Nimble Stair Supplies Seizes the Opportunity to Embrace Continuous Production with a Manufacturing Readiness Grant
Stair Supplies
A Case Study
Key Stats
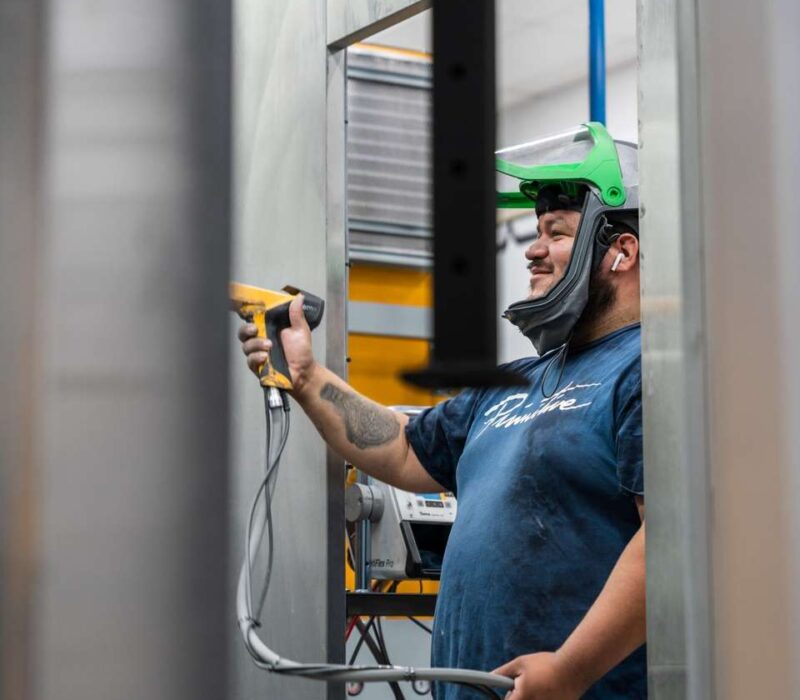
Company History
Stair Supplies Embodies Some of the Best Qualities of a Startup Company: Innovative, Agile and Growing.
Stair Supplies is not a start-up, but the company embodies some of the best qualities of one–innovative, agile and growing. Founded nearly two decades ago in 2004, it was originally an online sales company marketing stair supplies manufactured by others. Today, Stair Supplies manufactures its own premium stair systems and sells direct to homeowners, builders and contractors. With an almost 30-fold increase in production in the last decade and recent growth averaging between 50% and 70% annually, it maintains a start-up mentality. Not married to its batch processing system, the company has recently been “striving to automate all of our production into continuous flow,” specifically looking to implement a conveyer-based powdercoat line.
The potential advantages to the transition are clear: Automation would more than double capacity; material flow organized by orders with a first-in-first-out model would simplify a batch system made confusing by the sheer number of small pieces to be shipped with each order; color changes would be more flexible and swifter; and future opportunities for growth could be more easily met by adding another automation line. Physical space, however, was the primary barrier to making the transition. The manufacturing facility was inadequate to house and manage the equipment needed to make the switch from a batch to continuous flow.
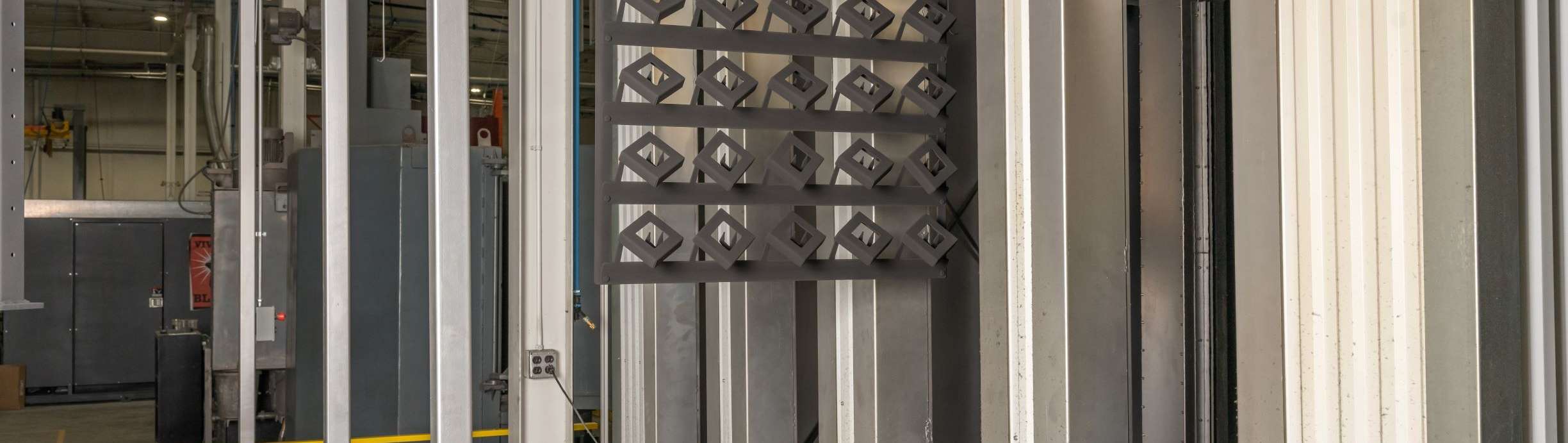
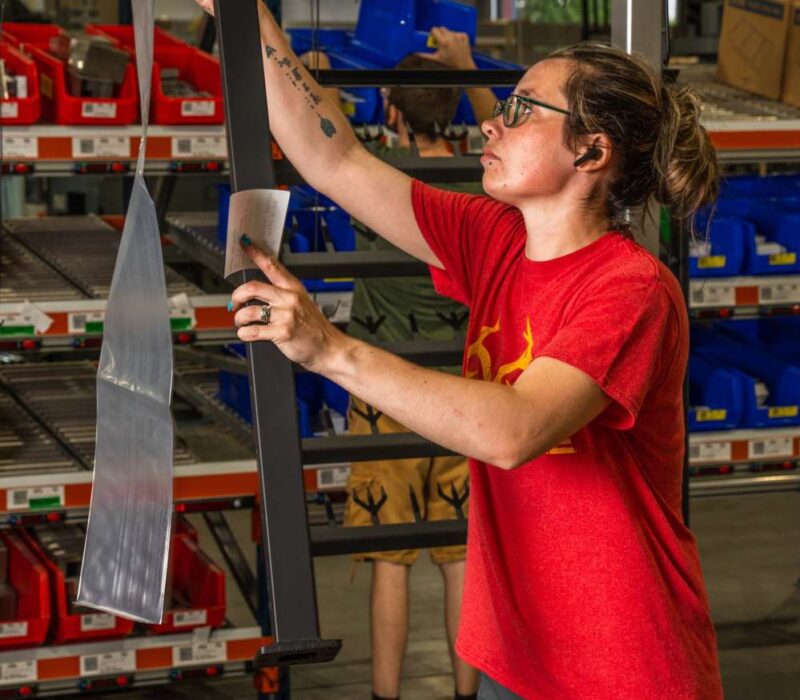
The Project
Everything Came Together: the Space, the Funds, & the Proof of Concept.
By 2020, physical space as the major stumbling block was removed. The Goshen-based company had relocated to a new, larger facility in the same Northern Indiana community, and began making plans to implement the transition to a continuous flow process. “It was the right time,” said Brett Harbaugh, CFO of Stair Supplies. “We had the space. It was the right time from a budgetary standpoint, and there was this new opportunity for the Manufacturing Readiness Grant to help relieve some of the costs. That definitely helped push us even more to decide that it was time.”
By 2020, physical space as the major stumbling block was removed. The Goshen-based company had relocated to a new, larger facility in the same Northern Indiana community, and began making plans to implement the transition to a continuous flow process. “It was the right time,” said Brett Harbaugh, CFO of Stair Supplies. “We had the space. It was the right time from a budgetary standpoint, and there was this new opportunity for the Manufacturing Readiness Grant to help relieve some of the costs. That definitely helped push us even more to decide that it was time.”
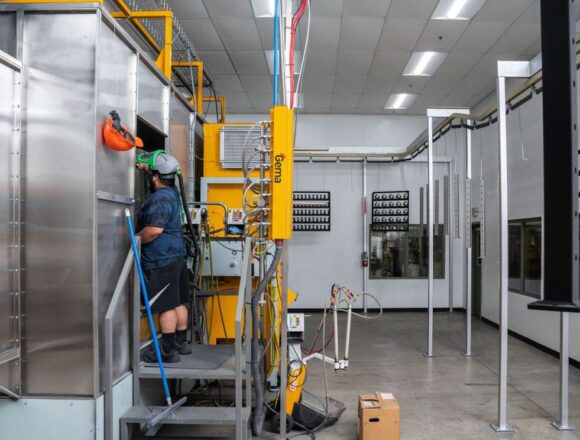
The team also compiled a considerable amount of data to support their decisions about what equipment would need be implemented, including line speed projections and first-in-first-out order processing systems. The manufacturing process would need to be aligned with internal metrics from the sales department. “We had to really look at the data and say hey, sales is telling us to do 10 to 13 colors [changes] a day,” said Lincoln Rassi, manager of the Stair Supplies manufacturing plant. And to meet these requirements, efficient color changes were a vital piece of the soon-to-be developed automated power coat line.
After months of intense due diligence, the machinery was ordered in late October 2020, with a projected delivery date of February 1, 2021. “The D Day, as I call it,” said Rassi. “Everyone involved showed up, and the equipment is here. By the end of January, we had the conveyor line built, the room constructed. A lot of hands were involved that did a great job of pulling through with this project in a very short lead time.” By the end of February 2021, the company had successfully implemented an automated powder coat line, which can track items by QR codes, boasts a 20-second color change, and coats 600 posts in just under 3 hours – quite an improvement from 600 posts in about 8 hours, including a 2 to 3-minute, manual color change process.
Manufacturing Readiness Grants provided by the Indiana Economic Development Corporation and administered by Conexus Indiana are available to Indiana manufacturers willing to make capital investments to integrate smart technologies. The smart technology and process investments being made at Stair Supplies to migrate from batch to continuous production for their custom order process met those requirements.
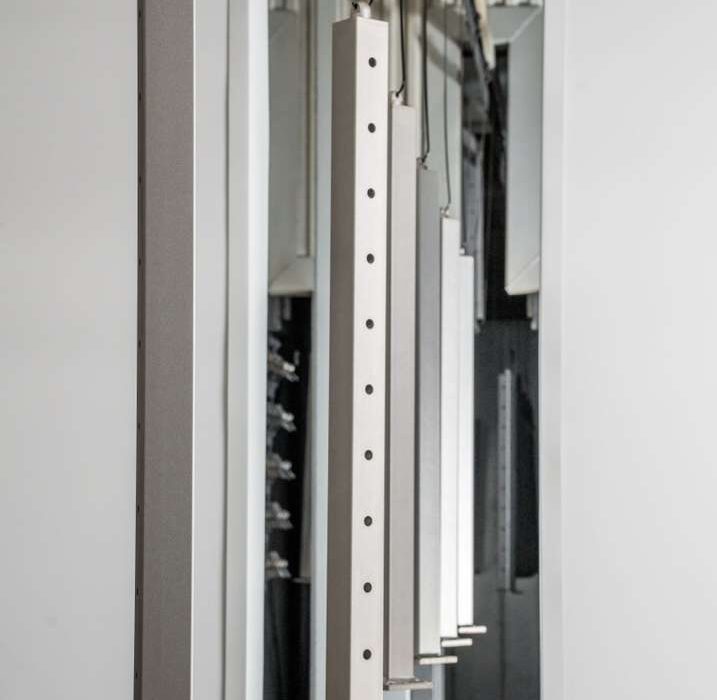
Project Impact
Automated Power Coat Line to Propel Production Capacity & Improve Order Completion Rate.
“In terms of measuring the success of the technology adoption project, it’s immediately doubling daily production of railing posts (‘posts’),” Rassi said. Under the current batch process, the goal has historically risen more than 20-fold in the last 15 years. That’s remarkable in itself, but there was no more runway to grow without major change. Rassi is aiming to double again this year under the new continuous flow process. “The big measure for success in my opinion, and we still have yet to prove it, but we’re on the verge of all the QR codes that guide conveyers to flow into the other conveyors. The key metric is order completion rate.” He’s convinced they will get there. “On average, one post has about 2.3 additional components,” he explained. So, if you do 1,000 posts you multiply that by 2.3 and that’s where you’ll see upwards of 3,300 parts a day going through the line. That number, with newer components and smaller pieces, keeps growing. So, a 10 post order, can easily have 30 to 40 pieces depending on the mounting hardware style.”
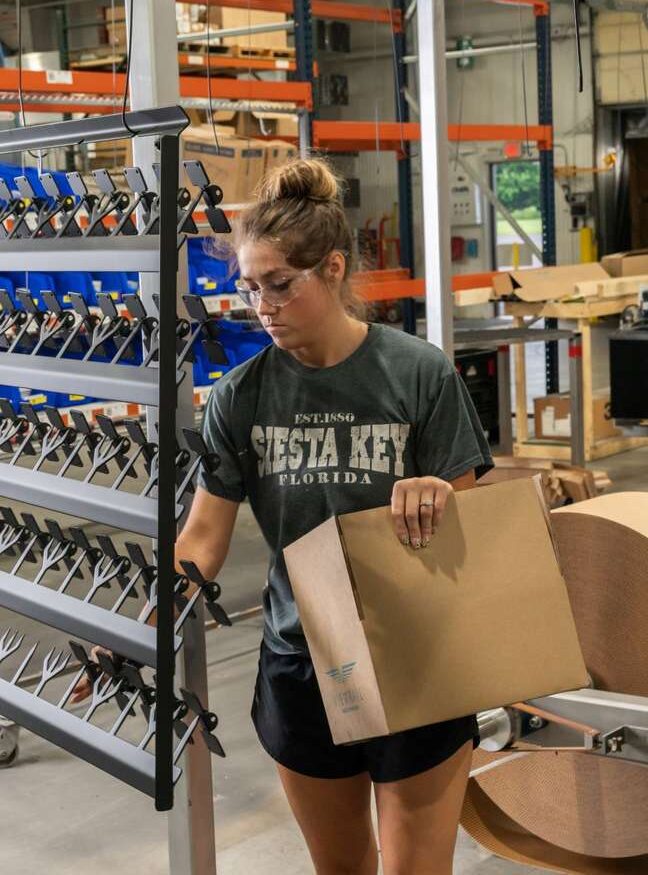
It may look like a powder coating project, but it’s really a digital plant initiative. Rassi points to the inefficiencies in the old batch process that required more paperwork and more marker boards. With the new system, everything trickles into place because it’s been tracked automatically. “The order comes off the line 100% ready to be packed and shipped,” Rassi said. “Look at value added time. In smart manufacturing, we get paid to apply the powder and make sure it gets packed in a box. All these other organizational steps, we don’t get paid for those. These conveyors and these cut files eliminate a lot of the brain work that happens upstream, and we work on optimizing our processes. In the end, we focus more on quality and throughput instead of where the parts are at.”
Harbaugh agreed. “Having that opportunity out there was something that definitely took this from something we’ve been talking about and pushed it over the edge of saying, okay, this is something we really want to take the next steps with, researching and getting drawings and figuring out what all it would mean,” he said. “And then when we received the grant it was perfect. We’re all bought in and agreed that this is the direction that we should be going.”
New Hires Accelerate Stair Supplies’ Transition to Continuous Flow
Barely two months into the transition, Stair Supplies has made three new hires, two powder coat operators, and one new employee with experience in operating and maintaining cleanliness in automated powder coat lines. That cleanliness is a key part of the employee’s responsibility. Rassiknew he’d need an individual with project-specific experience to make this a successful transition, “I recruited someone who… knows how to run a powder coat line with multiple color changes, how to keep the equipment clean, and knows what to look for when diagnosing issues.”
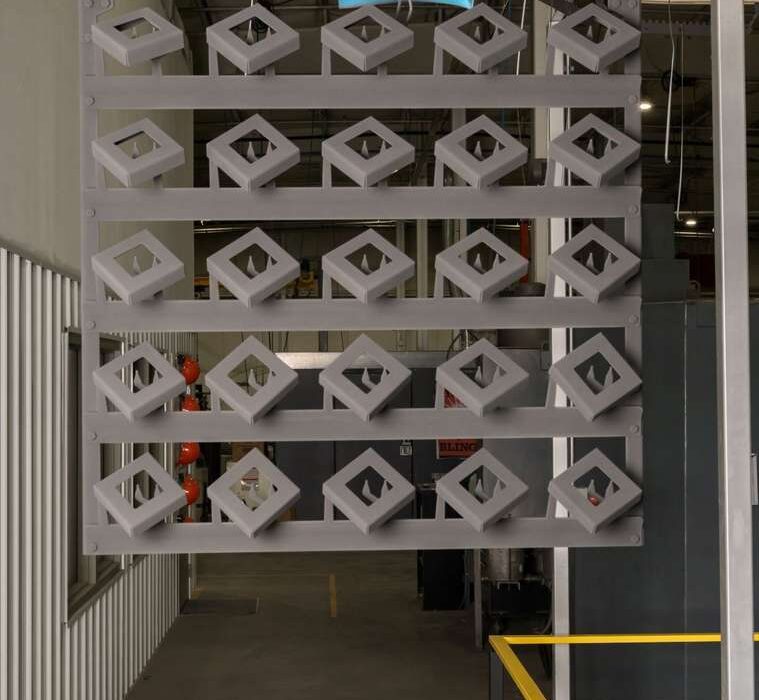
Key Learnings
Preventive Maintenance Training & Implementation of Digital Tracking Technology Prove Vital to Project Success
Preventive maintenance training to maintain conveyor belt cleanliness is crucial. “A lot of training time wasn’t operator-based as much as it was maintenance-based,” Rassi pointed out. “Preventive maintenance is huge on these controls. We’re on a train track here, and the conveyor is going this fast, and we can’t afford for that conveyor to stop. The preventive maintenance is the biggest thing that the training has taught us, and we still have a lot to learn.”
The company needed to get the tracking technology in place, too. For Stair Supplies that technology was QR codes. Other equipment also was required, such as what is needed for rapid color changes, an important benefit of the new system. Rassi remembers a time not so long ago when things weren’t nearly as digitized. “We used to manually drill. I think that was just five years ago when we first started doing cable railing. We had a manual drill press, and an operator would have a little print and then just go through and manually draw everything,” he recalls.
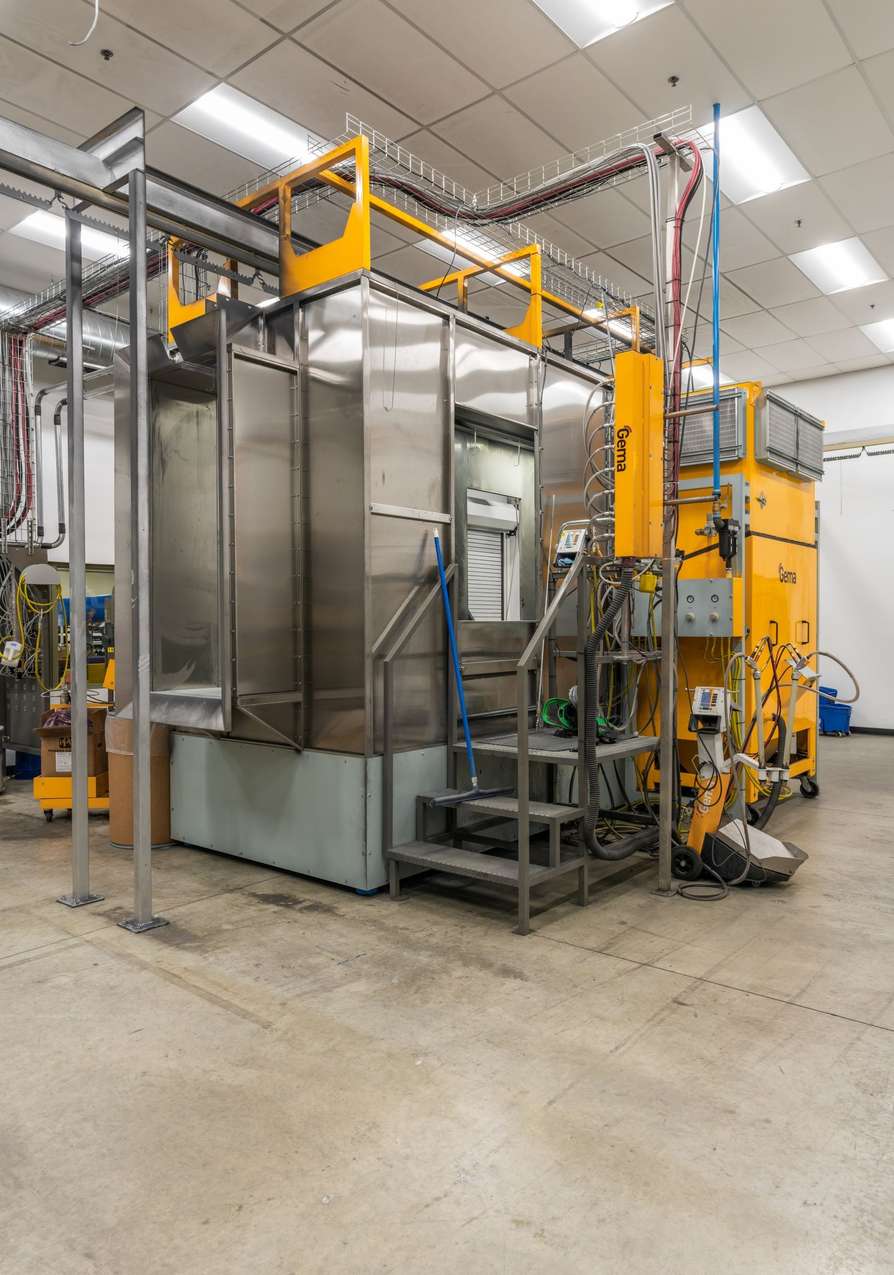
“With the automated process, the QR code will pull up the program file to run for the operator. There are over 10 thousand different ways we can drill and cut a post. It’s very important we get that right, so we created a database system to pull up those programs. We’ve had that in the works for a couple of years, and we’ve seen the fruits of that labor over the past year.”
After the planning phase, the company leveraged multiple partnerships with other Indiana firms for the tech adoption project. Midwest Finishing Systems in nearby Mishawaka, for instance, partnered to provide the fabrication and installation of the powder coat oven and conveyor line. While American Industrial Corporation out of Greenwood, Indiana and Gema Powder Coating in Indianapolis provided technical support and implementation of the new powder coating equipment. Lastly, Shane Dyer (StairSupplies buildings engineer) and his team were able to construct a 1,700 square foot environmental room in as little as 4 weeks. While all team completed their part of the project two weeks in advance of the promised delivery date. Rassi mentioned, “A lot of hands were involved that did a great job of pulling this project together with a very short lead time.”
“In terms of measuring the success of the technology adoption project, it’s immediately doubling daily production of railing posts (‘posts’).”
Lincoln Rassi
Plant Manager at Stair Supplies
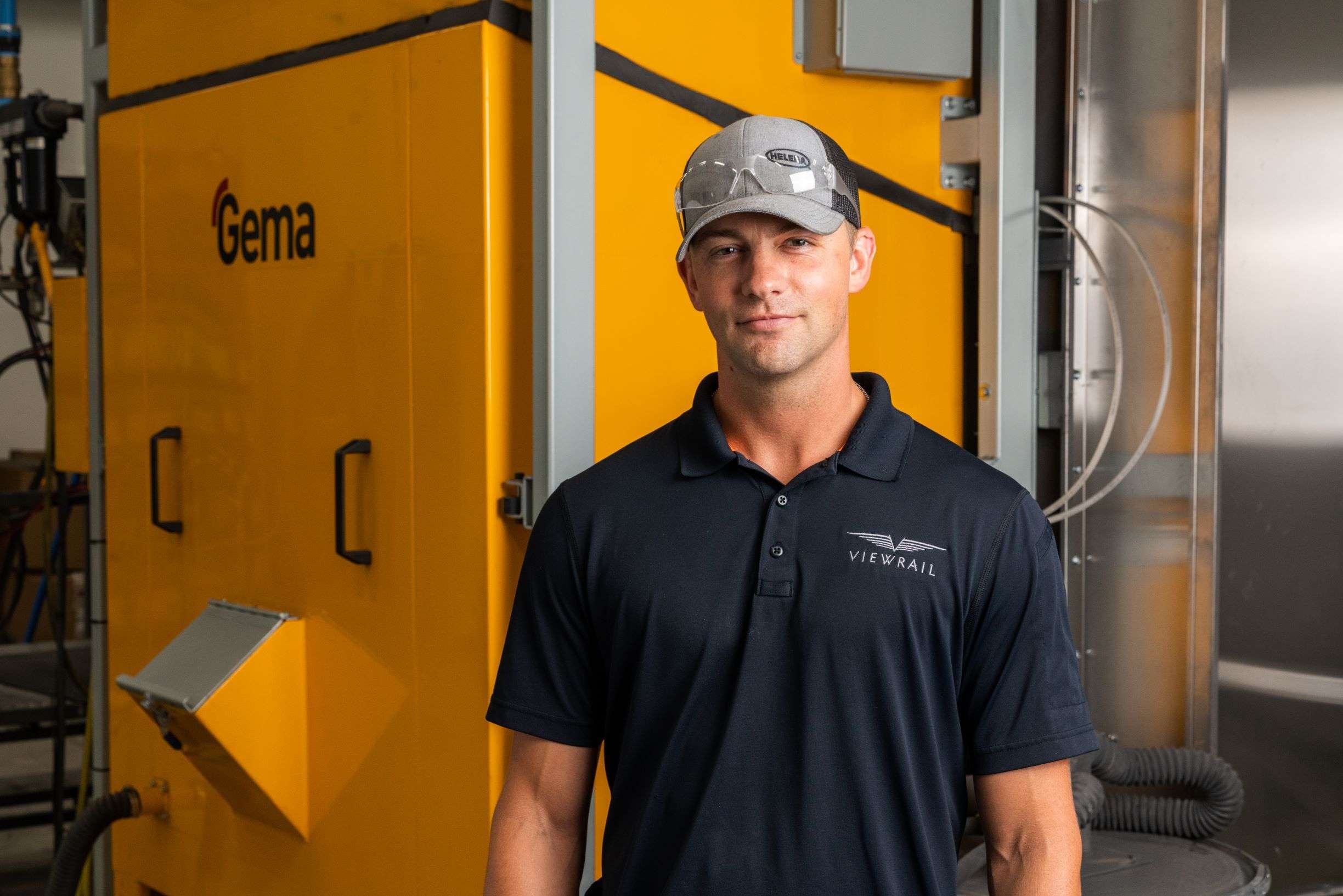