Hardtech manufacturer Copper Mountain Technologies expands product capabilities, enters new markets and makes a Moon landing with help from a Manufacturing Readiness Grant
Copper Mountain Technologies
Case Study
Key Stats
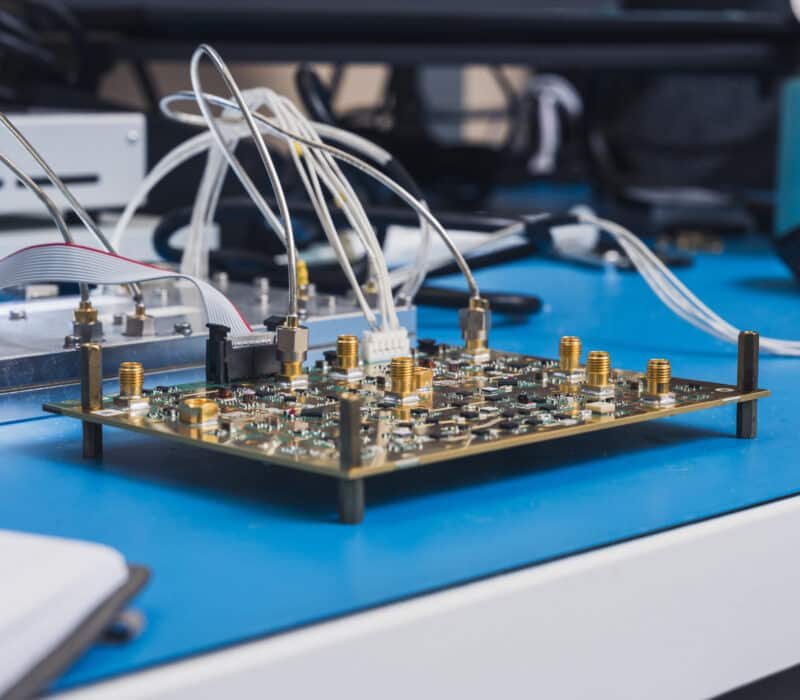
Company History
Copper Mountain Technologies is an Indianapolis-based hardtech business that has spearheaded the development and application of next-generation vector network analyzers.
In less than 15 years under the leadership of founders Irena Goloschokin as CEO and Alex Goloschokin as President, Copper Mountain Technologies’ (CMT) pioneering concepts in radio frequency (RF) testing and measurement equipment has grown into a successful enterprise with headquarters in downtown Indianapolis, a second location in Cyprus, and a worldwide customer base. Its line of vector network analyzers (VNAs) are used to test communication systems and components including antennas, mixers, filters, and more.
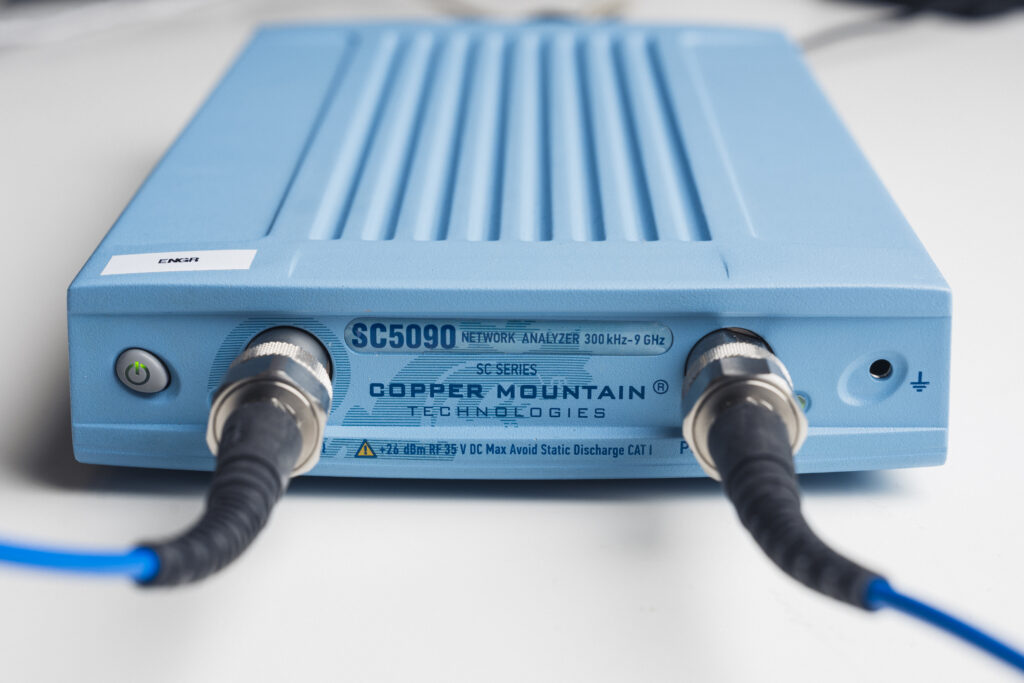
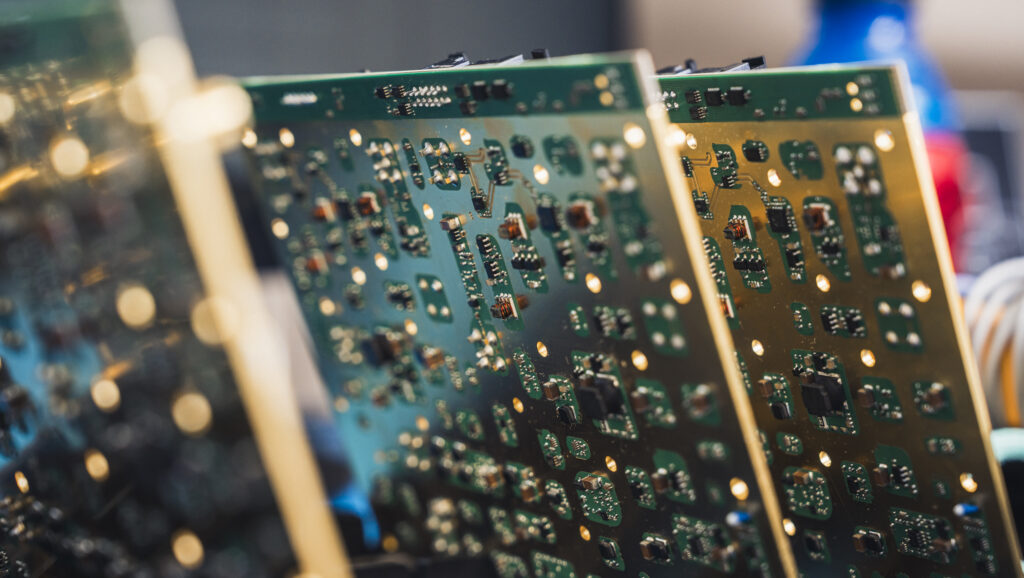
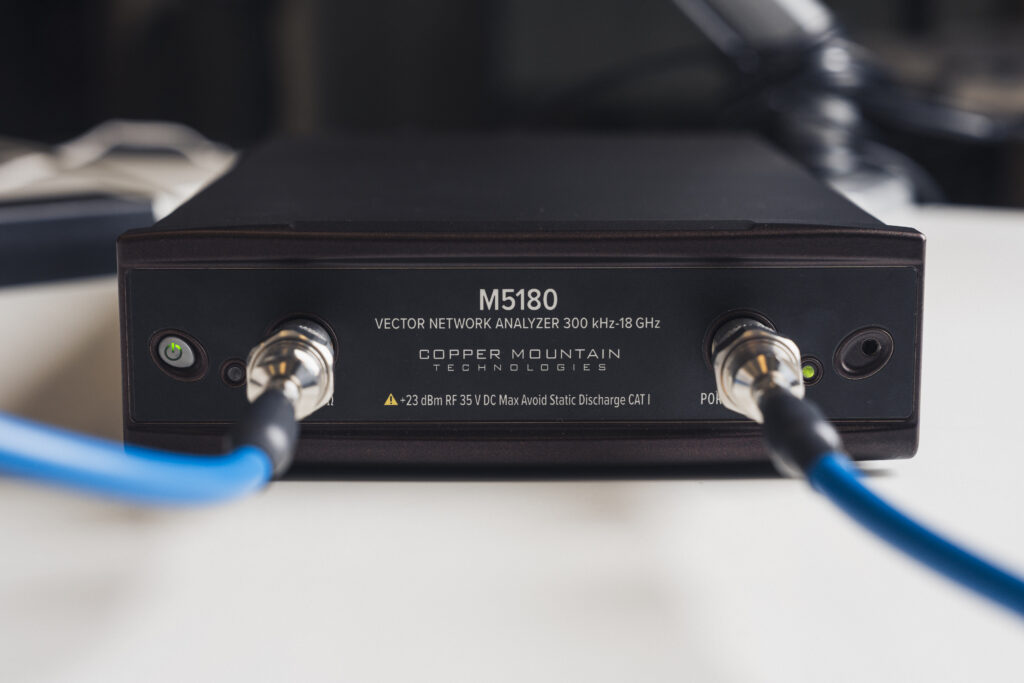
CMT’s primary development was hardware that offloads the required computing power from the analyzer to any external PC via a USB connection, allowing for an incredibly small form factor when compared to traditional analyzers that require significant benchtop space. “That was the innovation,” Irena explained. “Take the computer out, take the unnecessary cost and complexity out, and separate the measurement module from the processing module, which is a proprietary software application run on any external computer. The USB-based analyzer creates smaller, more affordable and versatile equipment accessible to a wider range of functions and customers.”
Irena shared the example of a system unique to NASA, employed on the Intuitive Machines Nova-C Lunar Lander. The agency leveraged one of Copper Mountain Technologies’ analyzers to measure the lunar lander’s liquid oxygen and methane levels in propellant tanks while en route to the moon. To determine fuel levels, the analyzer is installed inside of the tank where it first emits a known RF signal. It then receives a reflected signal that is altered by the fuel’s physical properties and distribution inside of the fuel tank. By comparing the known signal to the reflected signal, the analyzer can translate these two signals into fuel quantity. CMT’s analyzer, along with the rest of the lunar lander, successfully landed on the Moon in February 2024. “It took seven or eight years of testing, checking and retesting on Earth before it flew, but it did,” said Irena. Since the mission’s success, NASA has produced a paper and presentation explaining the analyzer’s operations, validating its use case and opening the doors for future applications.

Content: Slide 4 of NASA Document ID 20240015965
The agency leveraged one of Copper Mountain’s analyzers to measure the lunar lander’s liquid oxygen and methane levels in propellant tanks while en route to the moon. To determine fuel levels, the analyzer is installed inside of the tank where it first emits a known RF signal. It then receives a reflected signal that is altered by the fuel’s physical properties and distribution inside of the fuel tank. By comparing the known signal to the reflected signal, the analyzer can translate these two signals into fuel quantity. CMT’s analyzer, along with the rest of the lunar lander, successfully landed on the Moon in February 2024. “It took seven or eight years of testing, checking and retesting on Earth before it flew, but it did,” said Irena. Since the mission’s success, NASA has produced a paper and presentation explaining the analyzer’s operations, validating its use case and opening the doors for future applications.
Moving into its 2nd decade, CMT is focused on expanding its customer base and supplier relationships to remain at the forefront of the industry. An industry trend of moving into higher and higher frequency testing has not gone unnoticed and CMT is also preparing to support their customer’s needs in this space.
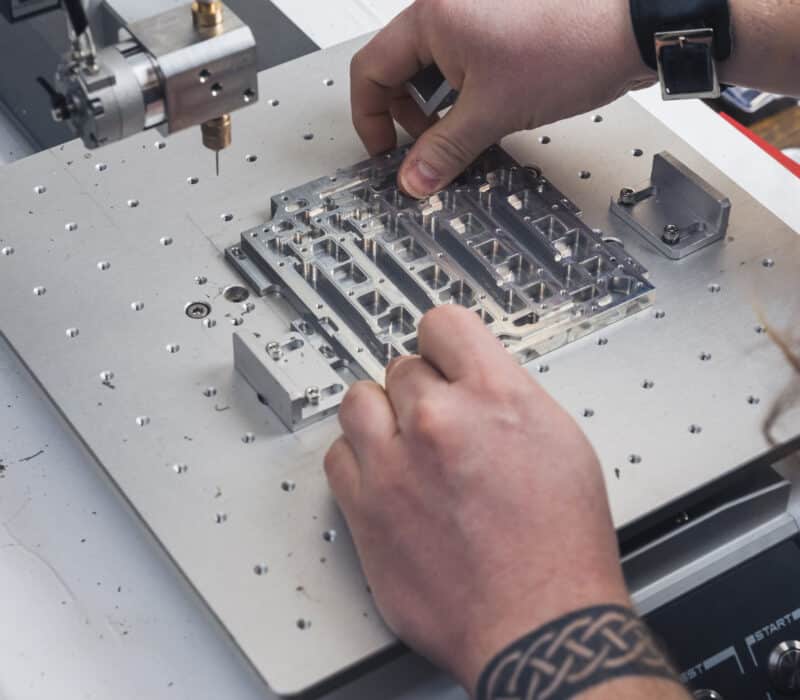
The Project
Copper Mountain Technologies’ competitive advantage necessitated an ability to perform more manufacturing in-house and form close partnerships with regional service providers.
“In business school, they say you need a competitive position; for some it’s price, for others, it’s new tech,” Irena said. “When we started, our competitive position was new tech. We were the only ones who had a vector network analyzer in this form factor. It took seven years for our largest competitor — a global company — to come out with their own USB analyzer.” The ability to rely primarily on CMT’s own team as opposed to offshore contract manufacturing helped to gain an additional competitive advantage in the industry. “That allows us to be more responsive and more flexible in meeting the needs of our customers.” Irena explained. “We take the traditionally built-in computer out, eliminating unnecessary cost and complexity. We focus on the measurement module and combine that with metrology-grade software that runs on a PC.” CMT’s instruments can work in conjunction with a single board PC, making it much easier for RF engineers to perform traditional network analyzer tests. “Because it’s so much smaller and doesn’t have the computer and computer peripherals inside, it opens up a number of applications that were not possible with a big, bulky bench-top instrument.”
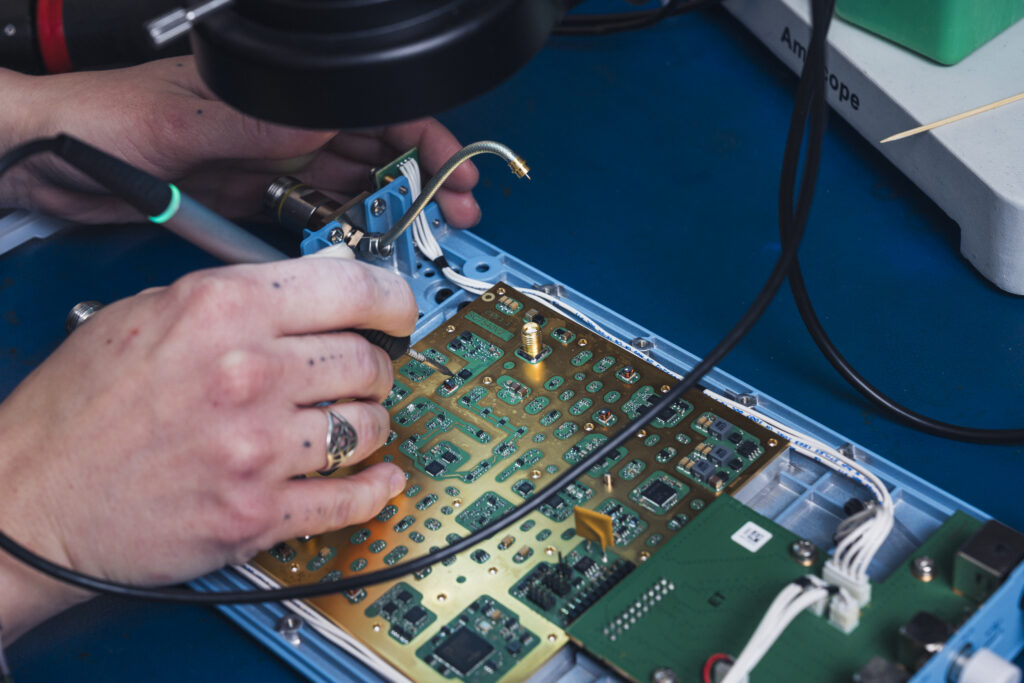
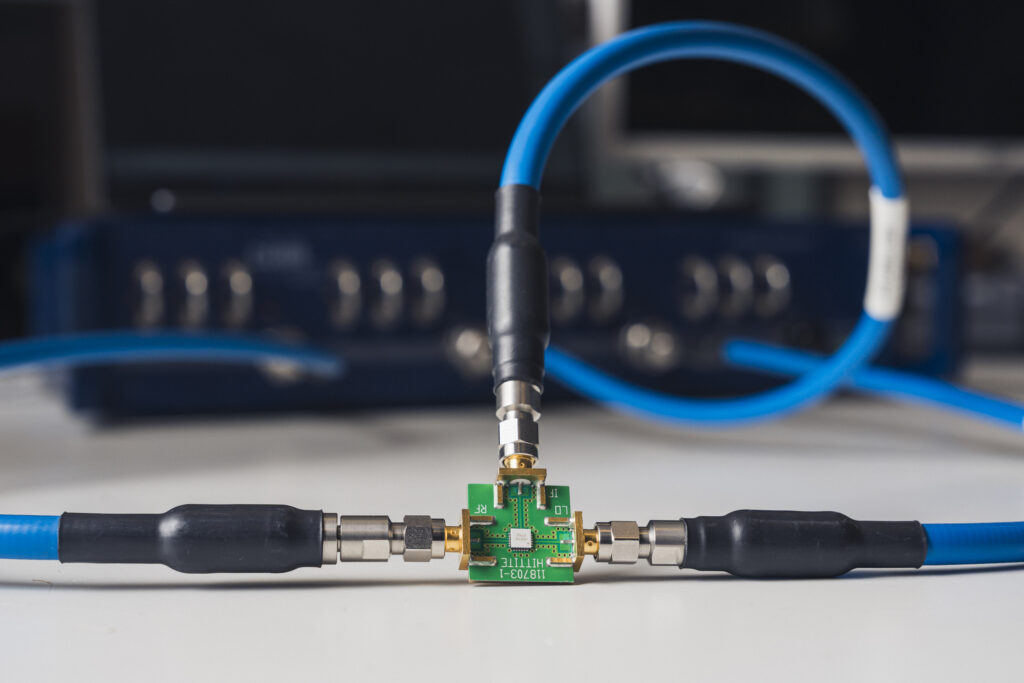
“Our typical customers are radio frequency component and system manufacturers,” Irena explained. “They’re communications companies, aerospace and defense. We have even seen applications in the medical industry. One customer built a breast cancer detection system around our instrument using RF imaging instead of the typical mammogram x-ray signal. Other customers use it to measure moisture in soil, in fruit, in other agricultural substances.”
Irena also mentioned a gold mine in Burkina Faso that contacted CMT looking for a solution to test the weld integrity of plastic pipes. “Our applications engineers recalled that one of our customers offers this type of testing using our analyzers. “We reached out to this customer and connected them with the goldmine in Burkina Faso. We hope they will be able to meet the mine’s needs, and we hope we can sell some analyzers in the process.” A major component of Industry 4.0 is mass customization; for Copper Mountain Technologies, customizing a complicated product like a vector network analyzer and adapting it for new use cases has cast a light on several new business opportunities. “We focus on the customer experience first and foremost,” Irena acknowledged. “The analyzer works the way the analyzer works. But we make a difference by offering a significantly smaller form factor. That’s the direction we’re going as a company. The capability to be flexible and do things our customers need is where we need to be.”
The instrument’s ability to function as an easily integrated, multipurpose sensor separates Copper Mountain Technologies’ product offerings from traditional network analyzer suppliers.
With the VNA’s vast potential in a variety of industries and use cases, CMT is developing more and more projects that assist customers by tweaking its off-the-shelf analyzer to satisfy unique and specialized applications. Developing a different connector or housing, adjusting the frequency range, or some other alteration is now a critical function for CMT’s business. To best meet current and future customer needs, they made the strategic decision to bring small volume production runs in house, leveraging an MRG award to support new equipment acquisition. This equipment centers around advanced printed circuit board (PCB) assembly equipment – including a thermal shock digital bench oven, a laser marking machine to easily identify and follow PCBs through the full manufacturing cycle, and an automated electromagnetic interference shield dispenser. “One of the things we’re doing with the added equipment is increasing our ability to move more quickly and bring some of those important processes in house,” Irena said. “The EMI shielding is very important for the accuracy of our measurements. This shielding material is found in virtually all our products,” Irena explained. “If this is not done correctly, the instrument will not deliver the accuracy and performance we specify.”
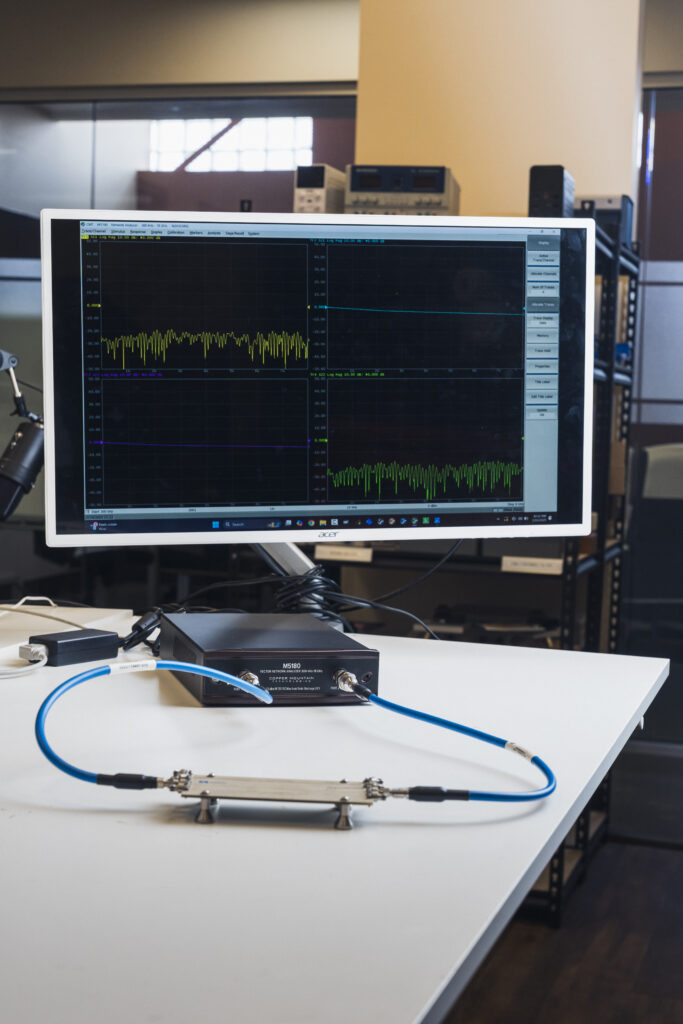
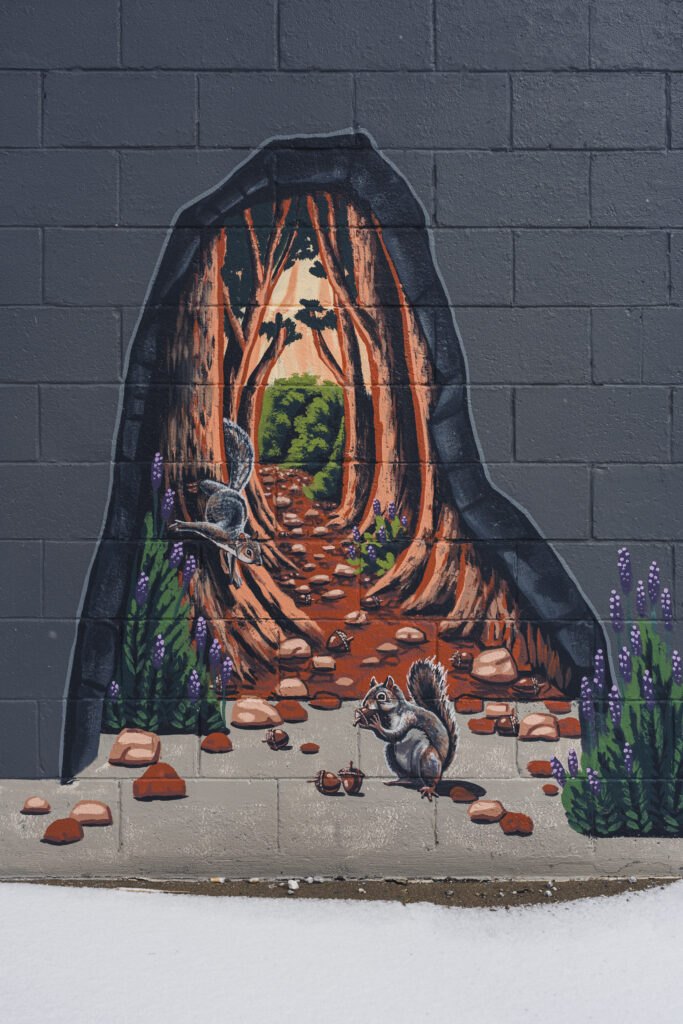
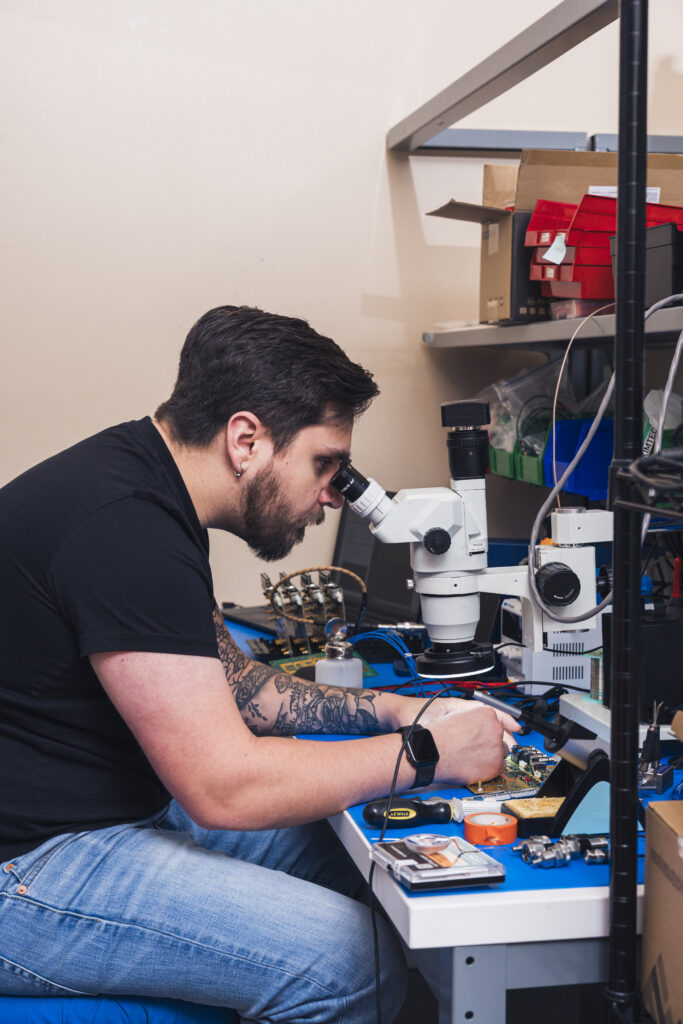
Bringing its manufacturing to Indiana benefitted more than just CMT’s operations – the company has engaged several local partners to assist in production. “It’s easier to talk to a partner and explain to them when we’re at the same table. We focused on Indiana when searching for those partners,” Irena said. Among them, she named Divsys, a branch of ICAPE Group for PCB fabrication and assembly; Stephen Gould in Whitestown for high-quality packaging to protect the sensitive measurement instruments while enhancing aesthetic appeal; Estes Design and Maintenance for sheet metal fabrication for analyzer housings; LaserScribe for laser engraving services; and Eagle Magnetic company in Crawfordsville, for powder coating services. “The more we can do ourselves and with local partners that are close, the better we can manage these customization projects and the more capabilities we can offer to a customer.”
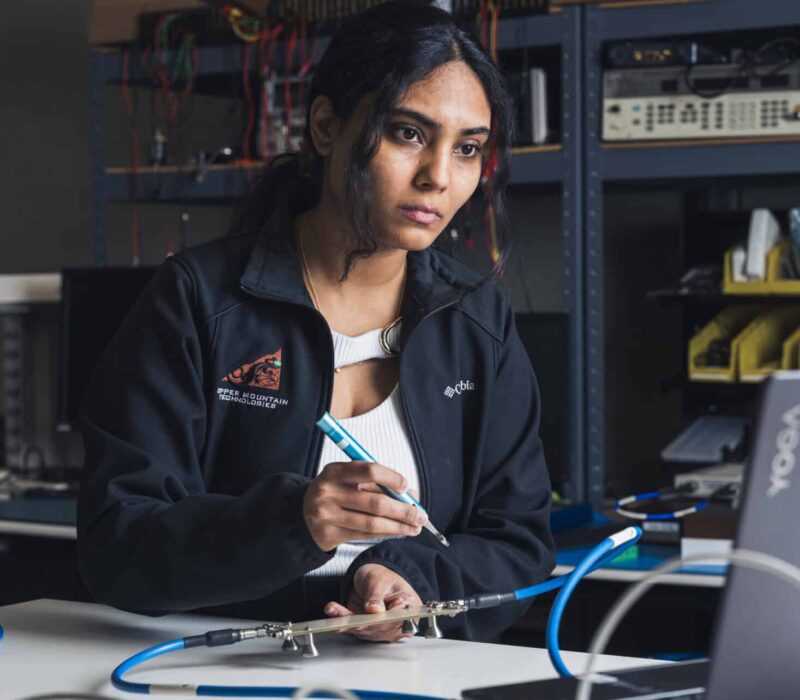
Workforce Implications
For CMT, technical expertise, internal drive and intellectual curiosity is a workforce must-have.
The company has hired 8 new employees since receiving the MRG award — all in their Central Indiana location. “We do difficult things in pretty much every part of the company, from design to support to repair to production to applications engineering,” Irena said. “We look for people who are interested in solving difficult problems and helping customers.” In fact, she joked, most CMT engineers “actually like talking to people, which is unusual.”
The production team contains experienced and skilled electronics technicians with expertise in assembly and repair soldering. “Working with surface mount technology (SMT) components, the majority of what they do is done with a microscope, because it requires a very high level of precision.” She gives a nod to associate graduates from Ivy Tech’s electronic programs. “We wish there were more of them. It’s a great program,” she said. “We also do a lot of training on the job. And we’re very fortunate that most people, when they come, they stay.” Irena pointed to a shortage of RF engineers in the U.S., particularly in mid-career levels, explaining that most of the applications engineers at CMT are in their 20s. “Currently, the engineering team lead is 29,” she said. “He’s the most experienced person on that team, and he’s been with us for 6 years. In that time, he’s seen just about any sort of network analyzer application there is.” In the early years of the 21st Century, computer programming and software engineering became a popular career choice, siphoning many students from a more hardware-focused career path. “People just didn’t go into hardtech, so there are not enough of them at mid-career levels now,” she added. “Even now, there are just not that many kids in high school choosing to go be hardware engineers.” Most of the engineers applying at CMT are from Indiana’s own Purdue, Rose-Hulman, as well as South Florida University, Moorhead College and other out-of-state schools.
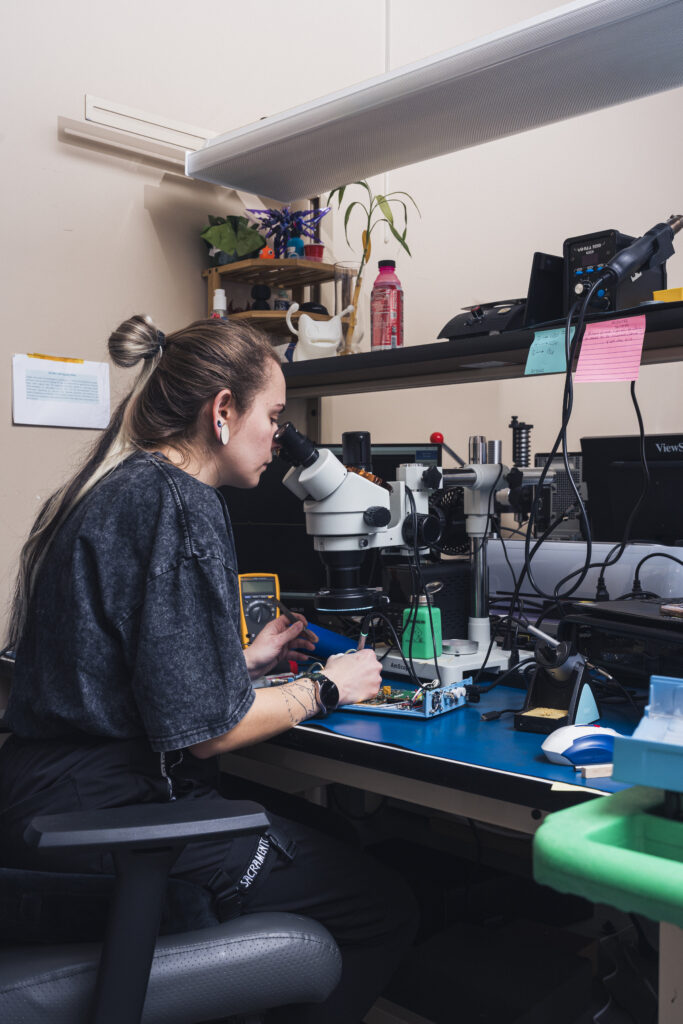
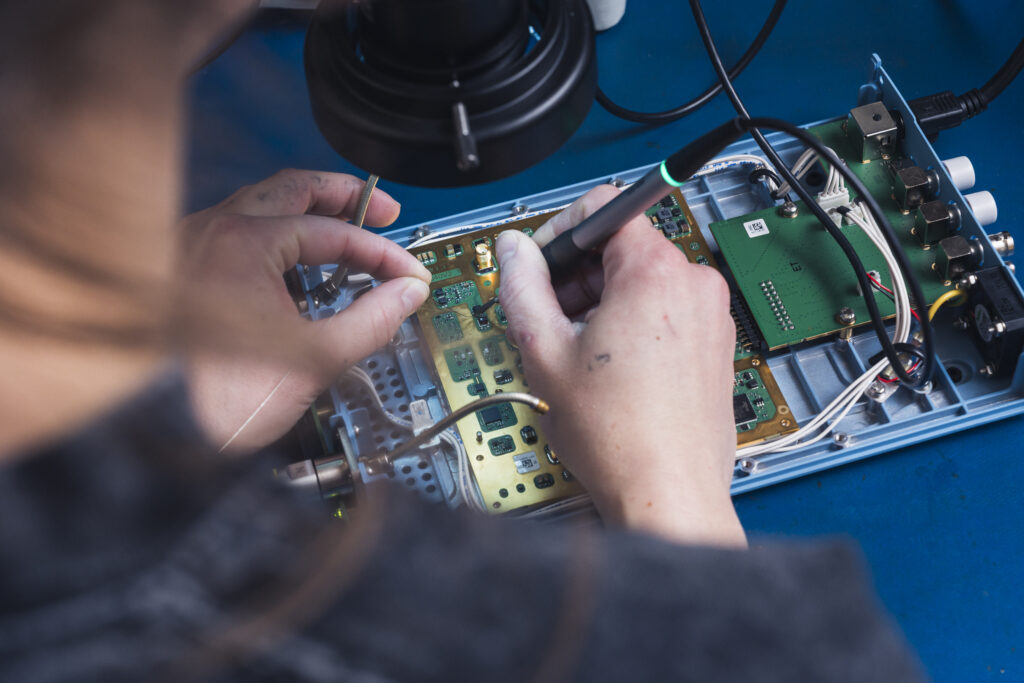
Despite these challenges, CMT has found success in supplementing new engineer experience with in-house education. She recalled that in CMT’s early history, the company was looking for an applications engineer. One individual applied who had more than 40 years of engineering experience and liked to teach. He joined the company in 2018. “His name is Brian Walker, and he pretty much taught all the younger engineers who are here now how to do applications assistance for our customers. It’s essentially his own master class inside the company. Outside the company he is very well known in the industry for hosting master classes on specific parts of vector network analysis and RF designs. Sometimes you just get lucky.”
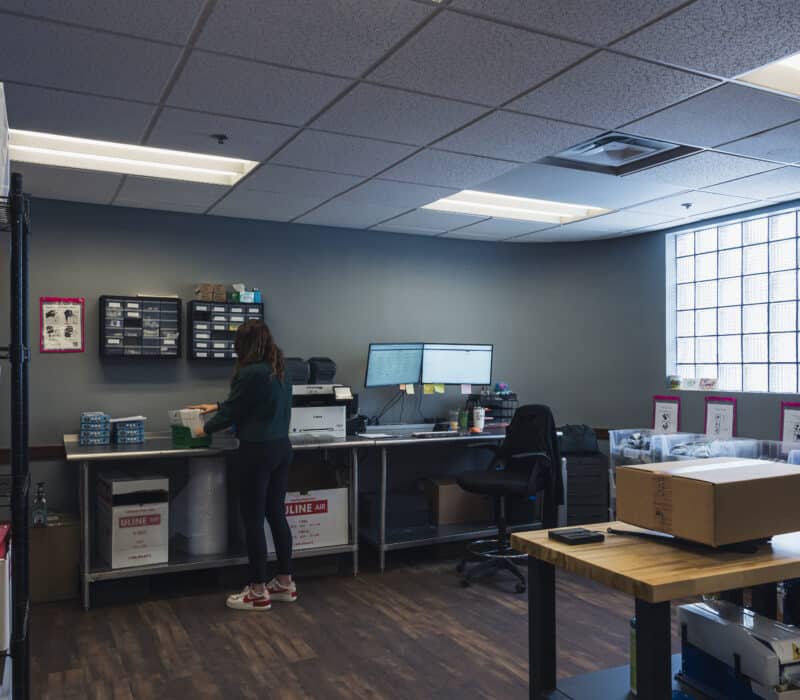
Shared Learnings
Companies interested in obtaining a Manufacturing Readiness Grant need to be alert to requirements, opportunities and closing dates.
“You have to be ready,” said CMT Operations Manager Ekaterina Rico-Castillo, who was responsible for writing CMT’s grant application form. “The application process is straightforward. I wouldn’t say it’s easy, but I understood what I needed to do and did my homework. My team wanted to get it done and we put it all on paper.” The MRG program is popular, and even with $20 million in funding allocated over the past two fiscal years, high-quality applications from Indiana manufacturers add up quickly.
One thing Irena and Ekaterina agreed would be helpful for hardtech entrepreneurs would be a shared resource space with serious equipment dedicated to hardware and electrical manufacturing. While some spaces like this do exist, most don’t have the level of tools and machines that hardtech entrepreneurs need to genuinely explore prototypes and enter production. “The required machine may cost half a million dollars, and you only need it 2 days a month and require 2 people able to operate it. How do we get enough of us together to justify a serious coworking space for hardtech that gets into the electronics and high frequency component base and the semiconductors, etc.?”
Building on the success of this relatively smaller MRG project, Copper Mountain Technologies is actively thinking about future MRG projects to transform their operations. “I do have a list of ideas,” Ekaterina said. “We’re thinking about writing another application and are watching the Conexus website for any announcements on future program funding. We recognize it’s a competitive grant process, and we want to be sure we have all our planning and details in place to complete a successful application.”
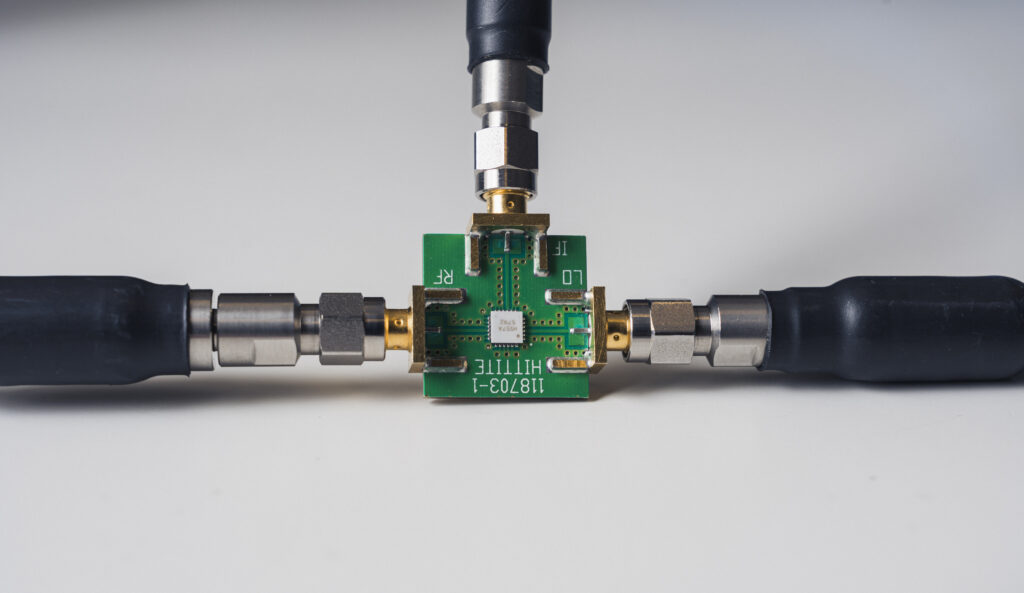
“We focus on the customer experience first and foremost. That’s the direction we’re going as a company. The capability to be flexible and do things our customers need is where we need to be.”
Irena Goloschokin
CEO of Copper Mountain Technologies
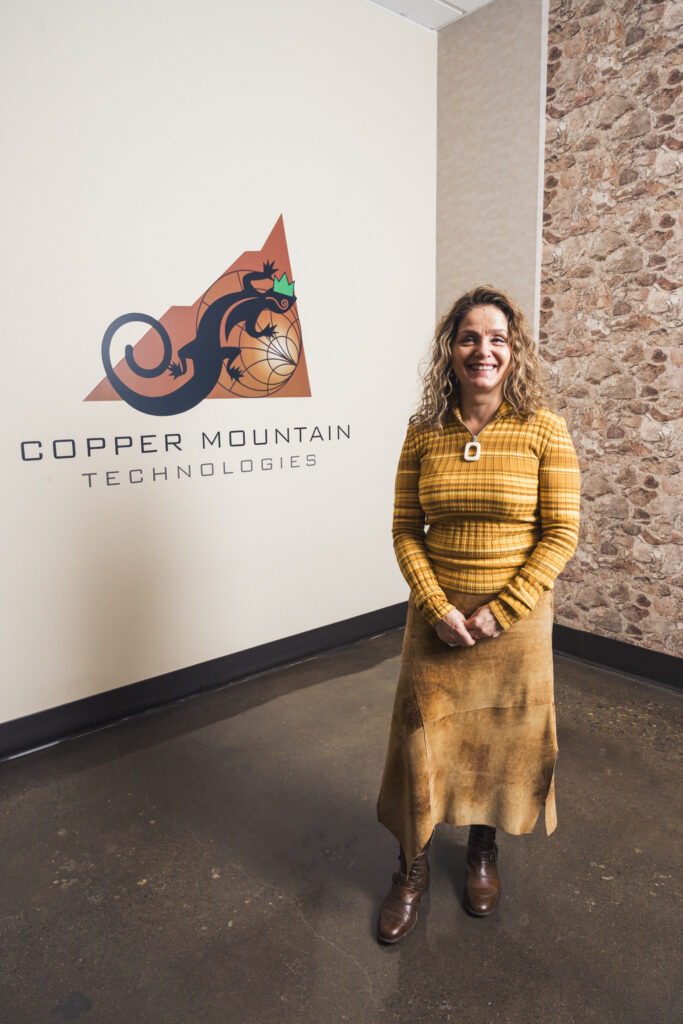