Marson International
Elkhart-based tube fabricator Marson International has pursued growth aggressively in recent years, investing in equipment, expanding operations and chasing new clients. While that approach has fed a steady stream of successes for the 20-year-old firm, this year it delivered a significant reward: A major contract with Volvo.
As it gears up to deliver on that contract, the company has tapped into a variety of resources designed to help Indiana firms grow.
With about 125 employees at three locations in Elkhart, Marson provides tube fabrication for customers including automotive and recreational vehicle manufacturers, mass transit and power generation organizations and construction and agricultural equipment firms.
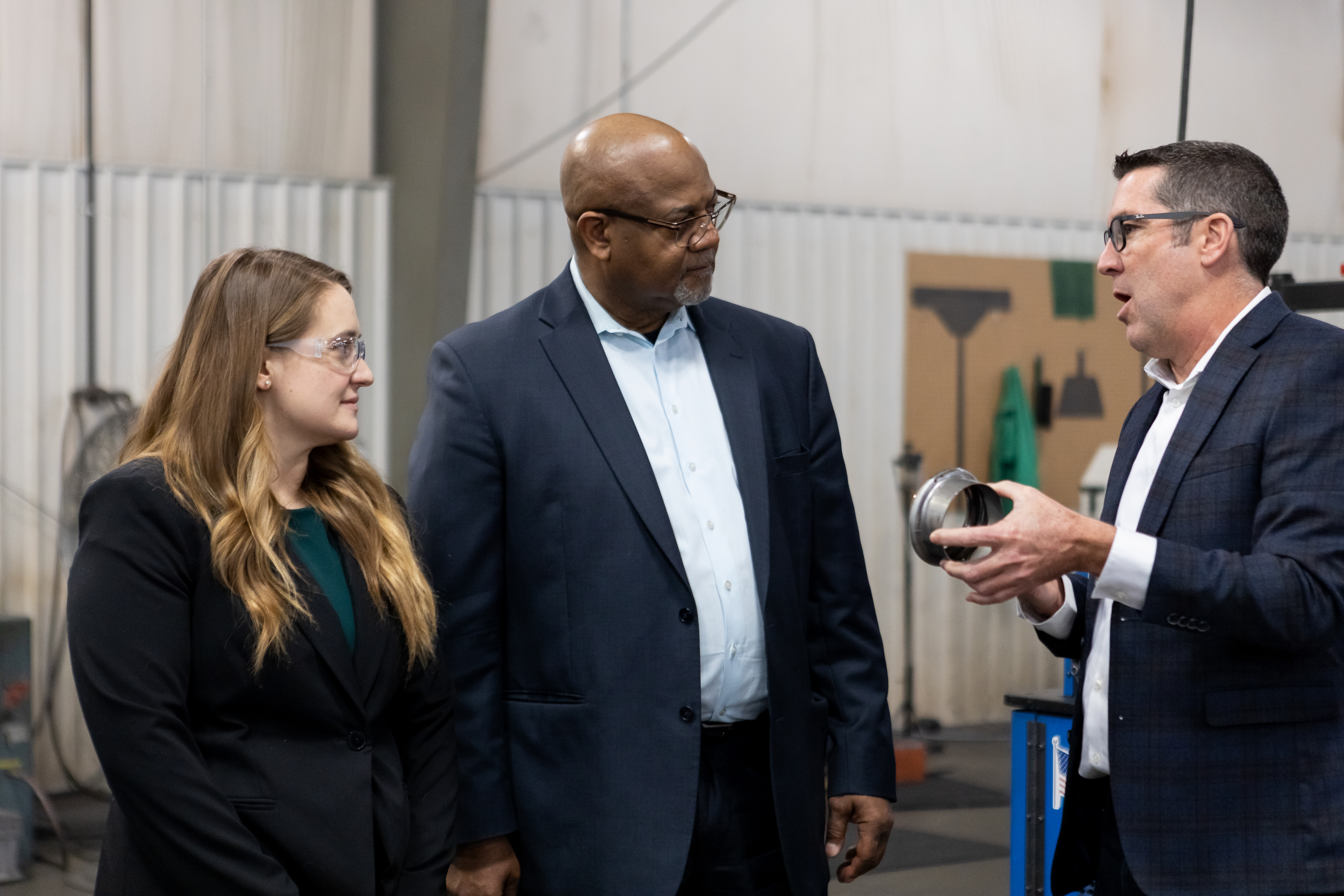
The company already had been modernizing operations, Plant Manager Lucas Vicentini says, but the Volvo contract kicked that effort to a higher level. A firm that typically produces relatively small batches of product, Marson was asked by Volvo to boost production to tens of thousands of units, a leap best realized using industrial robots.
Of course, buying robots is a significant leap for a relatively small firm, but Marson received a Manufacturing Readiness Grants award from Conexus Indiana and the Indiana Economic Development Corporation. Designed to help Indiana companies invest in Industry 4.0 technologies, the grant award softened the balance sheet impact of purchasing robots.
The next challenge: Finding workers to operate those robots. Complicating that mission is a nationwide worker shortage that has challenged the firm’s ability to recruit general labor, making it even more difficult to hire workers with the skill to program industrial robots and maintain equipment. The Elkhart-Goshen Metropolitan Statistical Area (MSA) currently holds the country’s lowest unemployment rate for MSA areas at 1.6%, with the MSA national average currently sitting at 4.4%.
To solve this problem, Marson connected with local and state education, workforce and economic development organizations to create a U.S. Department of Labor Registered Apprenticeship program that will prepare six workers to program, operate and maintain automation equipment through the process of loading tubes into and out of the machines that bend them.
When Marson announced the apprenticeship opportunity, three of its current workers signed on. The firm found three additional candidates at a job fair that attracted approximately 25 skilled applicants.
Among the incumbent workers who signed on was 27-year-old Antonio Lopez, who has been with Marson for five years, working most recently in the materials receiving department. Lopez says he looks forward to the apprenticeship program, which will see him taking classes through Ivy Tech Community College, South Bend – Elkhart twice a week for three semesters. The apprenticeship programs will leverage a new academic program of study option at Ivy Tech Community College called the Smart Manufacturing & Digital Integration Certificate. This provides students with the opportunity to earn both industry-recognized certifications from the Smart Automation Certification Alliance (SACA), as well as academic credits that can be used toward a future degree.
“I like learning new things,” Lopez said. “I’m always looking for new opportunities and looking to grow.”
While the mention of robots often worries workers who think they will lose their jobs to high-tech machinery, Vicentini points to the new positions being created by the robots, and said he expects continued growth at the firm that increases its workforce by about 50% over the last year.
“There’s more to come,” he said. “We have to be always learning and hiring.”