Mursix Corporation Implements Digital Plant Technologies for Large Scale Production of a Novel Medical Device
Mursix Corporation
Case Study
Key Stats
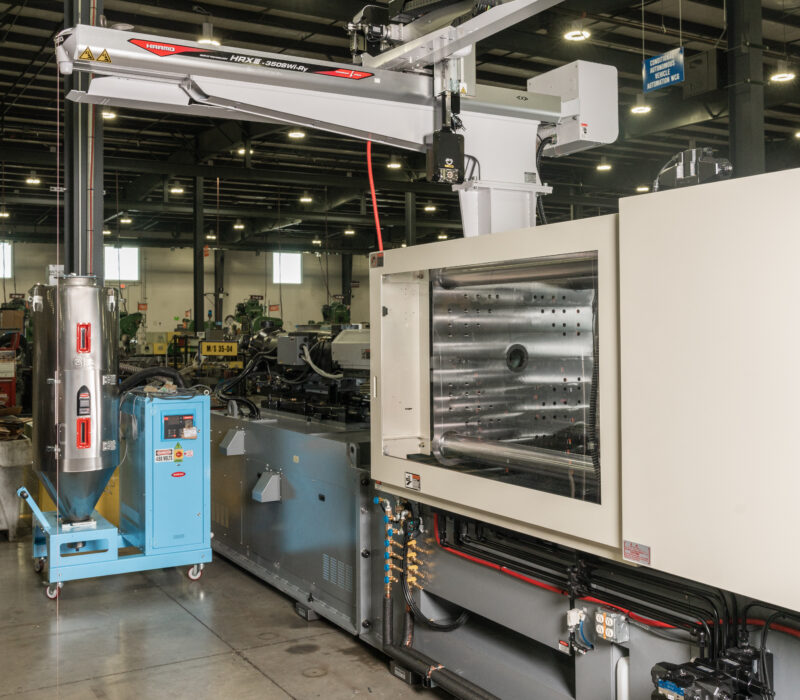
Company History
For Over 70 Years Mursix Corporation Expanded Business by Extending Manufacturing Capabilities.
Mursix Corporation grew from Twoson Tool, a company founded in 1945 to manufacture metal hose reels designed to mount on houses for storing garden hoses. By 1990, Twoson operated with some 20 employees and $3 million in annual sales. Originally Located in Fairmont, Ind., it was primarily an appliance supplier by then, and it was purchased in 1990 by the Murray family. The new owner added to its multislide stamping capabilities and expanded into metal forming and stamping. The company prospered, eventually becoming known for precision metal components, plastic over-molding and injection molding.
The financial crisis in 2008-2009 was particularly difficult for small businesses, but Mursix capitalized on its willingness to move quickly and decisively, extending its capabilities and moving into new markets and products. Today, Mursix calls Yorktown, Ind., home where it surpasses $40 million in annual sales and has more than 200 full and part-time employees. Its sterling reputation is built on custom-engineered product solutions for businesses in the automotive, hospitality, healthcare, alternative energy and other industries. It also continues to serve the appliance industry.
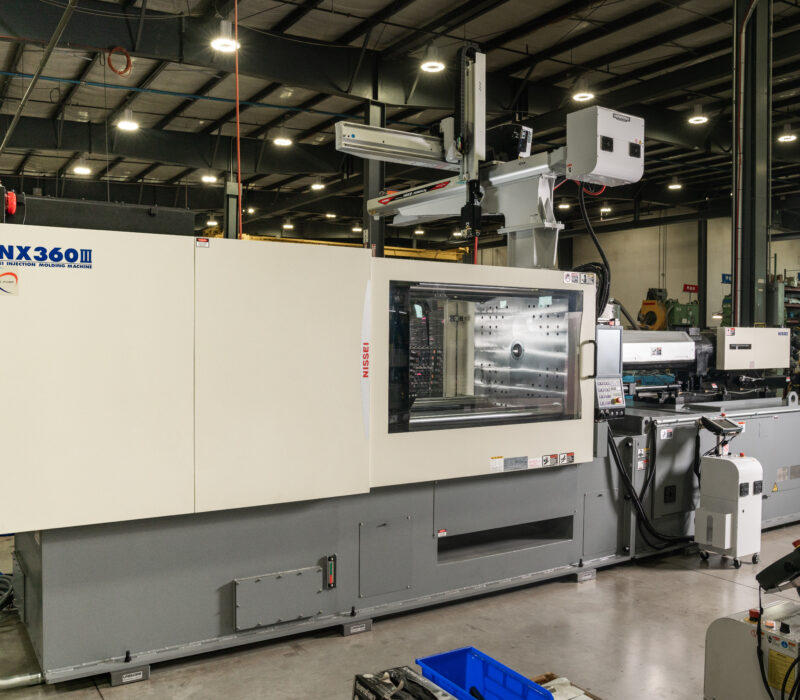
The Project
Forging a New Partnership for Medical Device Development and Production.
The Manufacturing Readiness Grants program seems custom-designed for creative and nimble companies like Mursix Corporation. Mursix pivoted early in 2020 to produce millions of pieces of Personal Protective Equipment (PPE) to support COVID-19 response efforts and is now aggressively pushing further into more sophisticated medical device manufacturing.
The Manufacturing Readiness Grant will support investment in production equipment rich with digital plant features necessary for the manufacturing of a new telehealth medical and drug device. The device is innovative and proprietary and is working its way through FDA approval at the time of this case study. It is still so confidential that Mursix, as the contract manufacturer, must refer to their customer as ‘Company Z’.
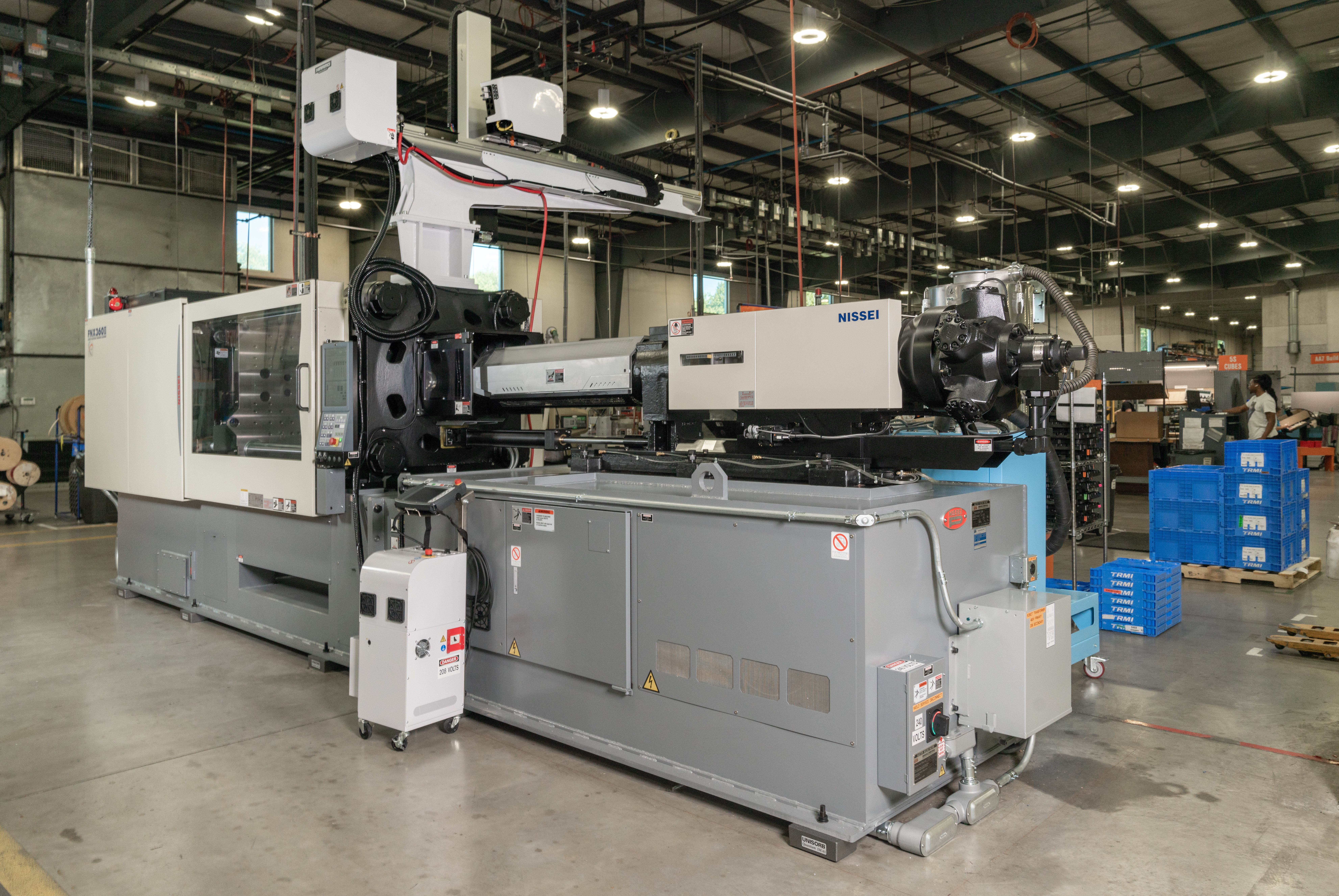
As Vice President of Business Development for Mursix, Susan Murray Carlock’s nursing background gives her a special interest and expertise in the project. A complex product, the new device will serve a complex customer. The healthcare industry and the regulatory agencies that oversee it have a justifiable low tolerance for error, requiring a new machine with significant technology upgrades to meet the demand for rapid and precise manufacturing under tight environmental controls. The challenge is welcome, even exciting for Susan, who calls the new device, “the only patented technology of its kind globally.”
Hiring the Right Players: From Product Launch to Scale
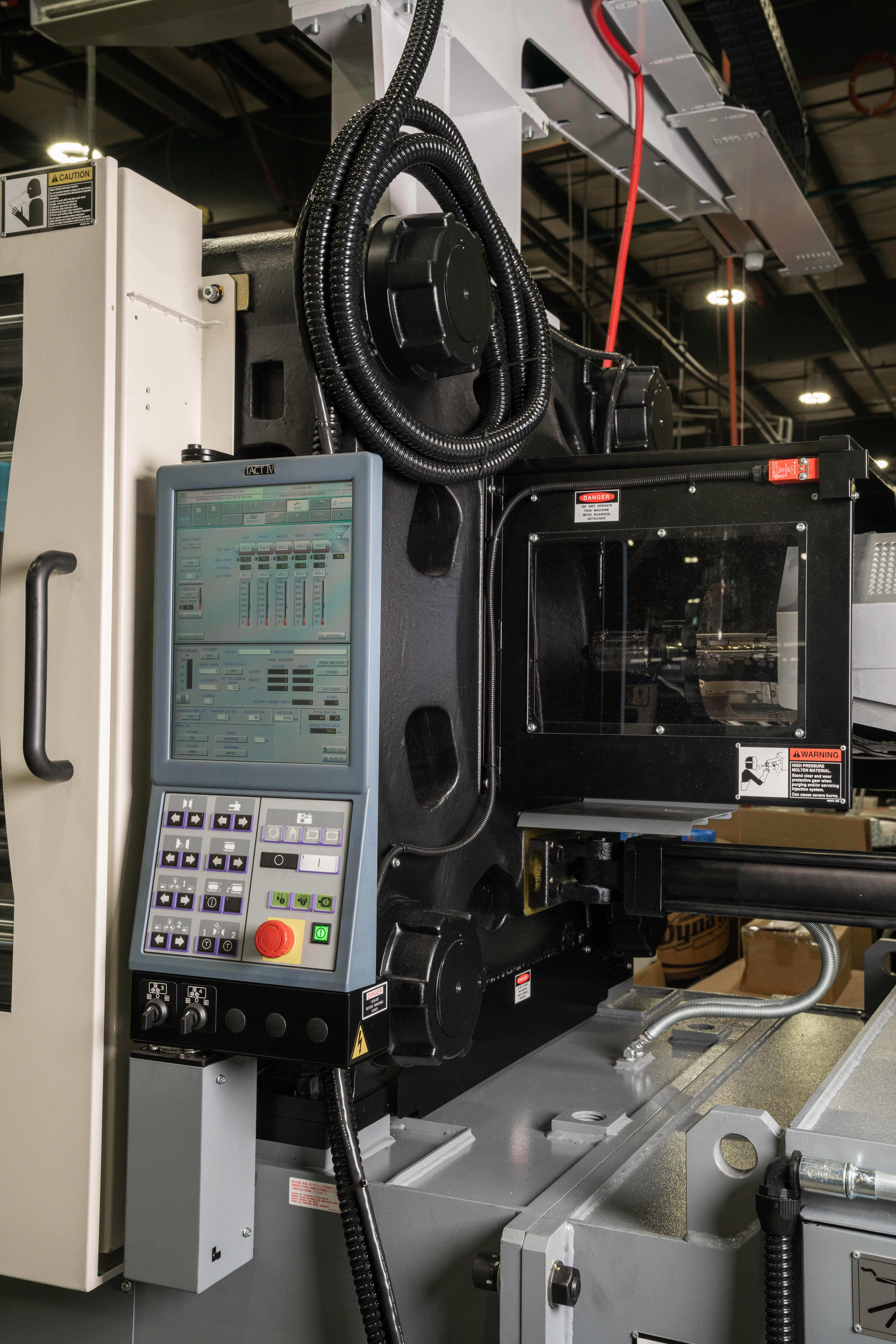
Becky Rhoades, Mursix’s program manager, was one of the first Susan chose for the team, whose focus is the Company Z product launch, and her manufacturing and process experience is high on her list of qualifications. Becky works alongside Susan on the new process and she, too, is excited about the technology and what it adds to the manufacturing process. “It’s smart technology, open architecture, and Bluetooth enabled,” she said. “We’ll be able to see downtime and how they’re running moment to moment, minute to minute, as opposed to at the end of the shift.” The vision system, too, is a great advantage for such a highly regulated product, she said. “The FDA, for example, will be able to visually see what we’re doing, how we’re tracking, and make sure our quality control is precise. Anytime you’re manufacturing a medical device, there are general practices and other issues the regulators like to check.”
Mursix received a Manufacturing Readiness Grant to install just one machine to manufacture the new device. It gives Mursix the confidence to pursue the project, anticipated to require 15 to 20 machines once production is fully at scale. The machine installation is part of a wider strategic technology adoption roadmap, including advanced robotics, automation, and smart machine investments at the Mursix plant. The upgrades will enable the manufacturing processes necessary to meet customer and regulatory requirements. For example, the device has more than 100 components, which requires rapid swapping of tooling inside an injection molding machine and tools that must be environmentally controlled to be at the proper operating temperature when swapped into production. The process could not be completed at speed without upgrading to a digital plant.
Manufacturing Readiness Grants provided by the Indiana Economic Development Corporation and administered by Conexus Indiana are available to Indiana manufacturers willing to make capital investments to integrate smart technologies and processes that improve capacity and productivity, as well as companies willing to invest in healthcare manufacturing technology to support critical COVID-19 response. The digital plant investments being made at Mursix Corporation to enable production of a novel medical device, as well as Mursix’ agility to produce millions of face shields in response to the COVID-19 pandemic clearly met those requirements.
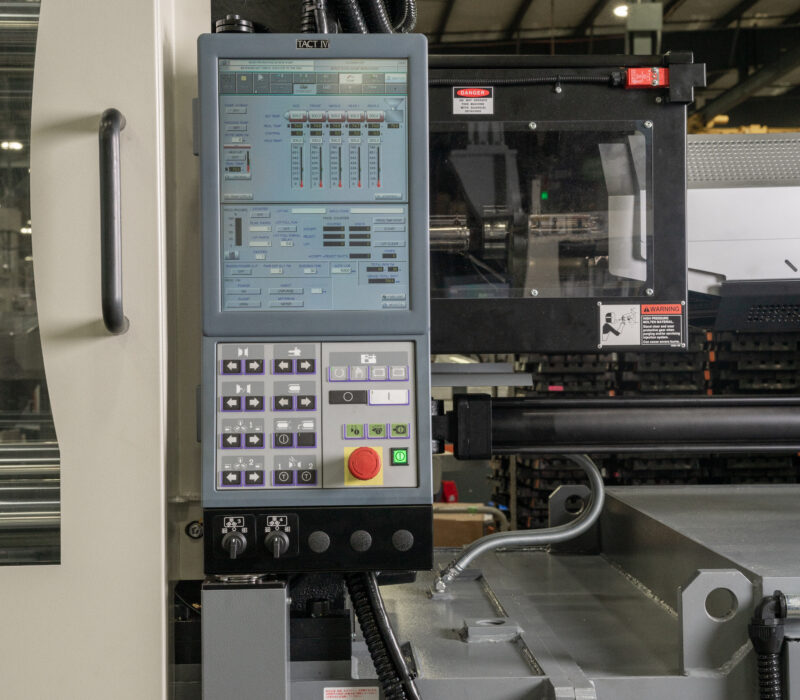
Key Learnings
Leverage Your Existing Strengths: Quality Audit Processes in the Case of Mursix
The company’s Yorktown plant is where the machine is to be operated and will house the Industry 4.0 processes sufficient for the healthcare industry. Mursix will implement a machine vision system that effectively will place Company Z on the plant floor, able to watch the process at every step and maintain the robust quality control required by complex medical devices.
The company already has a robust quality audit system to serve its experienced manufacturing custom systems for another heavily regulated industry—automotive—so they have a head start understanding what’s necessary in critical areas such as traceability. Not only must a component’s individual ID be noted on the packaging, it also must be present on the component itself since it will, at some point, be separated from the packaging.
Have a Vision for Upskilling Your Workforce in Industry 4.0: From Robotic Technicians to Environmental Facilities Engineers
Other obstacles presented themselves as the project planning progressed, including the implementation of multiple processes that are brand new to Mursix and its employees. Large blocks of new technology will be introduced, and workers must be trained to use the high tech. The regulations and reviews required by the FDA are both more numerous and more stringent than even in the automotive industry that currently occupies some 70% of the Mursix customer base.
The pandemic created more attention on the new telehealth device, and it was scheduled for rapid review, approval and production, adding additional pressure on Mursix and Company Z. That doesn’t mean a less stringent process though, and the FDA review remains a long and detailed oversight. One step in the production line needs to be fully automated, but the machine to do that doesn’t exist, so the company ultimately may need a custom build.
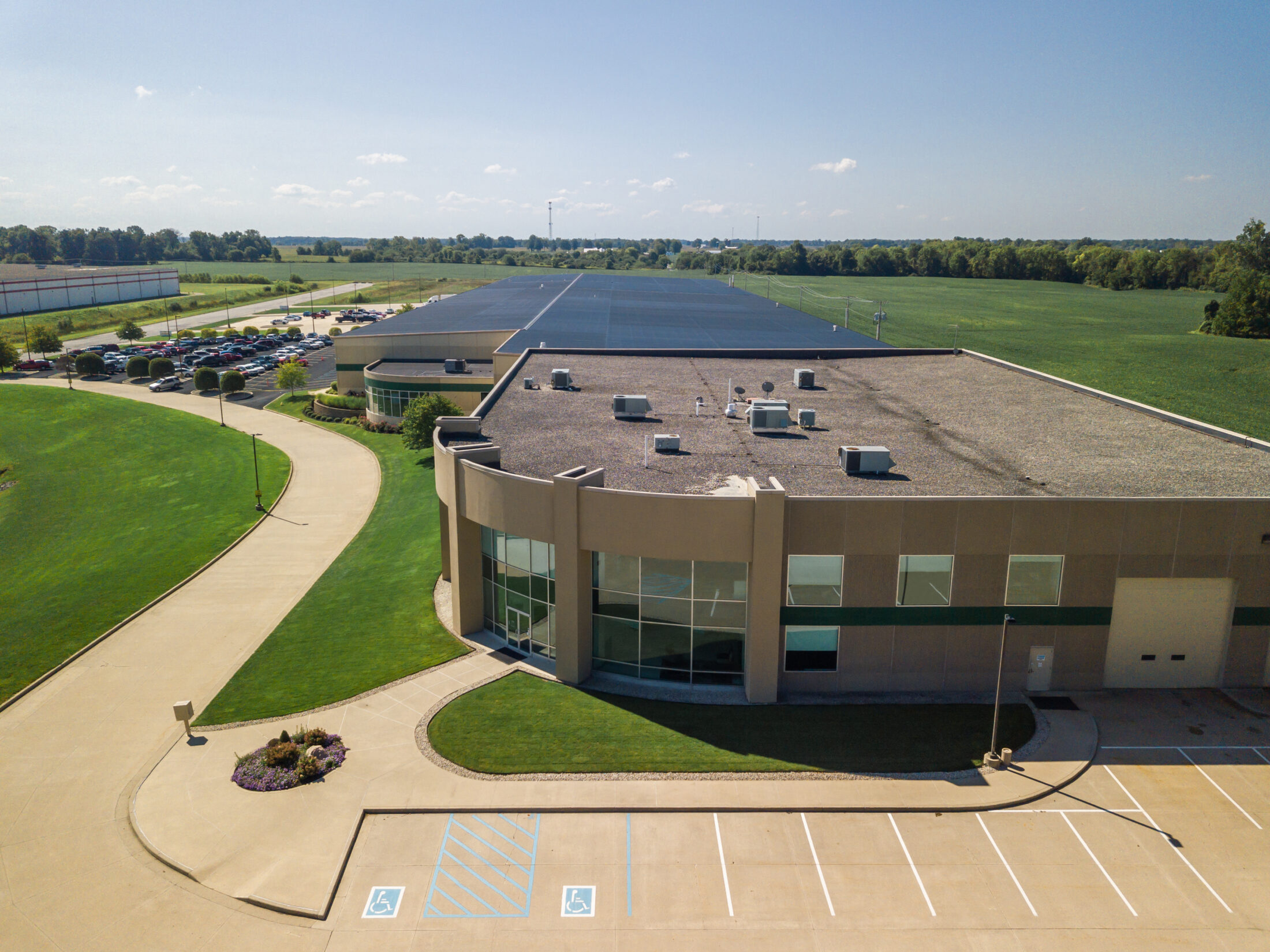
While Mursix employees are skilled at their jobs, the skillset for this project will require expertise on another level. The automated assembly line will need at the very least a controls engineer who has experience programming robots. The internal process engineers will need new training to commission, configure, optimize, and maintain the sophisticated new equipment. A facilities engineer will be required to supervise clean rooms, air filtration, temperature and other environmental factors vital to producing this complex medical device. And with the tremendous growth that is anticipated, Mursix will have to recruit, hire and train 80 to 100 new employees in the next two years.
Invest in Technologies that Allow Your Company to Grow & Remain Agile
Becky put a fine point on it: When you invest in Industry 4.0 you must make certain to choose open architectures that integrate broadly with equipment. Don’t get locked into closed, proprietary platforms. At every step of the start-up and operational process, it’s important to have flexible, open architecture to maintain control over the process; expanding, adapting and updating with the best technology available when needed. Transparency is likewise important. Customers want all data to be available and understandable, and the machine vision system is designed to ensure they have that. Success in developing and producing the new medical device is sure to rest on Mursix’s flexible approach to technologies and agility to pivot or adjust processes during the product development stages, especially as the device goes through regulatory approval.
“It [the grant funding] gave Mursix the confidence to pursue production of a new medical device, the only patented technology of its kind globally.”
Susan Carlock
Vice President of Business Development at Mursix Corporation
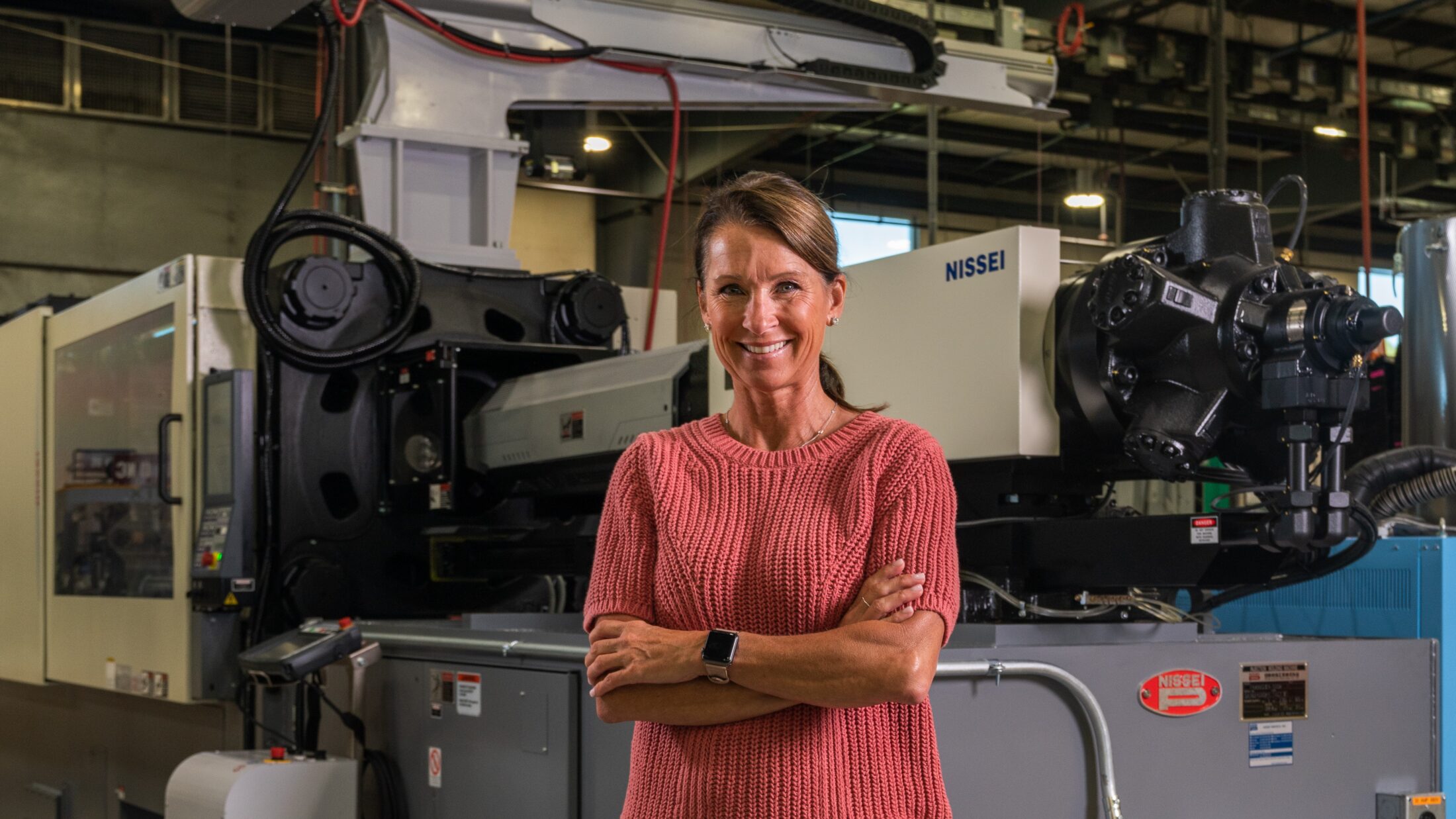