Fred Smith Store Fixtures Adds to its Smart Manufacturing Capabilities to Expand Product Offerings at its Corydon, Indiana Facility
Fred Smith Store Fixtures
Case Study
Key Stats
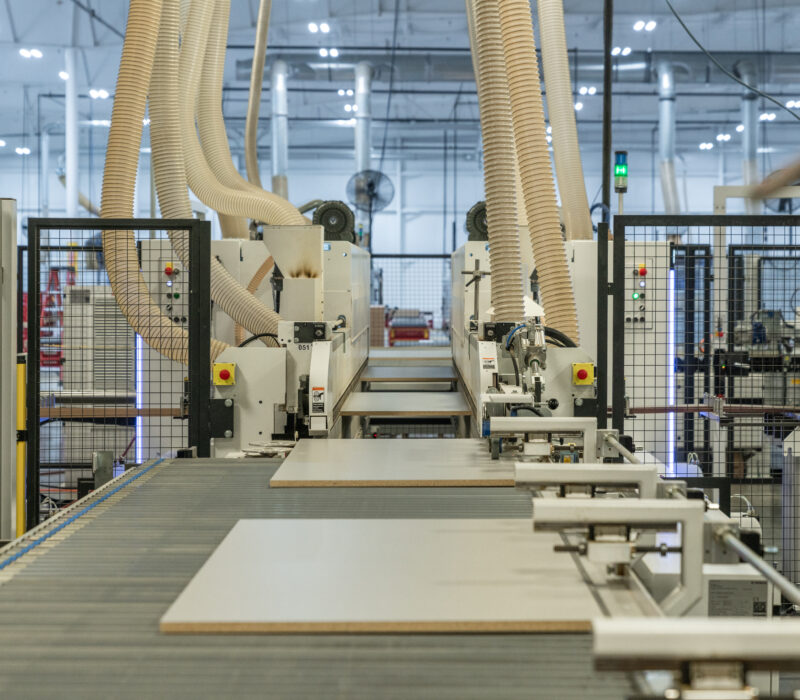
Company History
Fred Smith Store Fixtures began in Depauw, Ind., in 1963; today the company has expanded to include a second manufacturing facility in nearby Corydon with almost 150 employees.
When Fred and Laura Smith decided to capitalize on Fred’s woodworking expertise, the couple built a small shop behind their home in tiny Depauw, Ind., a community of fewer than 120 residents situated in Harrison County along the Ohio River, and founded Fred Smith Store Fixtures (FSSF). Jon Smith, the founders’ grandson and FSSF human resources director, said the company at first was focused on custom woodworking jobs. “They started with 10 to 12 employees, and a lot of them were family members,” he said. The new company made its reputation doing jobs for area businesses such as trim work at Hanover College, while building custom bars for local restaurants, storage units for commercial and school customers and retail store fixtures. When co-founder Fred Smith died in 1979, his widow (Laura Smith) and their son, Steve (Jon’s father), took the reins.
In the 1980s, under Steve’s leadership, the company changed focus to hospitality and office furniture. In 2016 FSSF opened its second plant in nearby Corydon, where the company is now heavily invested in creating custom laminate for shelving, countertops, storage and other products for schools, offices and the hospitality industry (hotels and motels). As FSSF General Manager, Dusty Rhodes explained, the company’s major product line manufactures flat surfaces to be used in other products, such as conference tables or countertops. “Our customer takes that flat piece and adds other elements to complete the unit. You’ll see a lot of the products we make in hotels and motels, but they will never have our name on them. We’re just the intermediary.”
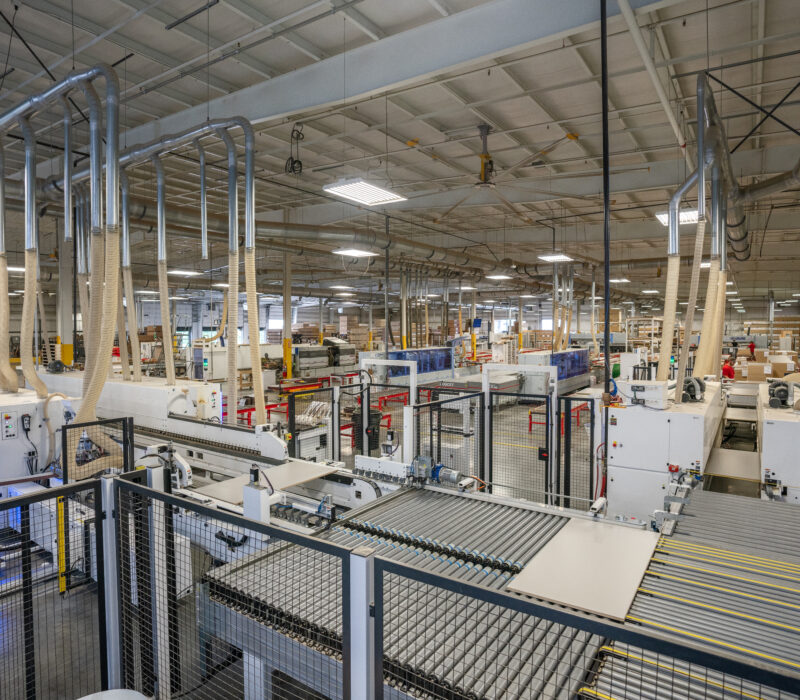
The Project
FSSF purchased a next-generation machine to improve production efficiency and grow with its new business, specifically within the hotel/motel industry.
Decorative additions to flat surface laminate were the reason for adding new manufacturing capabilities with next-generation machine. “Our largest customers have a stocking program for very specific colors and designs that are proprietary to them,” said Dusty. “There may be 6 to 9 variations of each inventory that we manage. The customer can call us and say they want this color in this finish, and the order is very specific to their designers. We have these colors in stock all the time, but a particular combination may be something we’ve never seen before.” As an example, he said, FSSF stocks as many as 7 different “whites” that a customer may incorporate in a specific order. Therein lies the value of the next-generation machine designed and purchased with the help of the Manufacturing Readiness Grants.”
The purpose of the project was to help FSSF find—or create—a machine that would improve production efficiency, ergonomics and the finished quality of the product. Most important, Dusty shared, was to improve the throughput creating growth at the Corydon facility where the project is located. “I always say ‘success is based on expectation,’” he said. “When the Corydon plant was opened in 2016, we had 1 person. Then we had 2, and 3, and 5. Now we’re up to 29, with some part-timers. What we’ve done is make this a specialized plant for the hotel/motel industry, and that industry is growing.”
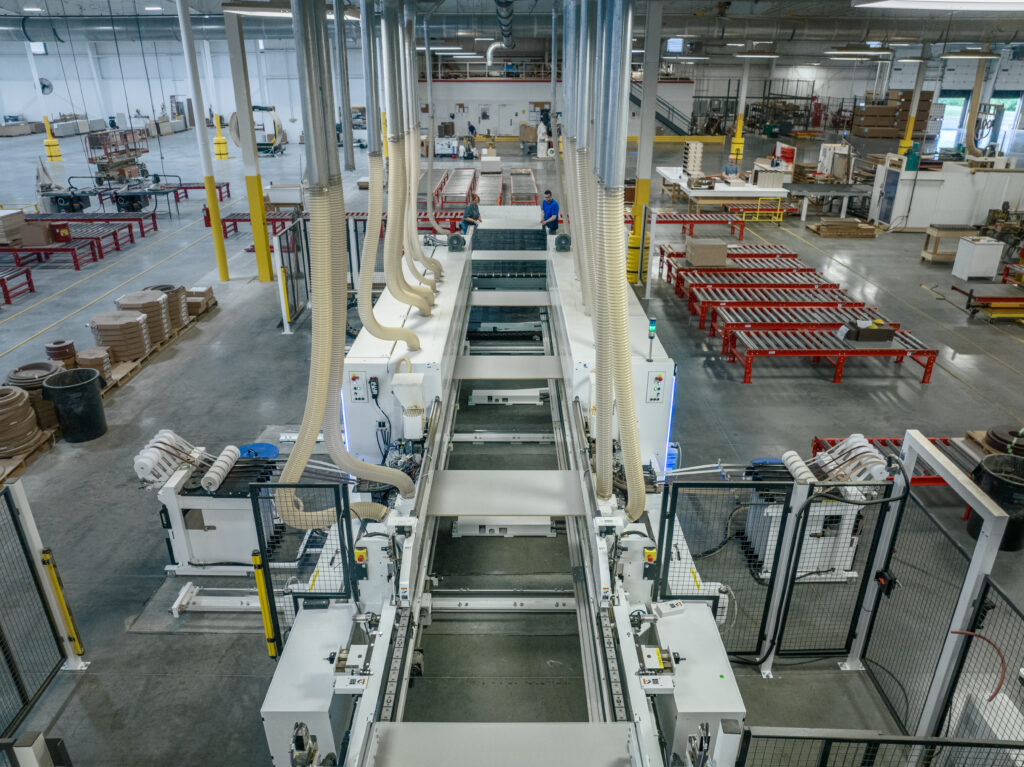
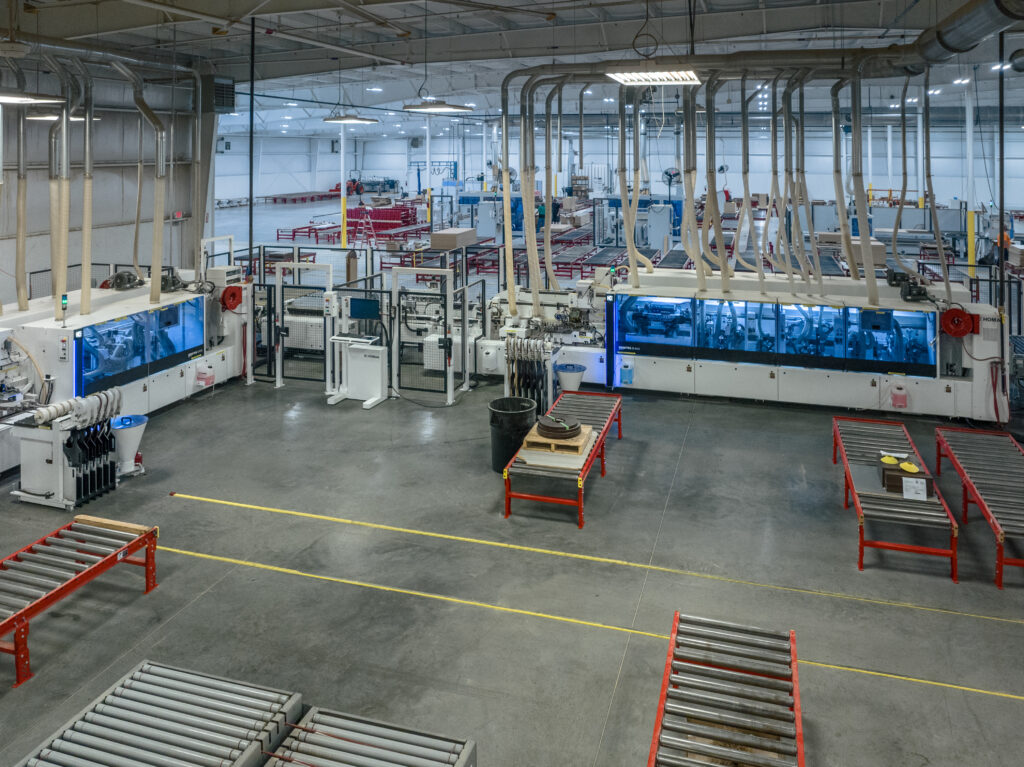
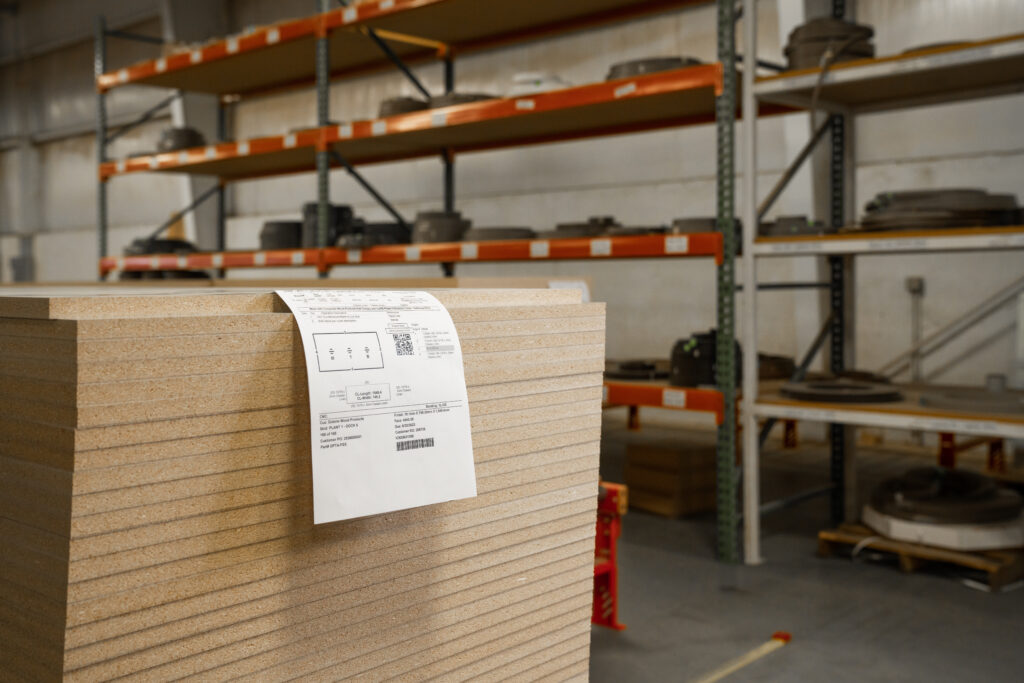
Before the next-gen machine was on-site, our process required placing a flat surface in the existing machine and manually pushing it through 4 times to cut 4 edges. With the new machine, the flat is entered once, and the end product is a flat surface with all 4 edges treated and completed as designed. “It makes the part more compliant with the drawing and specific to the color spectrum of the customer,” Dusty said. “Some customers have required us to adhere to extremely tight dimensions, plus or minus 0.3 millimeters. This machine gets us closer to reality in that regard—better than any process we’ve ever had.”
Dusty continued, “With the new machine capable of maintaining multiple colors in a single magazine, there’s no need for constant changeovers, either.” The machine at FSSF can seamlessly switch from order to order with different colors, and up to 6 units can be in the queue at a time, as long as they’re all the same length and width.
Manufacturing Readiness Grants (MRG) provided by the Indiana Economic Development Corporation and administered by Conexus Indiana are available to Indiana manufacturers willing to make capital investments to integrate smart technologies and processes that improve capacity. Fred Smith Store Fixtures made an investment in its smart manufacturing capabilities to expand product offerings at its Corydon, Indiana, plant.
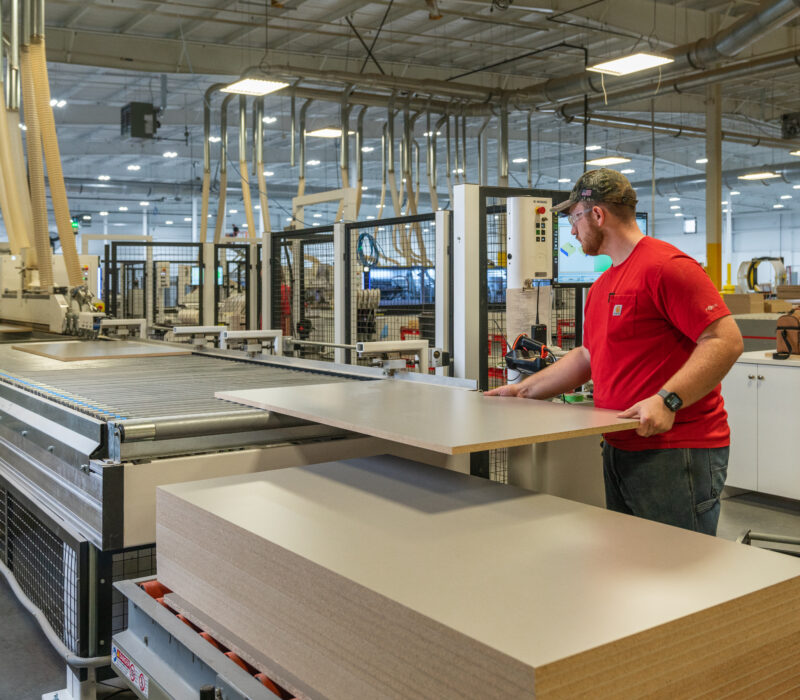
Key Learnings
Technology adoption should go hand-in-hand with overall strategic planning.
“If you walk into our facility today,” Dusty said, “you’re going to see this efficient machine sitting back there. It’s so large that we had to install it in an ‘L’ configuration, so as a product moves through the manufacturing line, it makes a 90-degree turn. With the Corydon facility expansion now complete, he added, the machine is migrating with other equipment into a straight-line configuration, “We call it a combo line,” he said. “The combo line now is our centerpiece of the operation.”
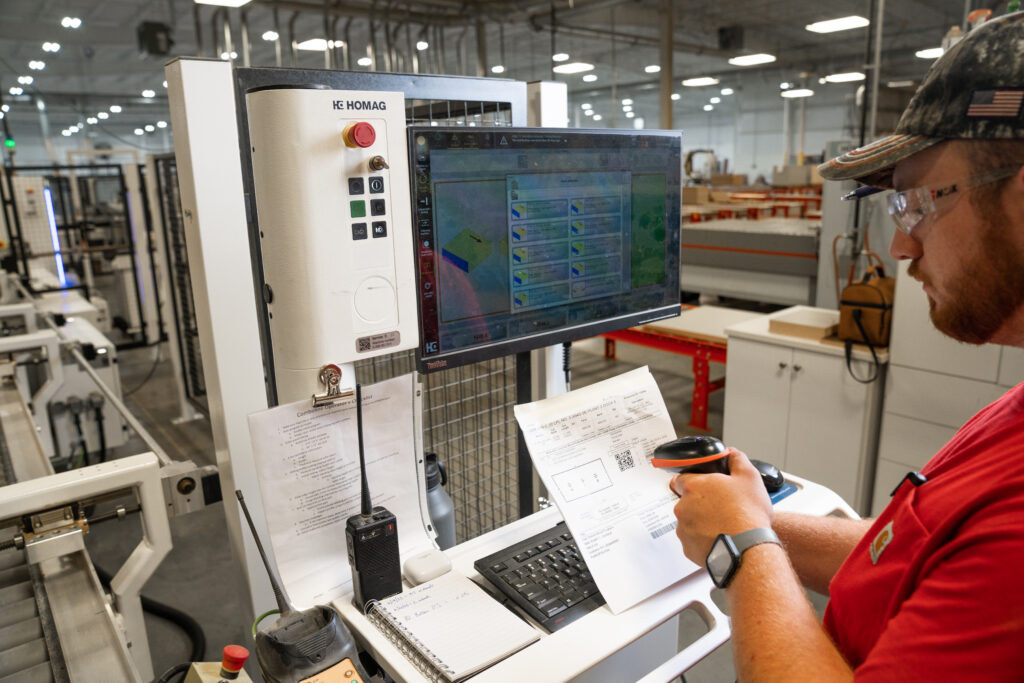
Although it all worked out in the end, Dusty said alignment with the overall FSSF strategic plan may have resulted in a different project design from the start. “We have so many more opportunities for automation and technology in our facility. This project has really helped us see what might be on the horizon in terms of adoption. We’re still scanning barcodes, we’re still loading programs, but this new machine takes us into the big league.”
Smart technology was the answer to augment a tight labor market when post-pandemic business growth returned.
With a 30% drop in revenue, workforce attrition, and a few layoffs as a result of the pandemic, the post-pandemic situation for FSSF was a different story. The hotel/motel industry came roaring back, resulting in massive growth and new orders for FSSF. But one pre-pandemic issue remained: a very tight labor market in Harrison County. Fortunately, the next-generation machine lightened that burden significantly. The general manager, Dusty, shook his head at media reports that automation kills jobs. “The only labor we reduced with the implementation of our new equipment was the manual aspects of our processes,” he said. “When I first started here 16 years ago, we hardly had any automated equipment. Everything was manual, requiring physical strength. And there’s also the generation coming in to work for us saying, ‘I like manufacturing, but I really want to be on the cutting edge.’ And boy, are we doing that!”
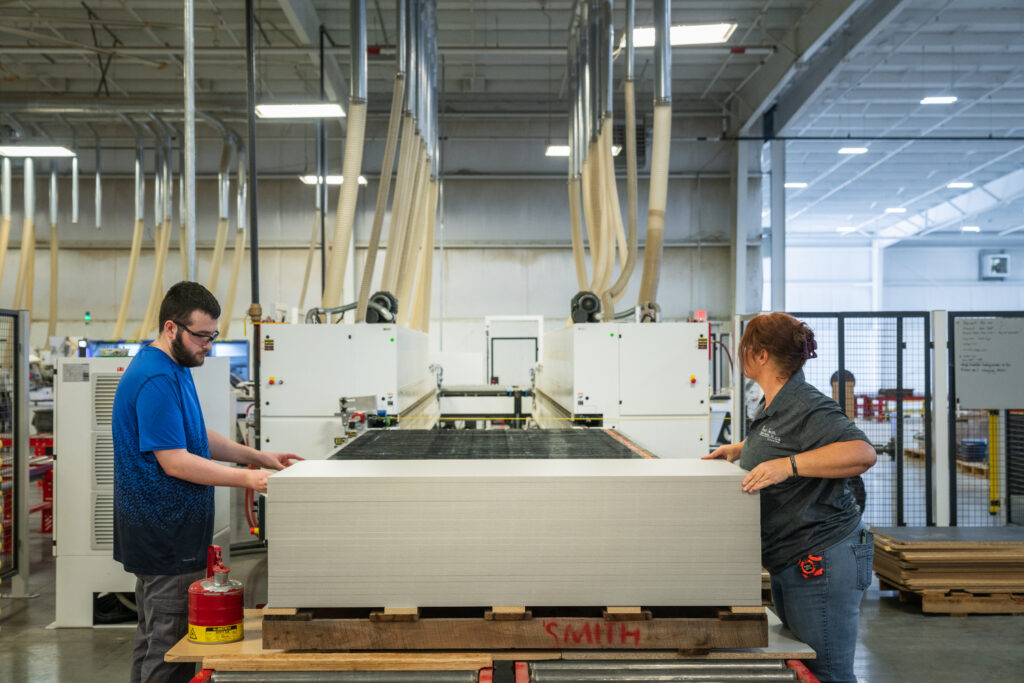
“We’re now back up to about 140-145 jobs,” Jon added. “But we’re doing almost as much business as we were when we had 170 employees, and that’s because of the smart technology we’ve been implementing. It really does keep us from having to add more shifts and ask people to work long hours. Technology comes at a cost, but it creates more productivity and pays a big dividend in terms of profitability and growth.”
Dusty agreed: “It’s not about providing any job. It is about offering roles that our workforce wants to be in for a long time and grow into. Technology adoption can entice the workforce to stay with us.”
“It’s not about providing any job. It is about offering roles that our workforce wants to be in for a long time and grow into. Technology adoption can entice the workforce to stay with us.”
Dusty Rhodes
General Manager at Fred Smith Store Fixtures
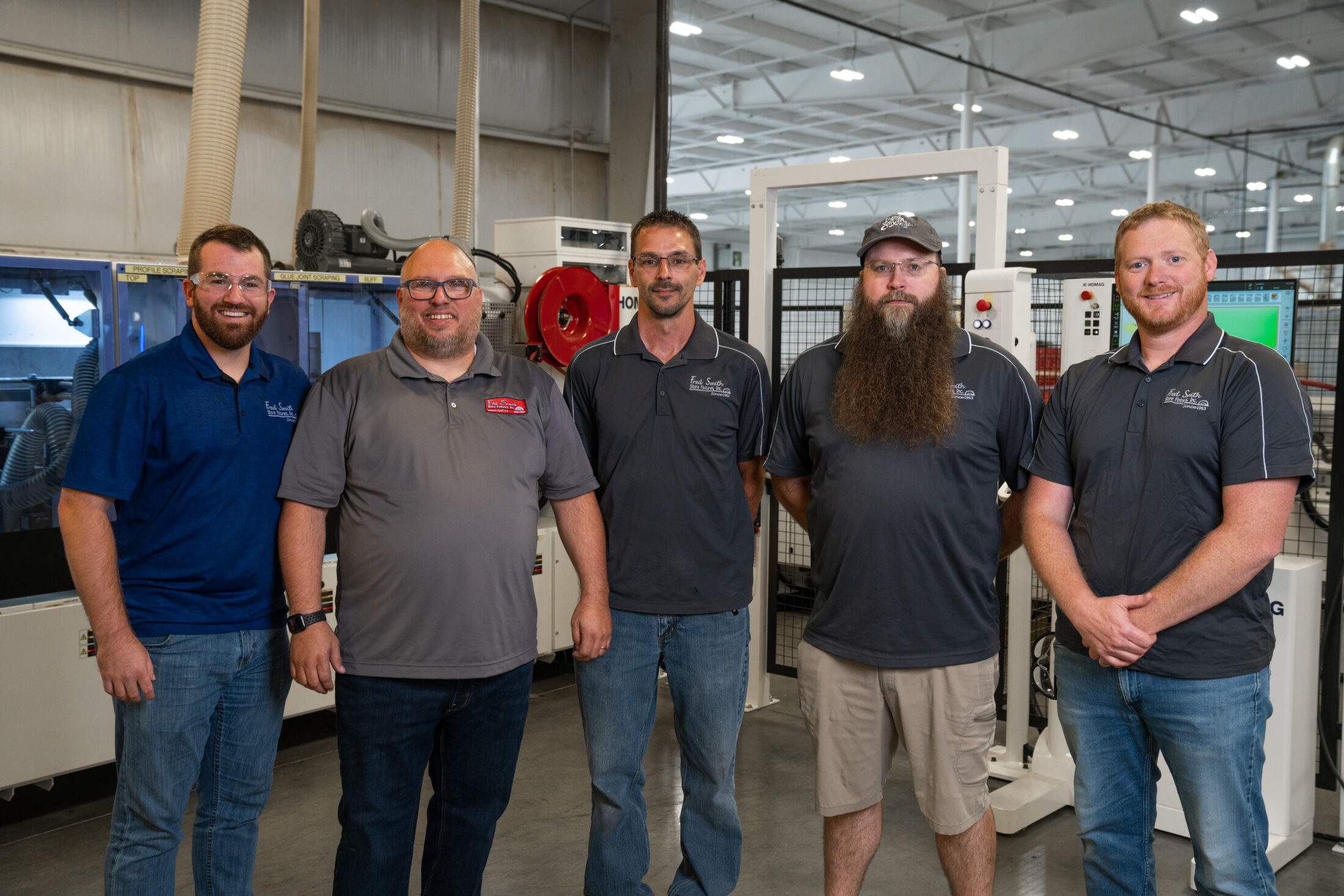