Smoker Craft Installs Custom-created Robotic Tube Welding System Saying, ‘There’s Nothing Else Like This in the World.’
Smoker Craft Inc.
Case Study
Key Stats
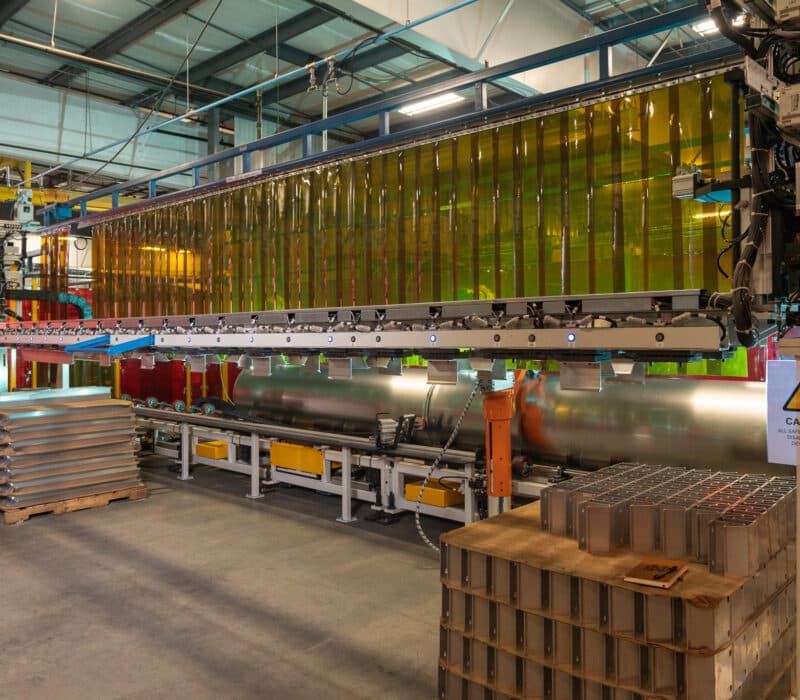
Company History
After 5 generations, 2 Indiana families continue in charge at Smoker Craft, the largest fiberglass deck boat manufacturer in the world.
The building that houses Smoker Craft Inc. occupies almost 1 million square feet in Northern Indiana’s New Paris, a community so small, it’s listed not as a town, but as a “census-designated place” (CDP) and barely 1,000 people call it home. The company dates back in Indiana’s history to 1903 when Arthur Schrock took a job at Star Tank and Boat Company in Middlebury, Ind., and purchased the company shortly after. Just a few miles away in New Paris, John Smoker founded Smoker Lumber Company in 1921 and soon sidelined into boat oars and paddles, calling that enterprise Smoker Oar and Paddle Company. By the mid-1920s, Smoker Oar and Paddle was the largest manufacturer of manual boat power in the world. The third leg of the Smoker manufacturing stool was in nearby Wolcott, Ind., where in 1948 the Sylvan Boat Company began building its reputation in houseboat and pontoon boat design and construction.
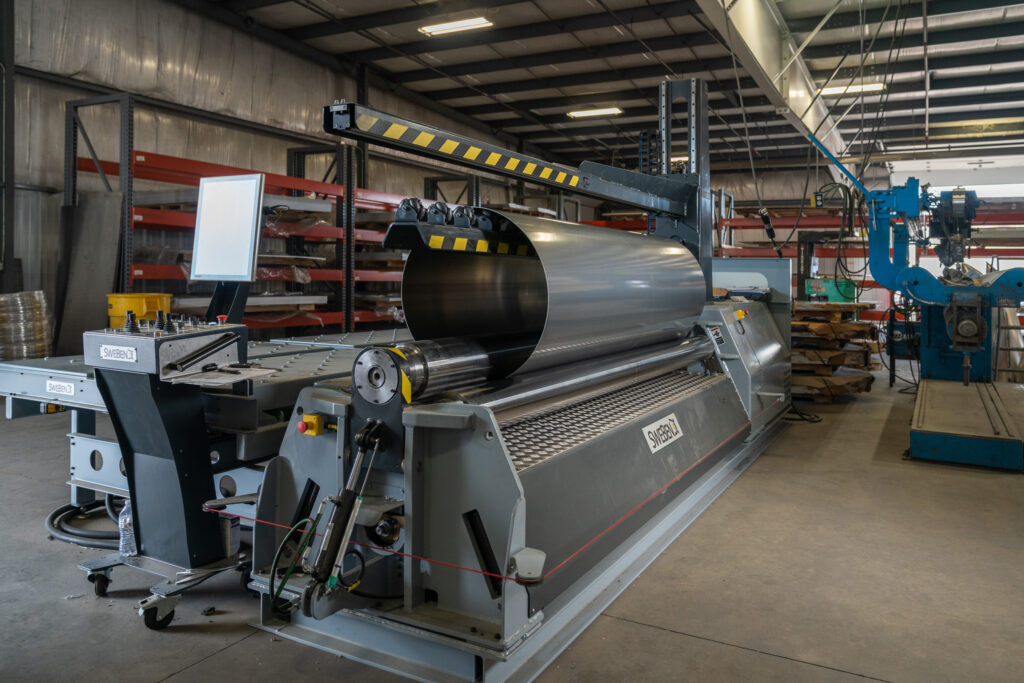
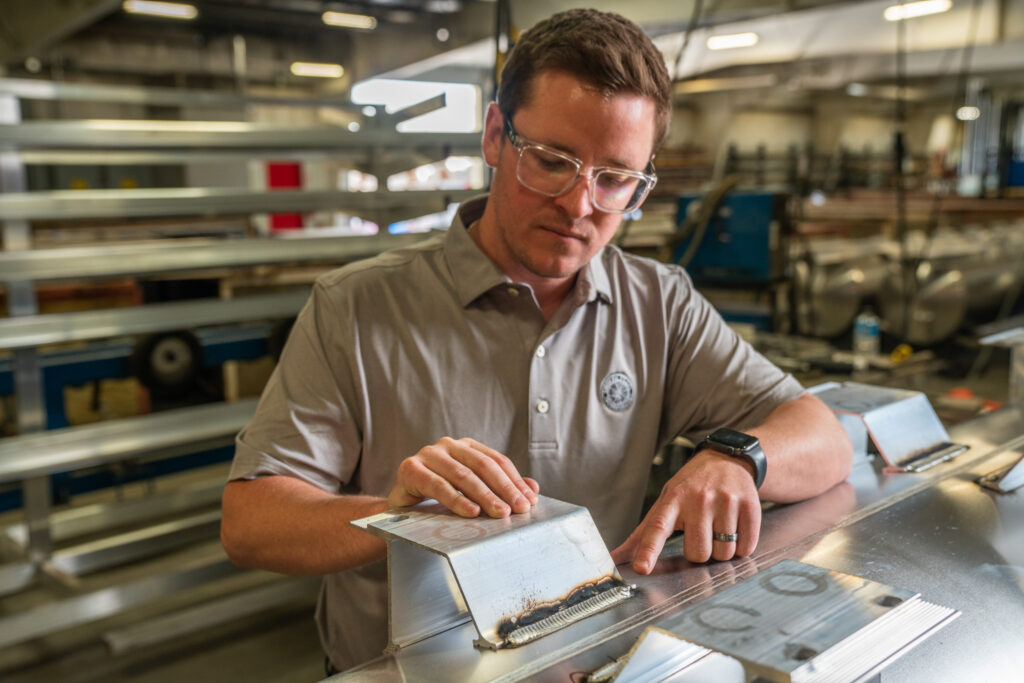
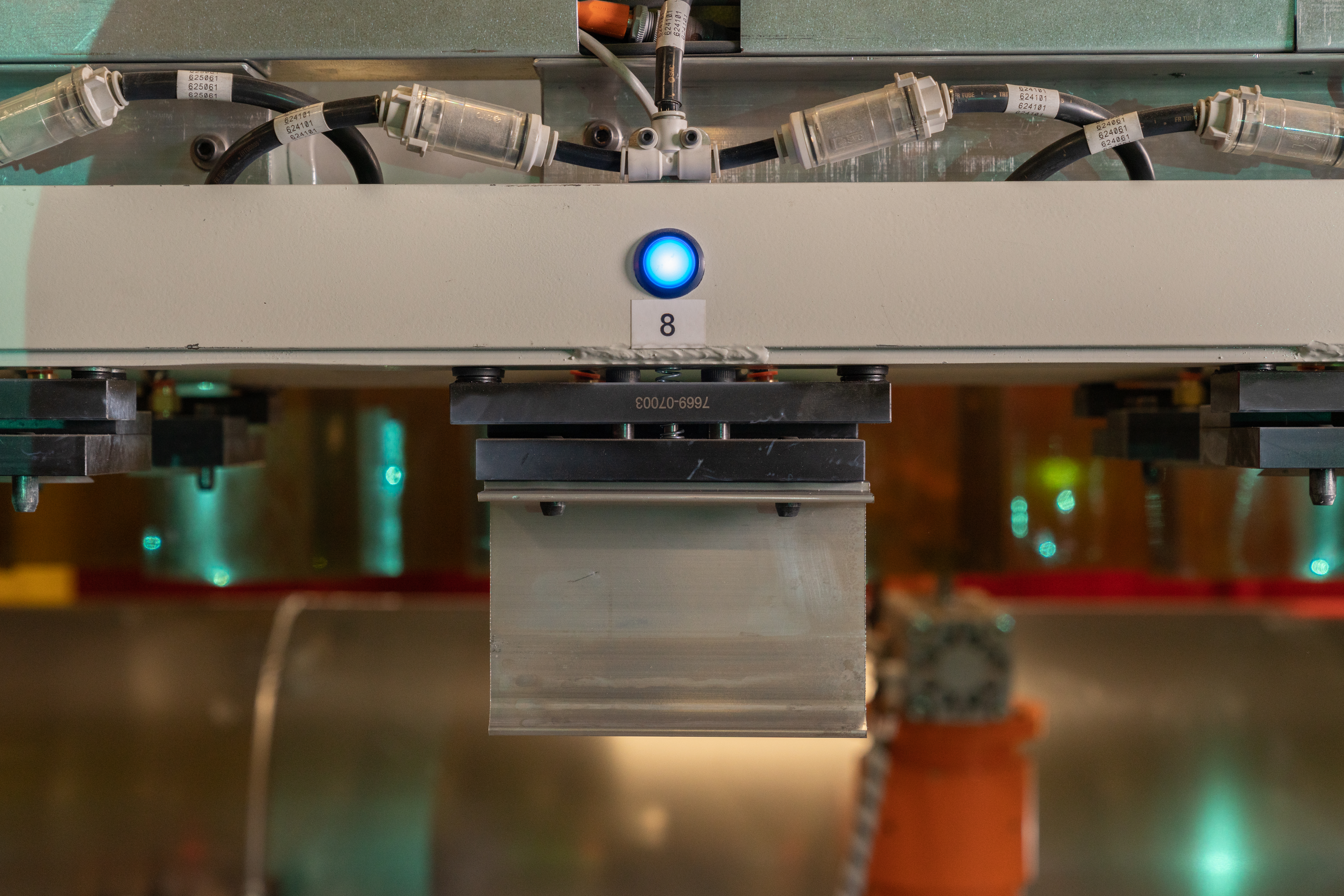
Today’s Smoker Craft Inc. officially came into being when Harold Schrock (Arthur’s son) purchased Sylvan in 1969 followed by Smoker Oar and Paddle Company in the mid-1970s. The mergers created what is now Smoker Craft, an international leader in aluminum boat production, boasting such innovations as the Deep-Vee aluminum hull design, the tri-hull Vega model, legendary Power-Trac hull, Hydra-Lift Reverse Chine Hull, Yarblow storage system, and RPT and SPX pontoons. The company’s reputation was attested by many industry firsts and awards for quality and customer service. Today the company supports more than 900 employees and is still owned and operated by descendants of the founding families. Together, the Smoker Craft team built over 20,000 boats in 2022, with aspirations to expand production capacity even more.
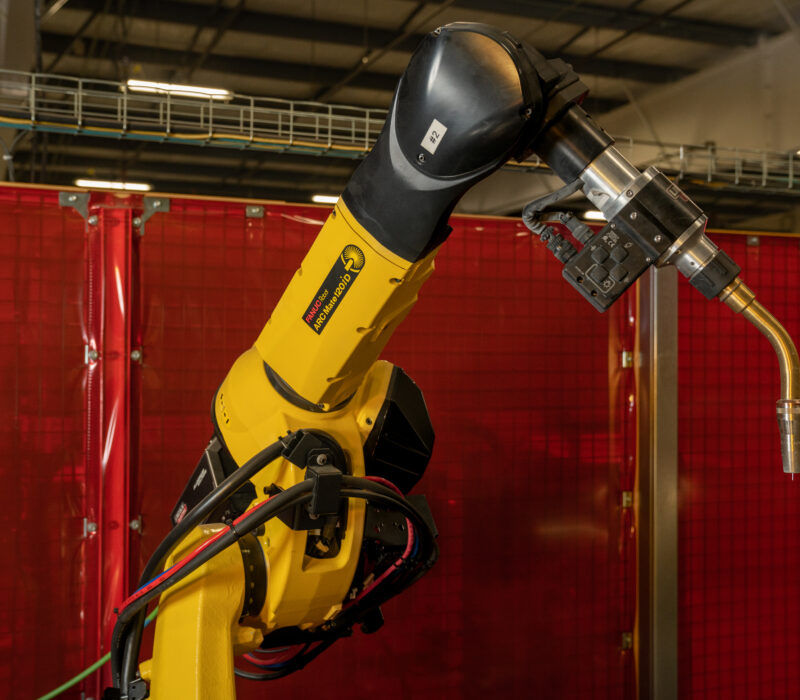
The Project
Designing and creating an Industry 4.0 solution unlike anything done before anywhere.
Michael Boyle interned at Smoker Craft in his last semester at Purdue University and moved into full employment as a process engineer after graduation in 2015. “I’ve had some awesome opportunities and seen exciting growth since I’ve been here,” he said. One of those opportunities was leading the Industry 4.0 smart technology project that earned a Manufacturing Readiness Grant of $200,000.
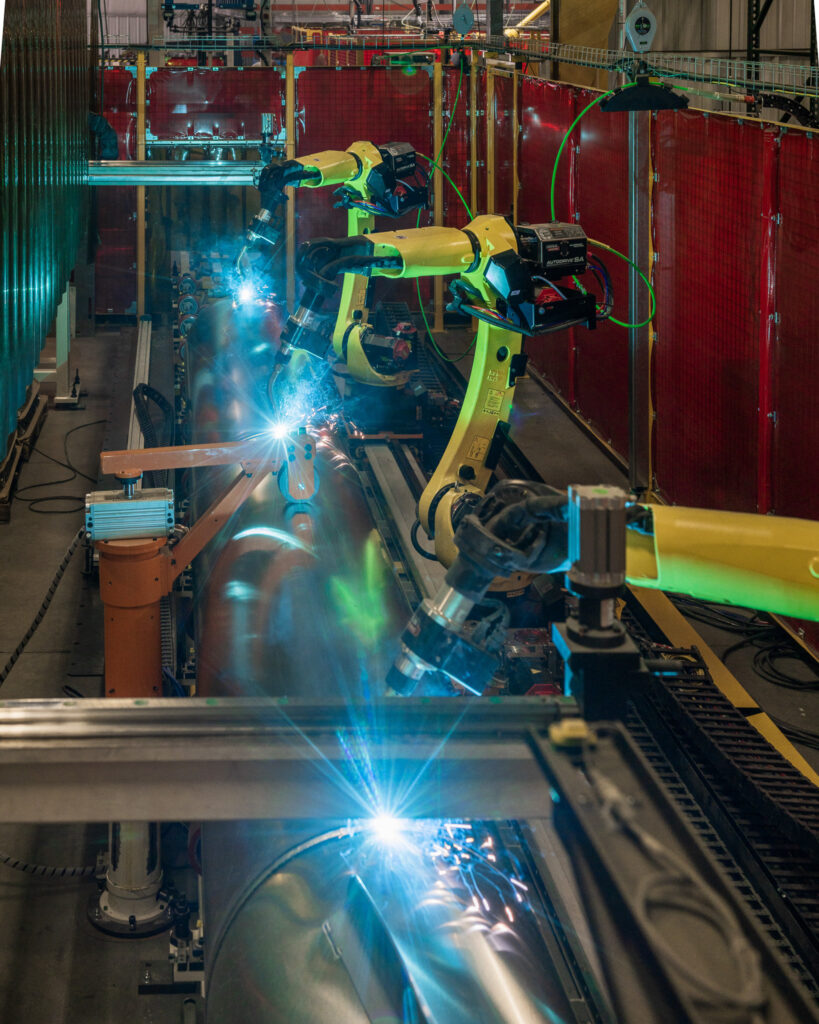
Throughout the years Smoker built its brands in fishing boats, pontoons, and fiberglass boats, each category including several models. “In all those years,” Michael said, “the designs have changed, but the manufacturing process has remained very manually intensive. Our low-volume high-mix was a challenge for automation. With the advancements in robotics though, we saw an opportunity.” The project was designed to automate every part of the pontoon assembly, beginning with robots to form and weld the nose cones and align those with the pontoons on pontoon circumference cells. “But they do so much more than just the circumference weld,” Michael said. Each tube is modular, consisting of several sections, and attached to the keel that runs the full length of the pontoon. That assembly can vary from 11 to 30 feet. Each boat requires either two or three pontoons placed side by side and joined by cross members. “We actually have 3 robots in each cell, operating independently,” he explained. “All 3 robots are welding and working at the same time. We’ve ventured in head-first, and it’s really exciting.”
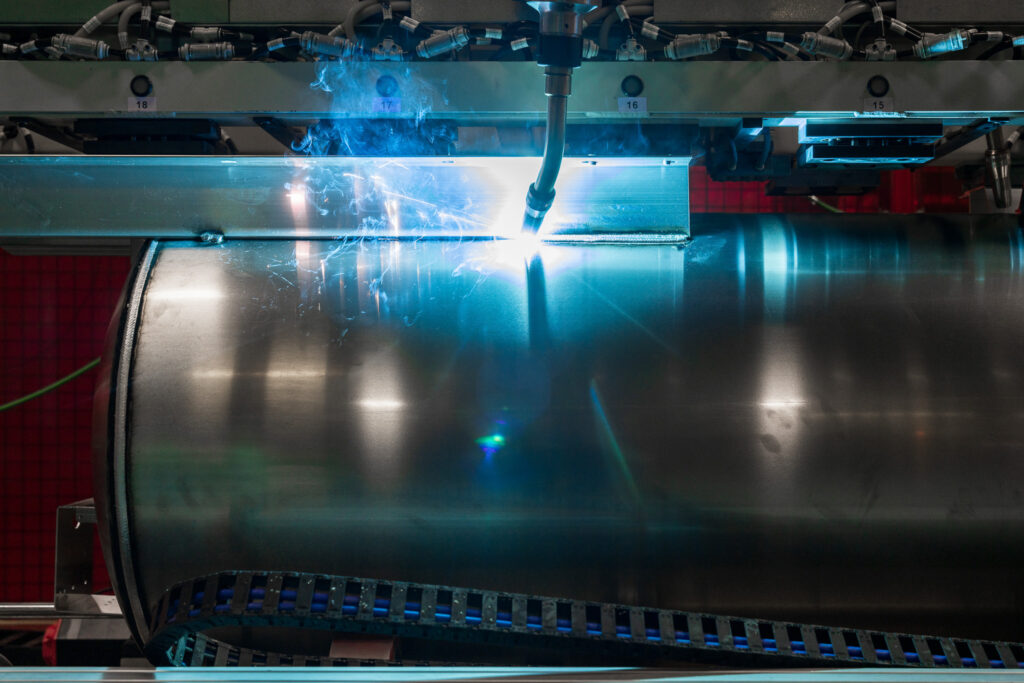
While the robotic cells are comprised of many commercial, off-the-shelf parts, it was custom designed to Smoker’s specifications that would ensure cycle time and other key parameters were met. “It is extremely custom,” according to Michael. “There’s nothing else like this machine in the world.”
The technology can be fine-tuned to a degree that was impossible to achieve with manual welding while increasing speed and efficiency.
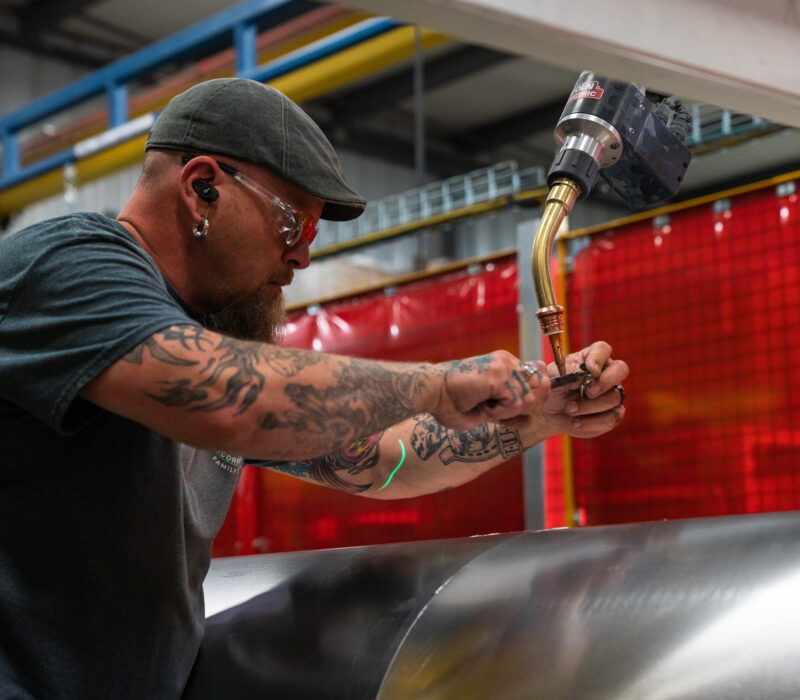
Workforce Implications
One new single-shift worker operates the system that does the job of 8 employees.
One of the goals when the project was conceived was a user interface operable by someone with no programmable logic controller (PLC) training and no robotic training. Leadership recognized that business was growing but the availability of skilled welders and operators was slim. The result was potential production left on the table. “The project grew from there,” Michael said. “That’s part of the issue in our area. We’re competing for welders in the RV industry. We fight every day for welders. We brought in these lines not to replace our current ones, but to be an addition to them.” Adding additional lines without the technology would require some 20 new welders and that, he said, was not viable. Instead, the new equipment would be operated by a single operator on a single shift. “We said we wanted to lower the barrier of entry for production workers,” he said, adding, “someone with no technical background, at an entry-level position that we could train to operate the robotic welding technology.” That ultimate solution has worked “Right now we’re producing around 60 pontoons a day on one 8-hour shift. “And that operator is maintaining equipment and ensuring that robotic welders run smoothly,” Michael pointed out.
Michael does all programming on the equipment. “I love this stuff,” he nodded. “But as a process engineer, I didn’t have experience with the technical side of it. I went back to school to learn about smart manufacturing and digital integration. These robots are my babies, all 8 of them.” Ivy Tech Community College and time at Lincoln Electric for intensive week-long courses were part of the Purdue graduate’s personal “up-skilling.” Michael specifically noted courses that he completed within the Smart Manufacturing and Digital Integration program to earn industry certifications focused on robotic automation technology from groups such as the Smart Automation Certificate Alliance (or SACA).
The existing workforce understood the process wasn’t replacing positions but adding to them. “We explained that ‘this is going to allow for increased production without having to increase time spent at the plant.’ We haven’t seen pushback, because our employees know it is in addition to their positions, not in place of them.”
Manufacturing Readiness Grants provided by the Indiana Economic Development Corporation (IEDC) and administered by Conexus Indiana are available to Indiana manufacturers willing to make capital investments to integrate smart technologies and processes that improve capacity, efficiency and productivity. Smoker Craft Inc. utilized its $200,000 Manufacturing Readiness Grant to create a custom-built cobot welding system at its New Paris, Indiana, facility.
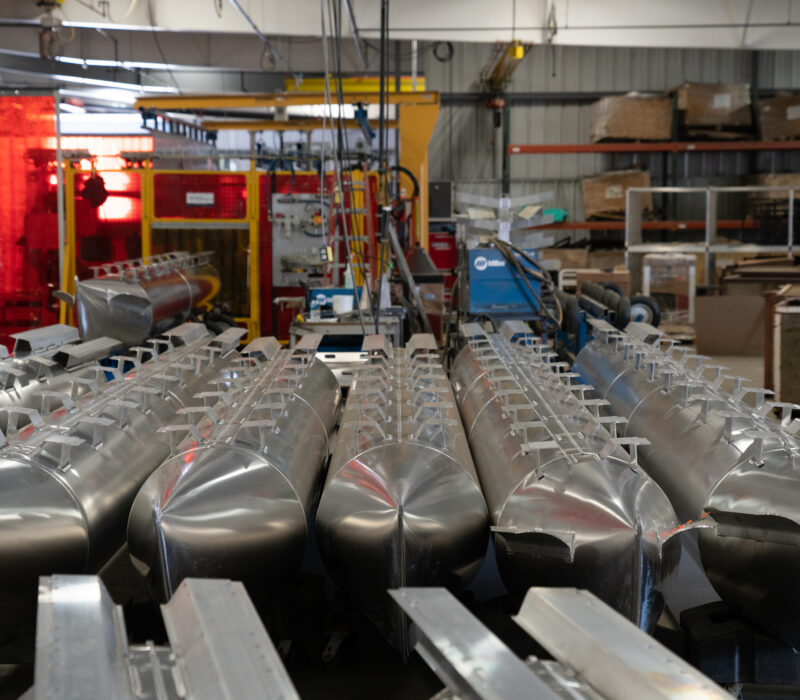
Shared Learnings
Choosing a local tech integrator, one willing to help design the system from the ground-up, was essential to the project’s success.
Smoker wasn’t initially shopping around for robotic welding solutions. Guide Engineering, a technology integrator from nearby Ft. Wayne, Ind., originally approached the company with their nose cone concept and, once Smoker leaders looked at it, they wondered if it would be possible to go beyond that. “We took a serious dive into it,” Michael said, “and started looking at cost. They considered what it would take to set up the additional volume manually, versus what it would take to do it through automation. “We looked at it machine by machine, person by person, everything we could fit in. And it came out that automation was barely more expensive to start with and, over the grand scheme, it was significantly cheaper to run. We could see a return on investment within one full year of production. Plus, we knew we would have a hard time finding the employees to meet our production goals. I don’t want to say it’s doing the job of 6 people, but it would have taken more welders that we don’t have and can’t find to do the job the robotic cells are doing.”
It was “the art of the possible,” he added. “You don’t know, what you don’t know. The tech integrators are so important to the process. You can’t just look at your process and wonder how to do it faster, cheaper, better. You need experienced eyes that can study it and suggest what’s possible given the limitations of the industry,” also pointing out that automation used to be the world of high-volume, high repetition. Today it’s much more adaptable and flexible, and a good tech integrator can open the door to the next level of automation. Taking that extra look can identify where control of the process is lacking. Otherwise, it’s just automating something that is already out of control. Automating that process just institutionalizes it and makes it much more difficult to correct later.
Automating the process in this instance allowed Smoker to move from manual TIG welding to robotic welding, considered stronger and of higher quality. But it is also more difficult to master manually. Michael explained, “has opened the envelope for process changes in quality and improvements because we’re now building on a super stable, super consistent foundation. If you’re spending $100,000, you want it to look like $100,000. With the introduction of our automation applications, we have been forced to improve the quality and foundation of our boats. Automation is not magic, so parts going into these cells need to be rock solid and in spec.
Overall, it has been an awesome experience with us and Guide,” Michael said. “We talked with other companies, but we’re very happy with our choice. Having people who are very similarly minded and have priorities in line with yours helps to push that ball to the finish line.”
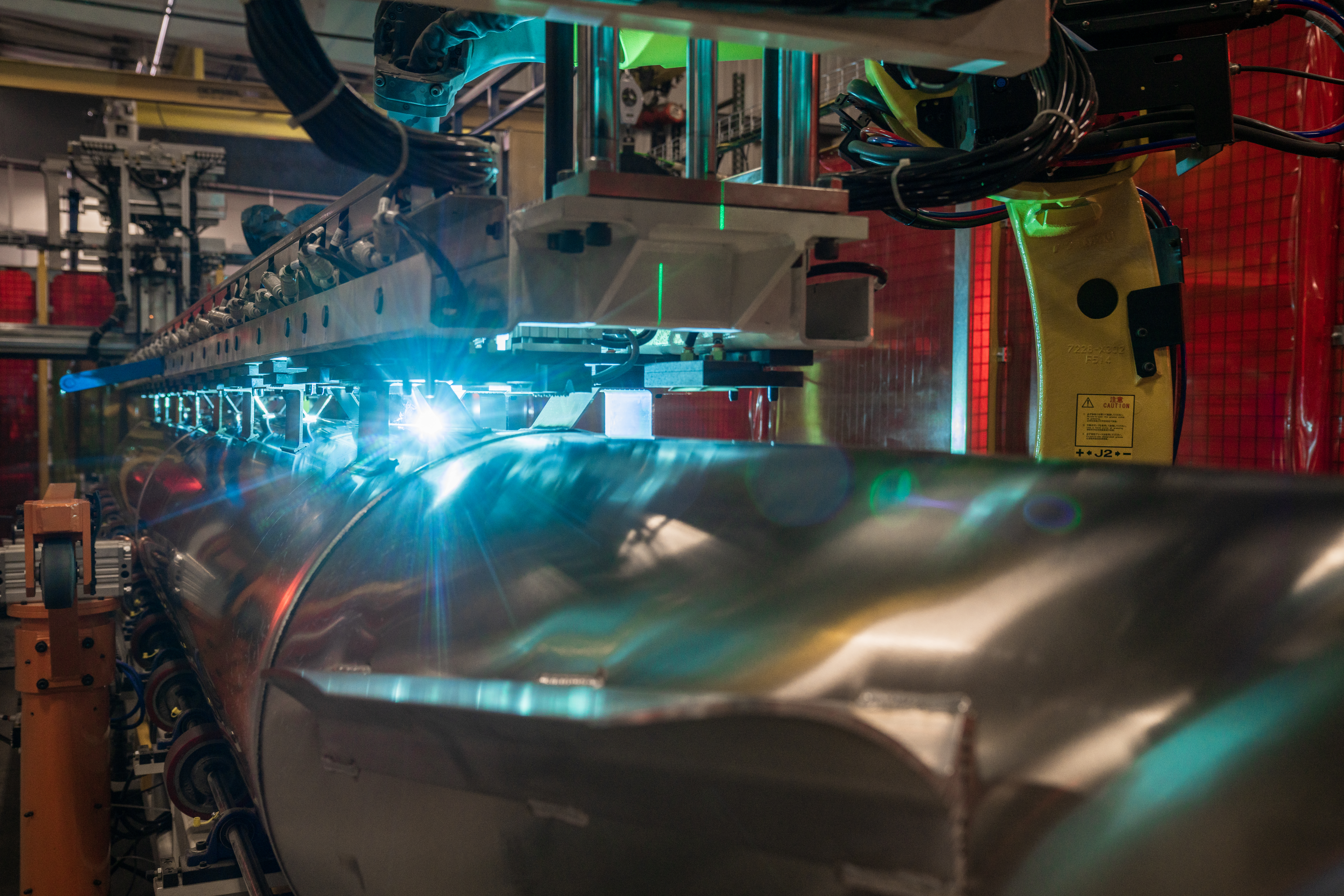