Hardtech company, MITO® Material Solutions, scales up production of its proprietary manufacturing additive materials with investments from Indiana VCs and a Manufacturing Readiness Grants award
MITO Material Solutions
Case Study
Key Stats

Company History
MITO Material Solutions grew from an MBA student’s business idea to a venture-backed, hardtech startup in less than a decade. Now the company provides various manufacturers with next-generation additive materials for their products.
Co-founders Haley Marie Keith and Kevin Keith parlayed their business acumen and a technology license from Oklahoma State University into one of Indiana’s newest and most successful manufacturing enterprises including making two of the Forbes 2021 “30 Under 30” lists within 5 years of found the company in 2016. When Haley Keith was an MBA student at Oklahoma State University, the concept that became MITO was hatched as part of a classroom assignment to create a business model. That model remains the company’s roadmap today and has helped MITO grow from five employees to 14 since it was relocated to Indiana in 2020 after participation in The Heritage Group Accelerator Powered by Techstars.
“During my MBA, MITO’S original technology was sitting on the shelf, patent-pending, and still in development at Oklahoma State University,” Haley Keith, MITO CEO, was quoted in an interview with one of MITO’s early investors, venture capitalist Evergreen Climate Innovations. The interview was posted on Evergreen’s website, September 14, 2021. “After some back-of-the-napkin math, my co-founder and I realized the impact one additive could have on an aerospace application.” Adding the additive powder to a single Boeing 787 airplane could reduce up to 48,000 pounds of weight, saving millions of fuel costs and untold emissions, she estimated. The opportunity was one big enough to form a startup around — Haley as CEO and Kevin as CTO. The goal of MITO’s is to “unlock the power of hybrid polymer materials with specialty additives” and provide them as scalable solutions to empower manufacturers and their products.
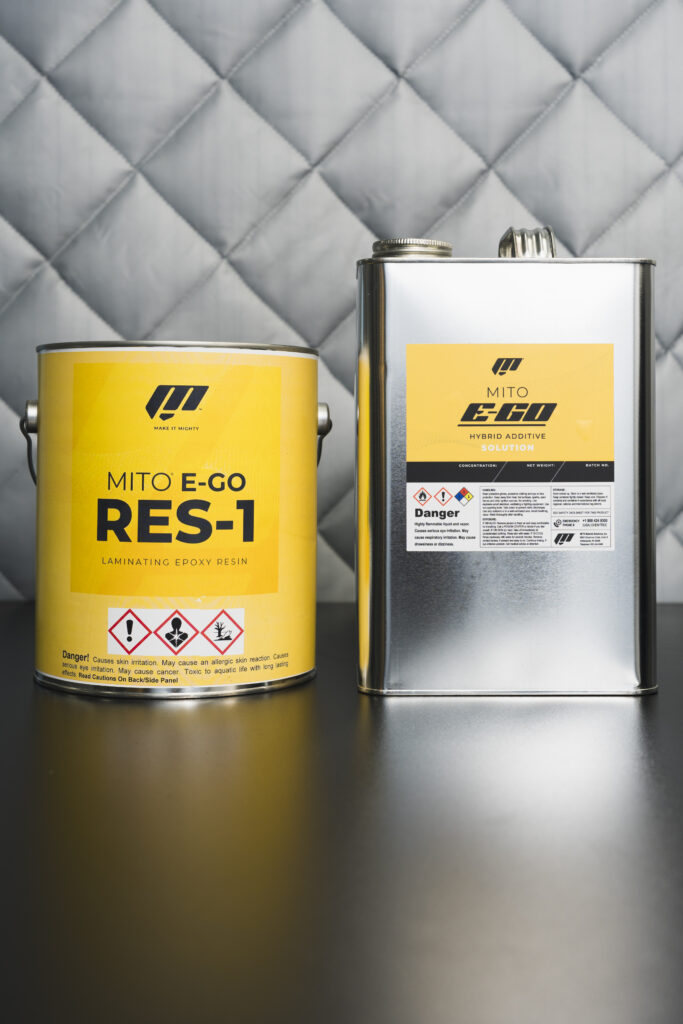
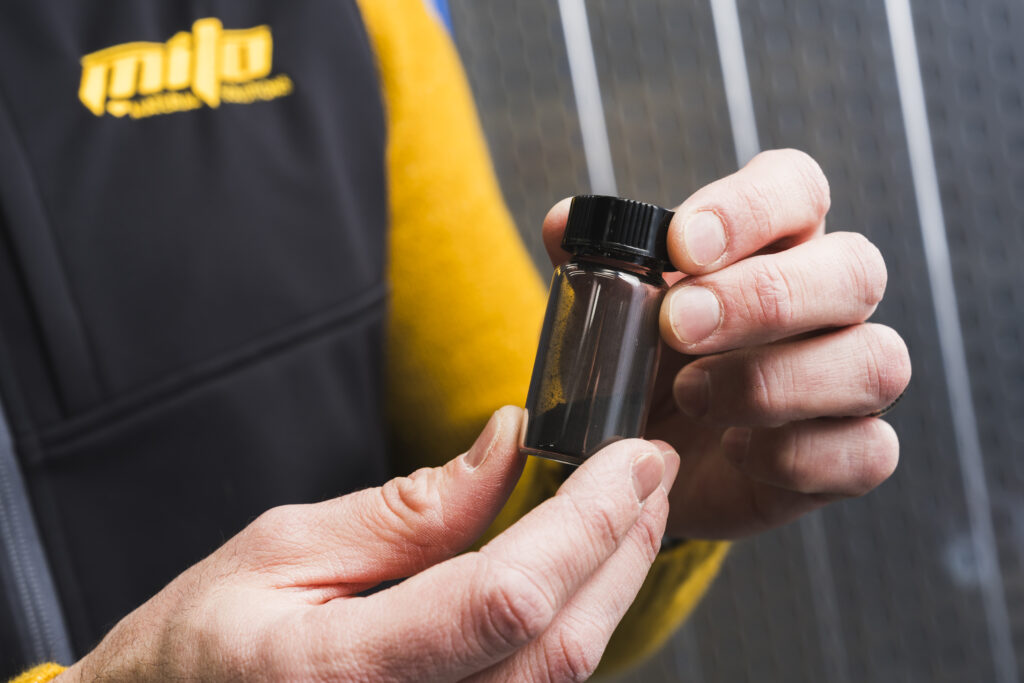
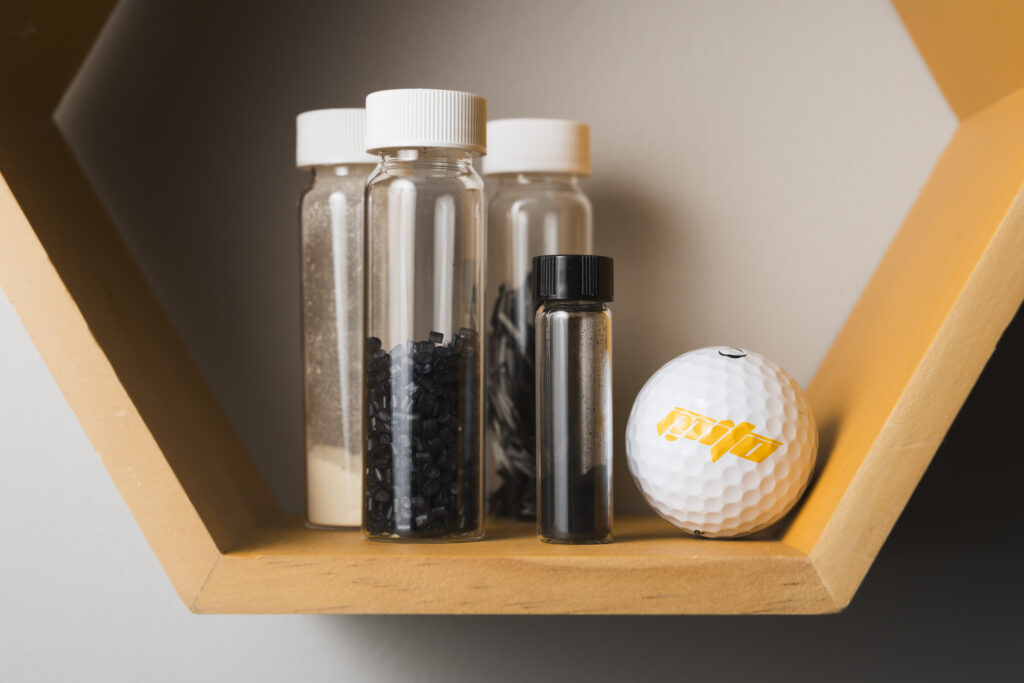
MITO’s patented technology platform can functionalize substances like graphene and biomaterials, creating hybrid additives that increase a product’s strength, durability, flexibility and sustainability. In fact, MITO’s first commercially adopted product, E-GO, was used in a consumer product by a customer called Folsom Custom Skis in 2022. Folsom found MITO’s additive improved its ski performance in the lab and on the slopes. While the MITO additives are proprietary, Keith noted, “MITO does not manufacture graphene and other substances. We source the materials and use them as platforms to formulate and pair with other molecules” Using its proprietary chemistry process, MITO develops new hybrid additives for use in composite materials in various applications.
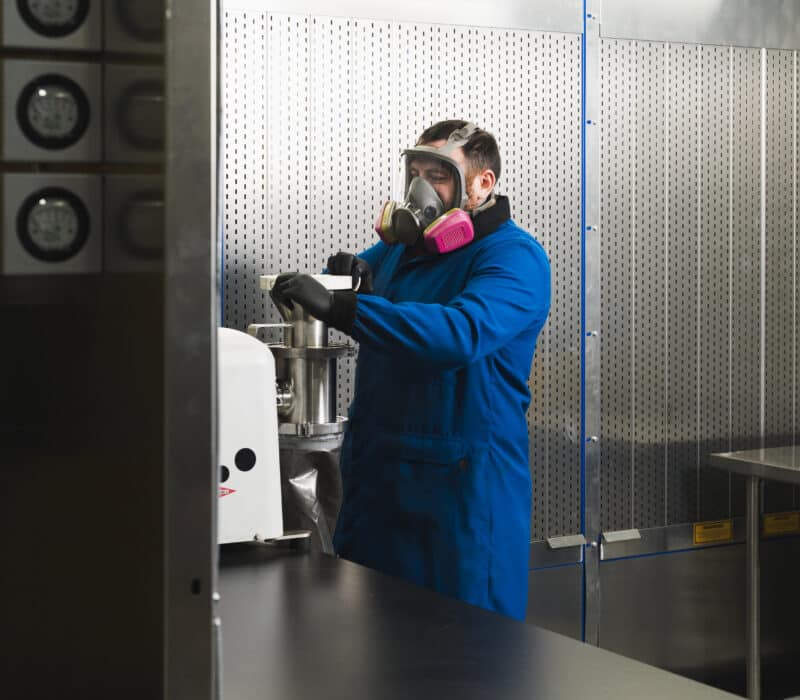
The Project
Tech adoption will help MITO achieve its long-term production goals, including processing efficiency and product quality.
MITO serves the transportation sector, including trains and cargo ships; sporting goods from bicycles to baseball bats; and, most recently, the infrastructure sector. “There is a huge movement on the longevity of roads and bridges, cell phone towers, and concrete itself,” said Caio Lo Sardo, Executive Vice President at MITO. “We replace some materials or concrete with a composite strengthened with MITO additives to extend durability. In turn, our customers use less material and lower their operational costs because they no longer require the same amount of concrete to achieve the same performance. It’s a bit of a domino effect on the value chain when customers implement our polymer or polymer additive into a composite material.”
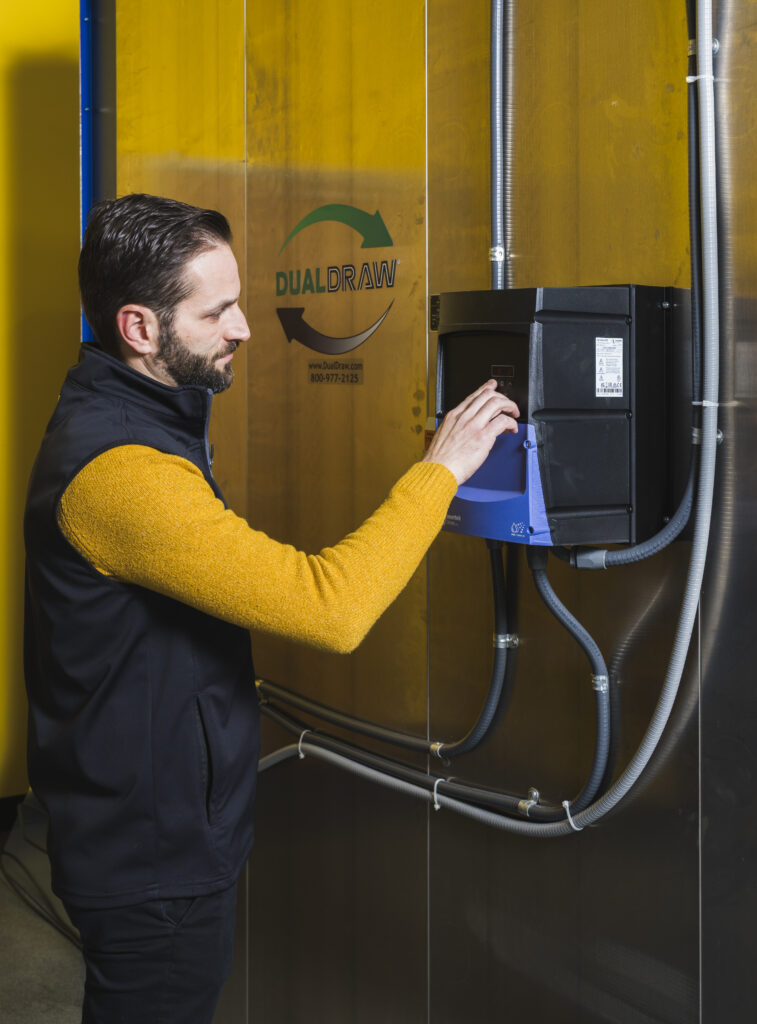
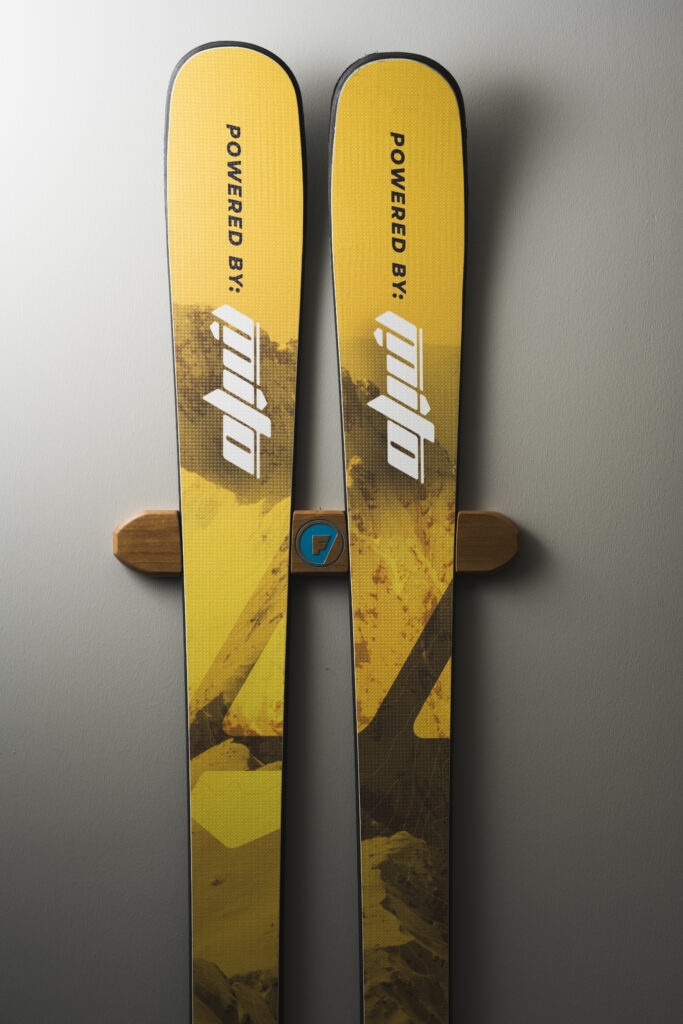
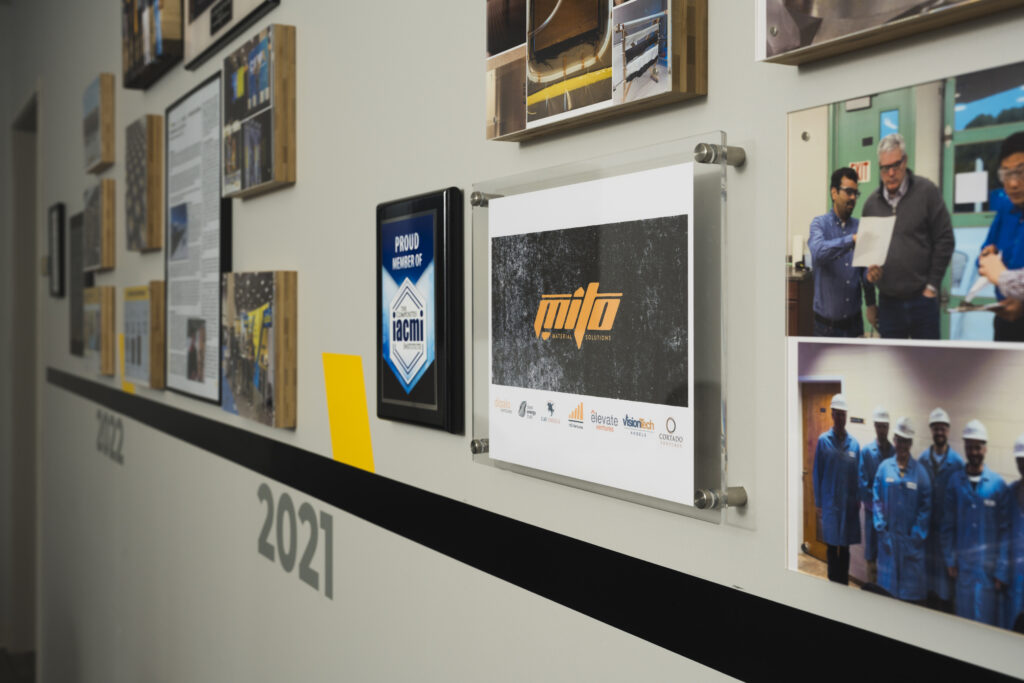
A contract manufacturing partner completes 85% of the process and delivers the additive materials to MITO for post-processing. At MITO’s facility, the material is refined into powder form and transformed into an additive that’s easily used by customers. “That part of the process is kept in-house because of the intellectual property and trade secrets,” Caio Lo Sardo, Executive Vice President said. Part of MITO’s Manufacturing Readiness Grants (MRG) award was devoted to a new powder processing system for use in MITO’s in-house production facility, which will significantly increase MITO’s efficiency and capacity. The closed-loop system not only boosted output but also decreased production time to just a few hours, marking a substantial time-saving compared to the two weeks before the equipment was installed.
The remaining portion of the MRG was invested in an enterprise resource planning (ERP) platform, which was custom-designed and created for just-in-time inventory control between MITO and its contract manufacturers. Due to MITO’s special requirements as a supplying manufacturer, the ERP had to be designed from scratch and required nearly a year to complete. The system ensures MITO can achieve its long-term, large-scale volume processing with efficiency, quality, and consistent batch-to-batch post-processing goals.
Manufacturing Readiness Grants (MRG) provided by the Indiana Economic Development Corporation and administered by Conexus Indiana are available to Indiana manufacturers willing to make capital investments to integrate smart technologies and processes that improve capacity and productivity. An MRG of $112,500 was one of the investments that helped MITO Materials bring custom-designed technology in-house to manufacture their proprietary and transformative additive materials at scale.
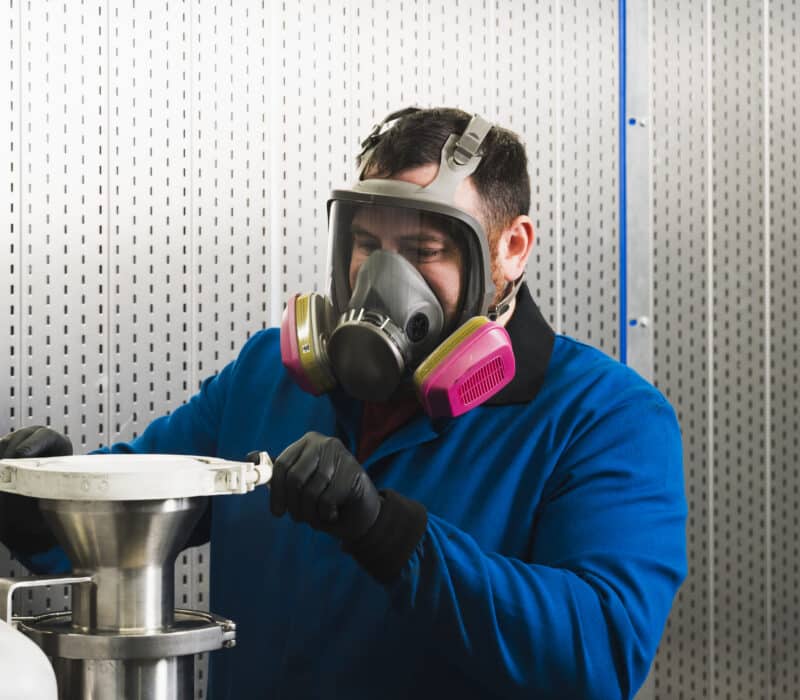
Key Learnings
From a small incubator in Oklahoma, to the Heritage Group Accelerator Powered by Techstars, MITO leveraged entrepreneurial resources in Indiana to accelerate their commercialization journey.
“It’s difficult to be a hardtech startup in today’s market because of the long sales cycle and product development times,” said Lo Sardo. Participating in a startup accelerator with The Heritage Group helped us confront those challenges head-on. “Using The Heritage Group’s resources and network of mentors, we focused on compressing 12 months of growth in 12 weeks. Go-to-market, hiring, fundraising and proof of concept are all requirements to build a manufacturing company from scratch.”
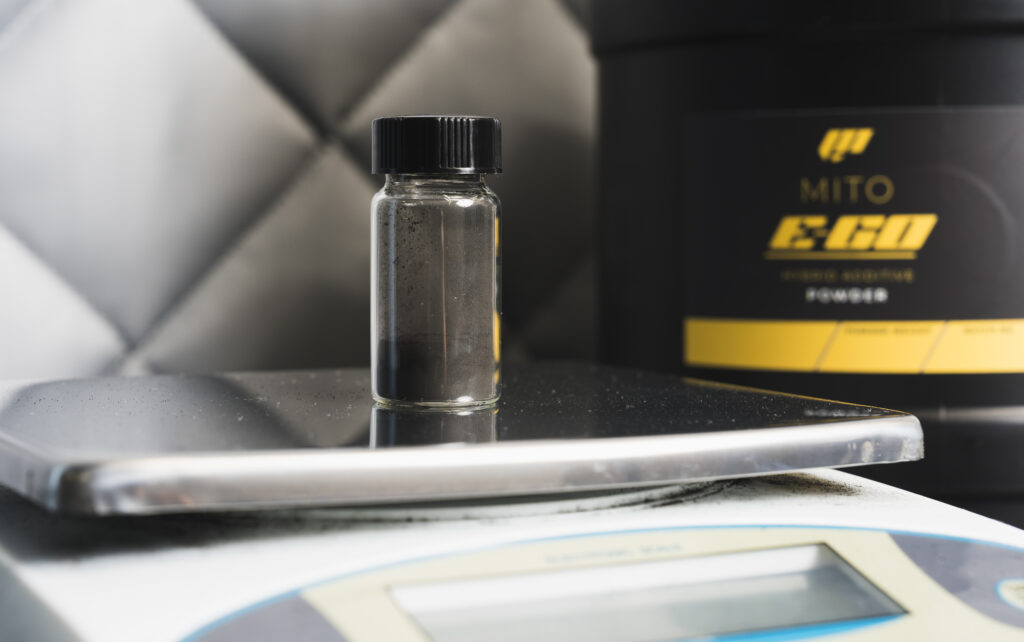
After the program, MITO experienced increased fundraising success, including venture funding from Indiana’s Elevate Ventures, Chicago’s Evergreen Climate Solutions, and several angel investors. Many of those initial investors were once again on board for the second funding cycle in 2022 led by Ingevity Corp. of North Carolina. With those funds, MITO leased a space on 86th Street in Indianapolis with a new lab for developing its industry-leading products and technologies. The 86th Street location was outfitted for growth and opened in April 2022. “Quick to market for us was crucial,” Lo Sardo said. “That was something we were able to achieve much faster with the startup accelerator program in Indianapolis and all the mentors at The Heritage Group. Everyone was extremely supportive, and it was a game changer for us.”
Keith believes locating MITO in the greater Indianapolis area was a significant asset, too. “Indianapolis has all the diversity of the Northeast with the grit of the Midwest,” she said in her interview with Evergreen Climate Solutions. “Indiana is a great place to grow a business, raise a family and build on our company’s success.”
Finding a trusted technology provider is crucial for successful project implementation.
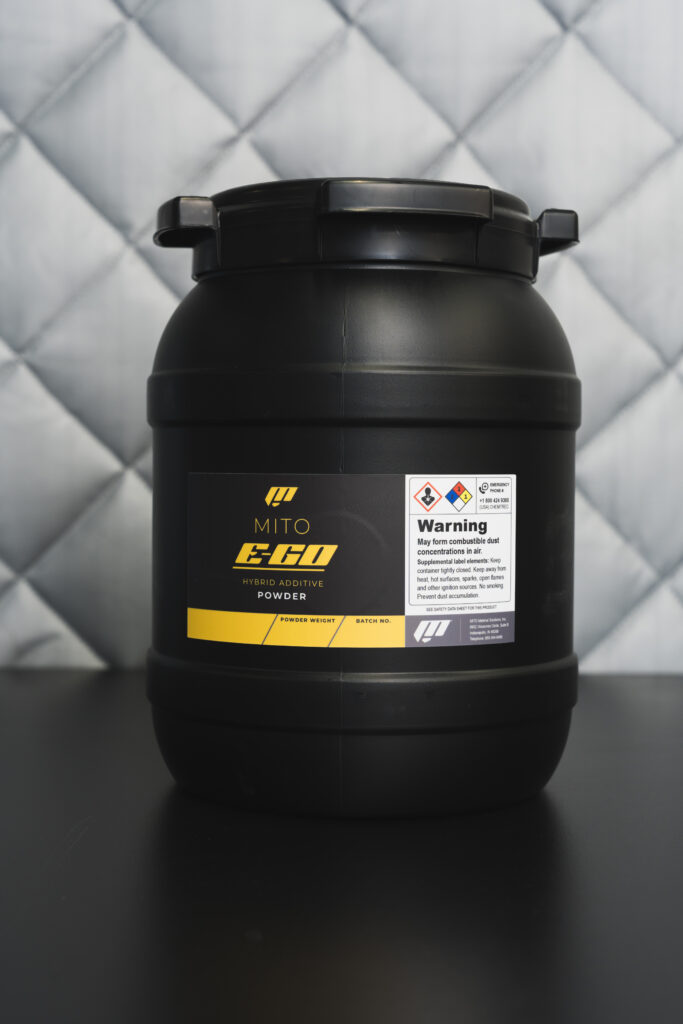
Lo Sardo, MITO’s operations chief, again stressed the need to protect intellectual property and trade secrets throughout the equipment procurement process. “You need to be able to interact openly with technology partners,” he said, “and you need to pay attention to the details.” Implementation of MITO’s new powder processing system was less about workforce training and more about the identification of the right machine and specs. “Because our technology platform is patented, there is no machine or specs that are one size fits all. It was always going to be something custom-built to suit our needs,” Lo Sardo said. “It also had to be cost-effective and safe.”
For a startup with 14 employees, allocating $250,000 to expand manufacturing capacity represents a significant capital investment and positions MITO strategically for expansion. The combination of a new powder processing system with automated ventilation, coupled with the development of an ERP platform from scratch, is geared towards not only growth with existing customers but also capturing demand from new markets.
“Because our technology platform is patented, there is no machine or specs that are one size fits all. It was always going to be something custom-built to suit our needs.”
Caio La Sardo
Vice President of Operations at MITO
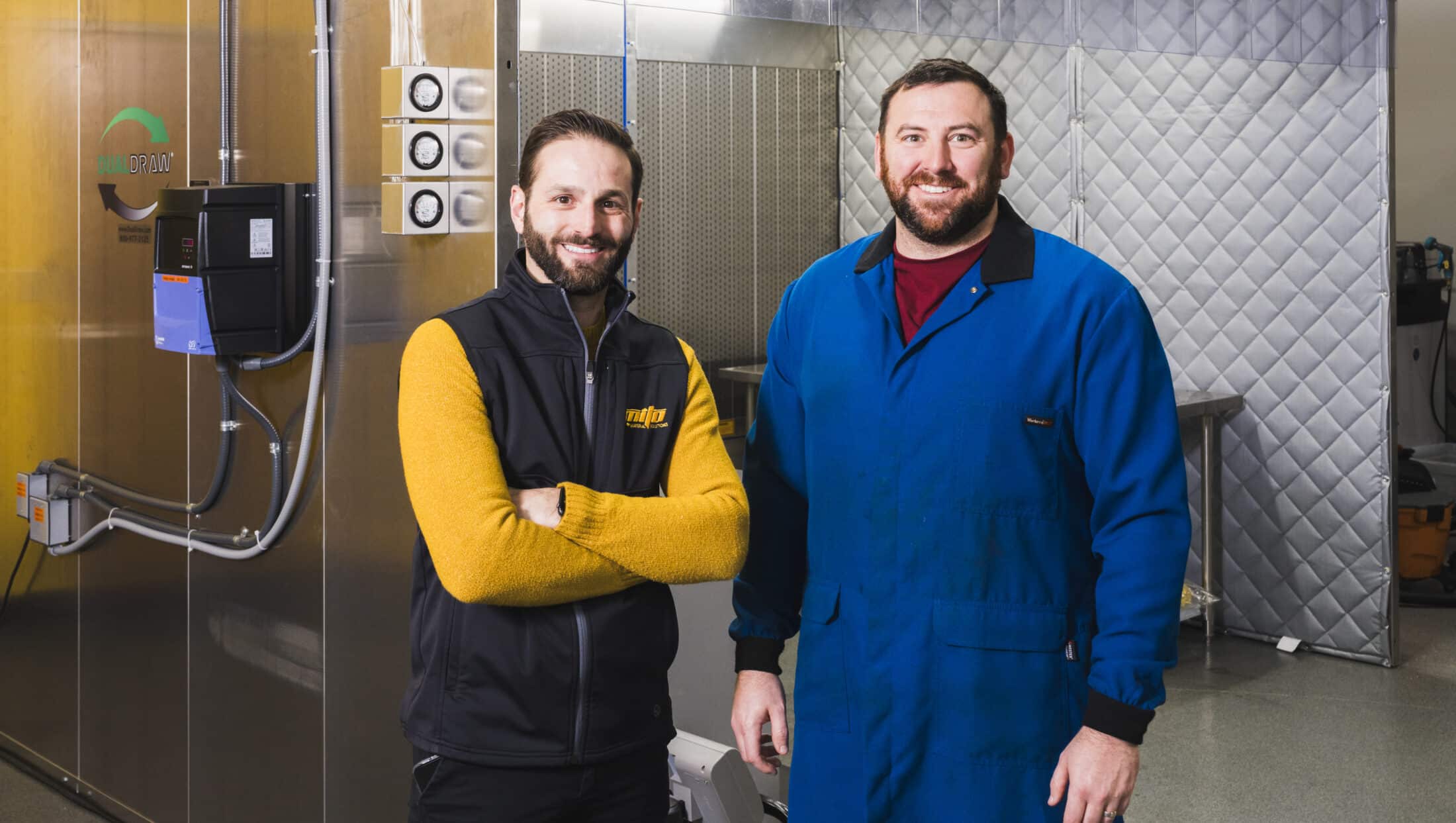