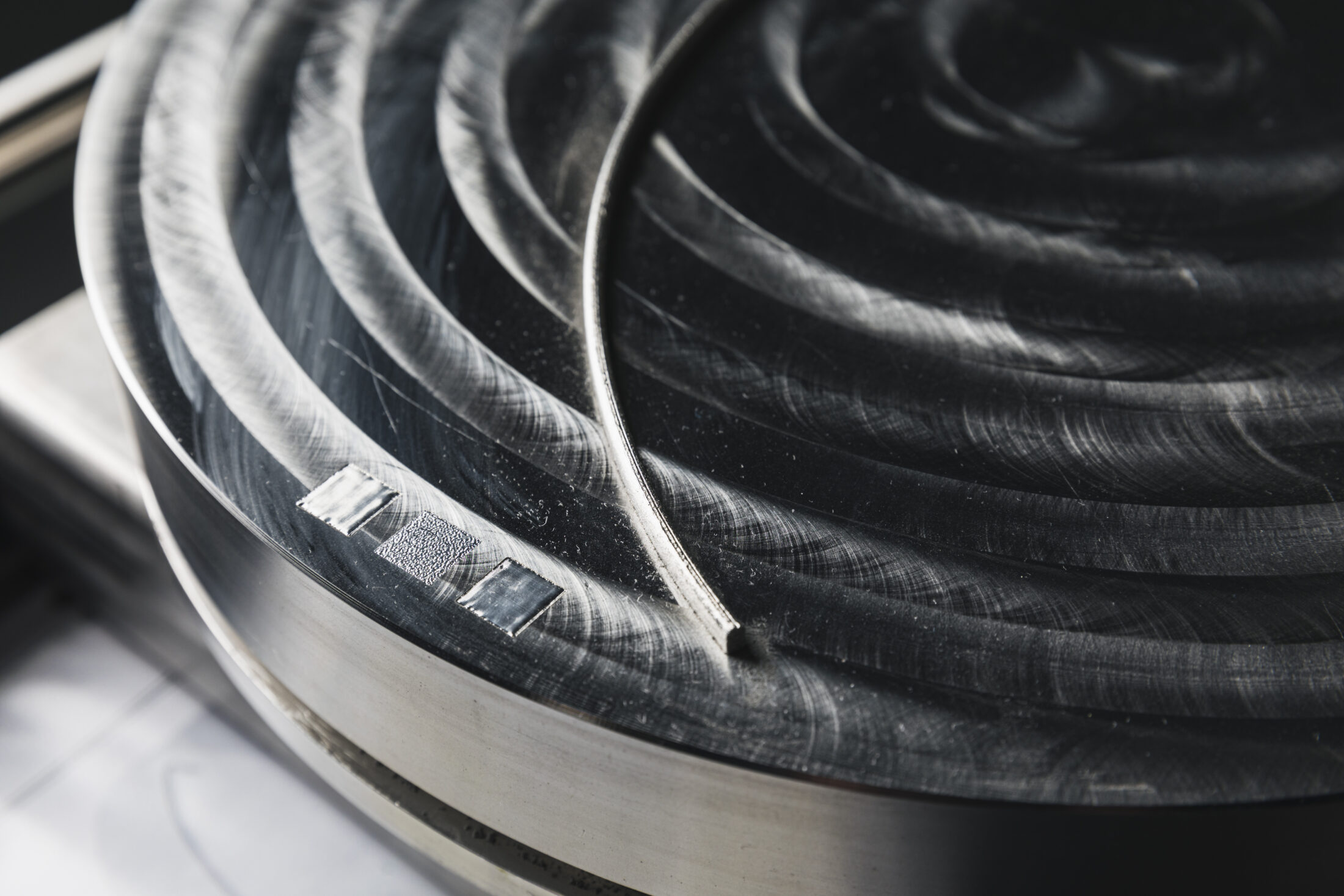
Luckily, the nuances pertaining to using metal powders are not exclusive to additive manufacturing. There are powder metallurgy parts, cold spray and thermal coatings, among other uses. “It’s relatively well understood from a health and safety aspect. We’re not unique in that regard,” Bob said, “but we have consultants that we work with on the safety side, and we work with community colleges, certification programs, and we definitely rely on Purdue MEP a lot.”
Take the opportunity to learn from experts and keep up with industry trends.
Another excellent way to collaborate with external partners is on the standardization of additive manufacturing processes. Manufacturers approach additive in unique ways, and processes are often industry-specific, therefore it’s crucial to be at the forefront of these ever-changing technologies and standards.
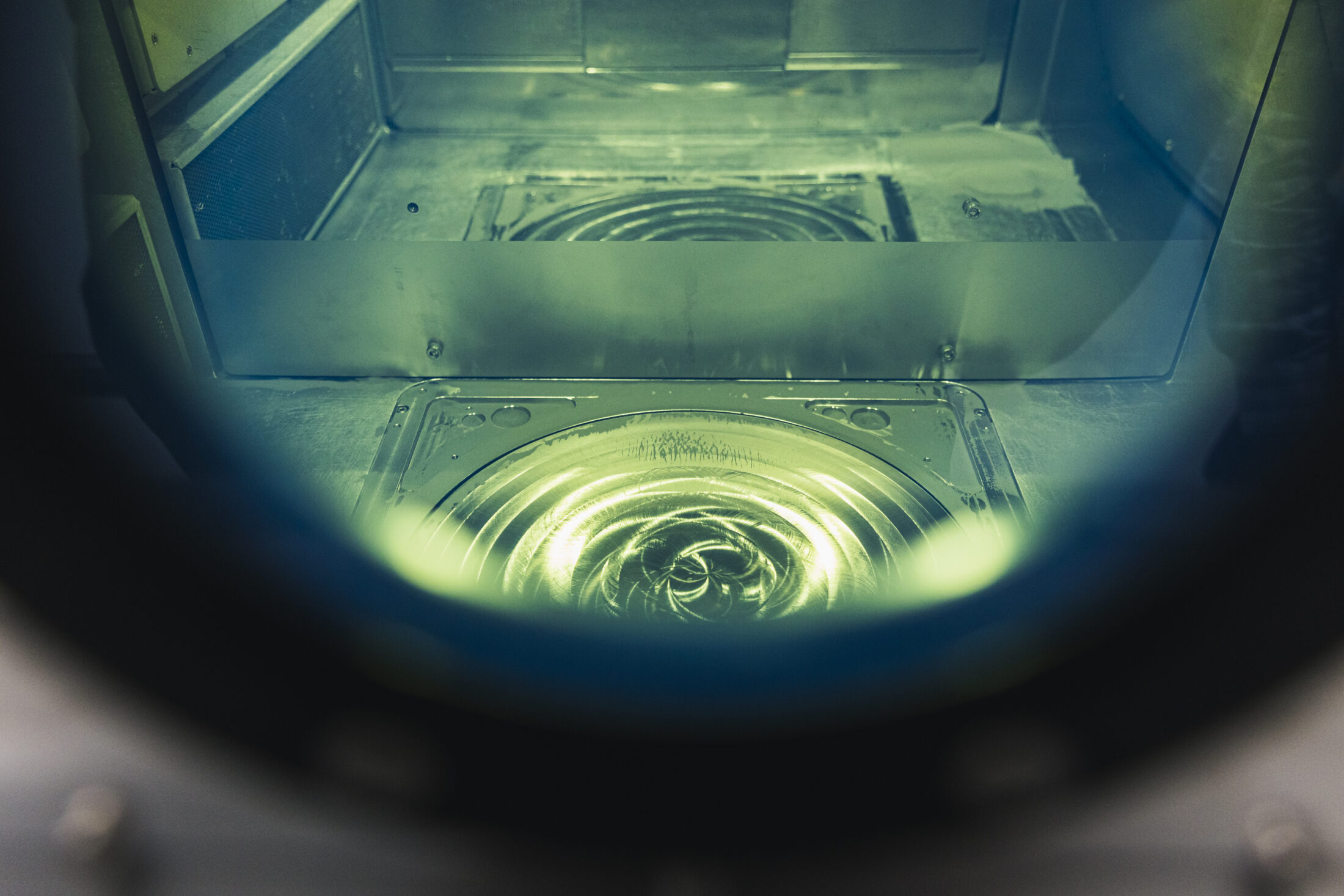
Bob recalls an instance when he attended a VELO road show in Jupiter, Florida. “There were a bunch of engineers from Siemens Energy, Lockhead Northrop,” he recalls, and a variety of half-hour presentations well worth attending.
“Stay aware of what’s happening in the industry,” Bob recommends. “Our facility in Florida is doing covers for firefighters’ tools. The pointy end might not justify the full cost of tooling, but it’s really needed. There are a lot of interesting use cases. There have been a ton of specs released over the past year, and you can jump on Zoom calls and discuss all the wording and what not. It really helps drive the industry forward. Plus there are a variety of new value propositions.”
“The real value of additive, is when you start designing for it… you are designing parts that can’t be made any other way and that approach really harnesses the power of what’s available.”
Bob Markley
EVP at Addman Engineering
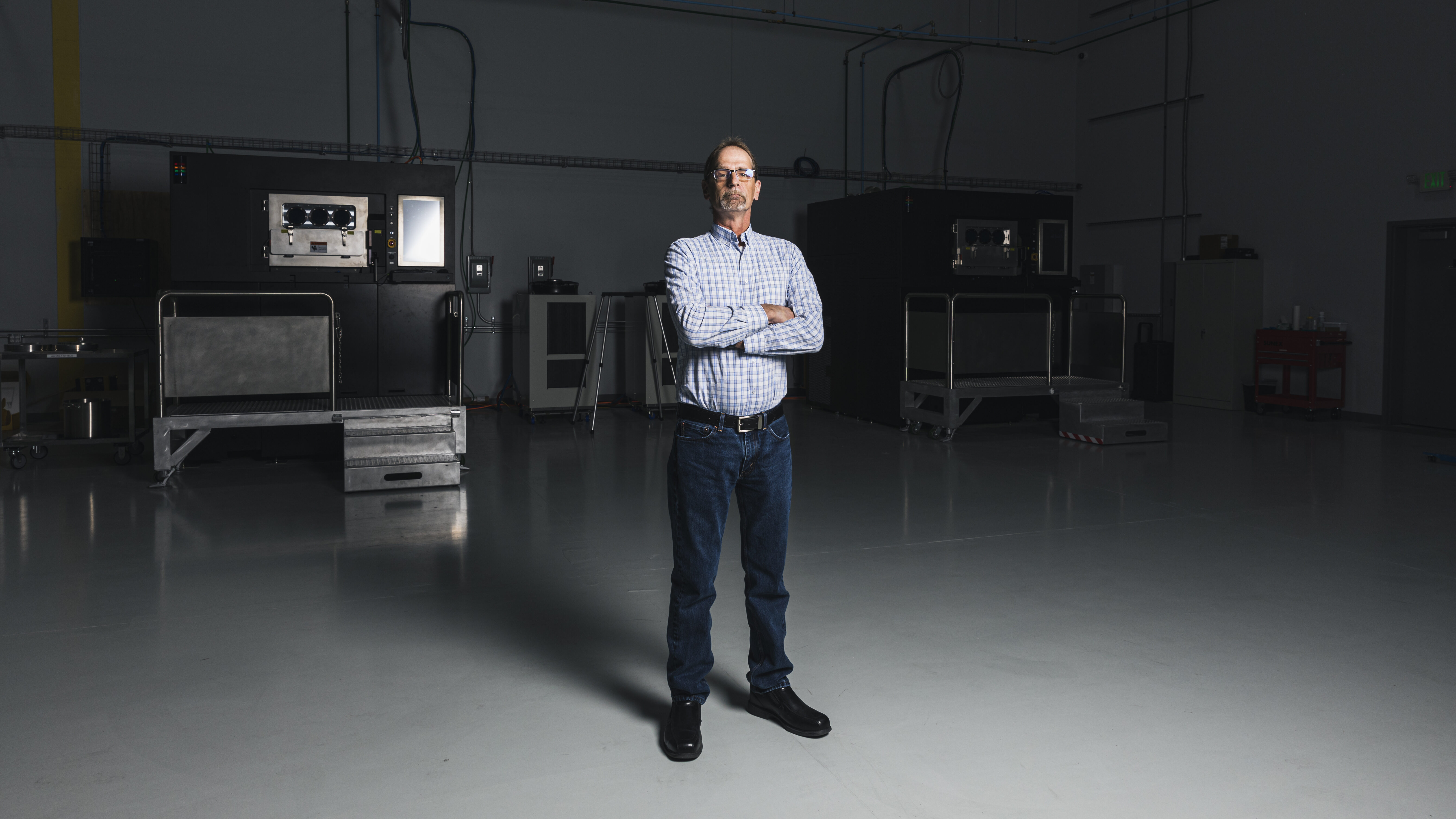