Innovative approach to part-time and gig workers helps Toyota Material Handling’s Parts Distribution Center reach untapped workforce
Toyota Material Handling
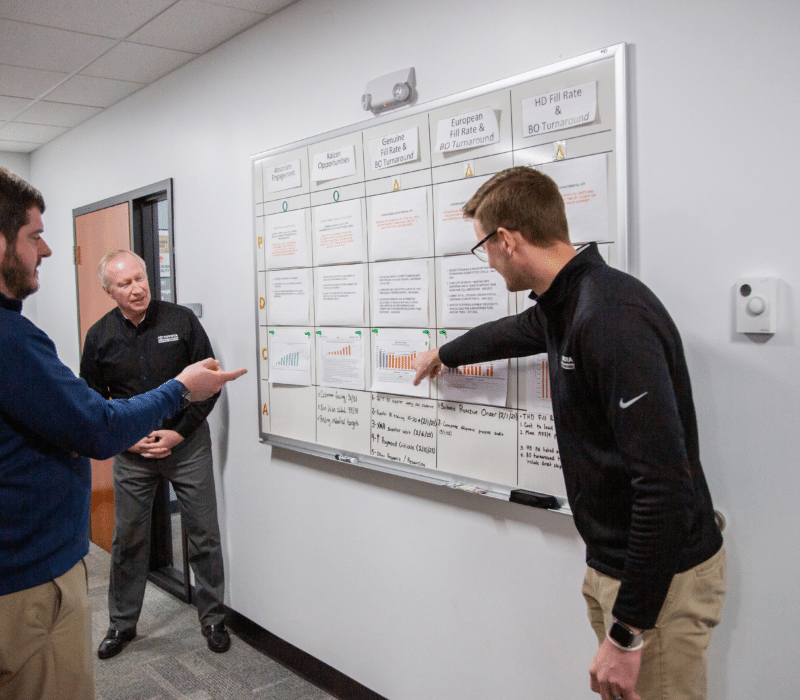
Background
Since opening in 1990, Toyota Material Handling’s Columbus plant has produced more than 750,000 forklifts as well as other material-handling machines while also distributing parts and accessories to its industry-leading North American customer base.
While most people likely associate Toyota with top-selling automobiles like the Camry and RAV4, Toyota is also a world leader in the production of forklifts and other material-handling equipment and solutions. In addition to manufacturing those workhorse vehicles in Columbus and East Chicago, Indiana (Toyota Heavy Duty), the company also supports customers with parts distributed from the company’s Columbus headquarters.
A pick-pack-and-ship operation, the facility is the only source for Toyota Genuine Parts for its North American dealer network. And with hundreds of thousands of forklifts – not to mention other material-handling machines – having been produced in Columbus, the 87-member team that makes up the Parts Distribution Center must hustle to keep up with demand during its three shifts of operation.
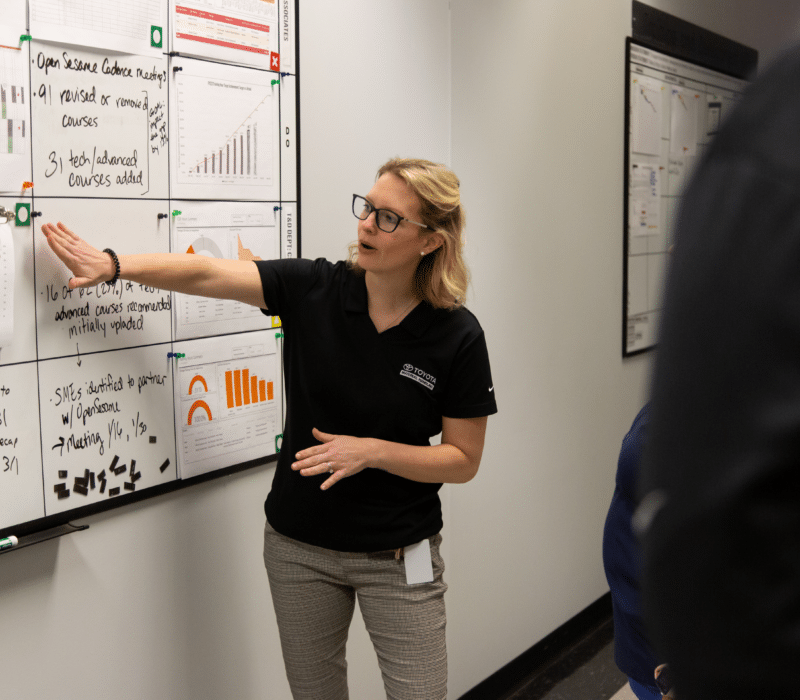
Challenges and Solutions
Business growth brought three interrelated challenges to Toyota Material Handling’s parts warehouse: finding enough workers in a thin labor market, fitting those workers into a limited space, and ensuring a worker experience worthy of Toyota’s employer brand.
Toyota Material Handling’s parts distribution operation has seen steadily increasing demand over the last few years, said Warehouse Manager Sandi Hahn, and the company has worked to add to its workforce to keep pace. Of course, in this effort, the company recognized that it faces the same tight labor market as every other employer, but it also saw that the type of workers in the labor pool had changed as well. More workers were looking for an alternative to the traditional 40-hour work week.
The company decided to look beyond those traditional 40-hour workers and open its distribution team to part-time labor. This step quickly increased the talent pool from which Toyota was hiring, Hahn said, bringing a segment of the workforce to the company’s doors that previously would not have considered Toyota as a possibility: people who want to work fewer hours each week, perhaps because they have a full-time job and want additional income, are students, need to be home with children, or have other reasons.
In addition, by scheduling these workers in times when workloads are heavier, the company can reduce extra burden on full-time workers, not be overstaffed when workloads are lower, and not add extra bodies in an already congested space. The company partnered with Elwood Staffing to put together a dedicated contingent of part-time workers on consistent schedules, allowing both the company and employees to plan ahead.
After finding success with this approach, the team took the flexible scheduling concept a step further by collaborating with Veryable, a national supplier of on-demand workers to manufacturing and logistics operations, to bring in short-term workers for specific needs. For example, if a big shipment of parts is expected, or a big order needs to be prepared for distribution, Toyota Material Handling’s Parts Distribution Center can bring in a handful of workers to fulfill that work without pulling its full-time workers away from their usual roles or overworking its regular team members during peak times.
In both the part-time and on-demand scenarios, Toyota Material Handling often can bring the extra workers in during second or third shifts, when there are fewer workers in the warehouse and more room to work.
To further address the challenge of limited space, the company is investing in warehouse automation, Hahn said, which will allow it to go more vertical with the 44,000 parts it keeps in small-part bins in its warehouse and do more work without adding more workers.
As it implemented these approaches, Toyota wanted to ensure that it wouldn’t diminish its commitment to providing employees with an enriching workplace that supports individual growth and success. Leaders have worked hard to make part-time and gig workers feel like they are a part of the team, Hahn said, to make full-time employees feel comfortable having the part-time workers in the workplace, and to support ongoing growth and opportunities for all. To that last point, Hahn said that part-time workers brought in by Elwood Staffing who are interested in full-time work and prove themselves to be good workers are eligible to be hired, and some have been.
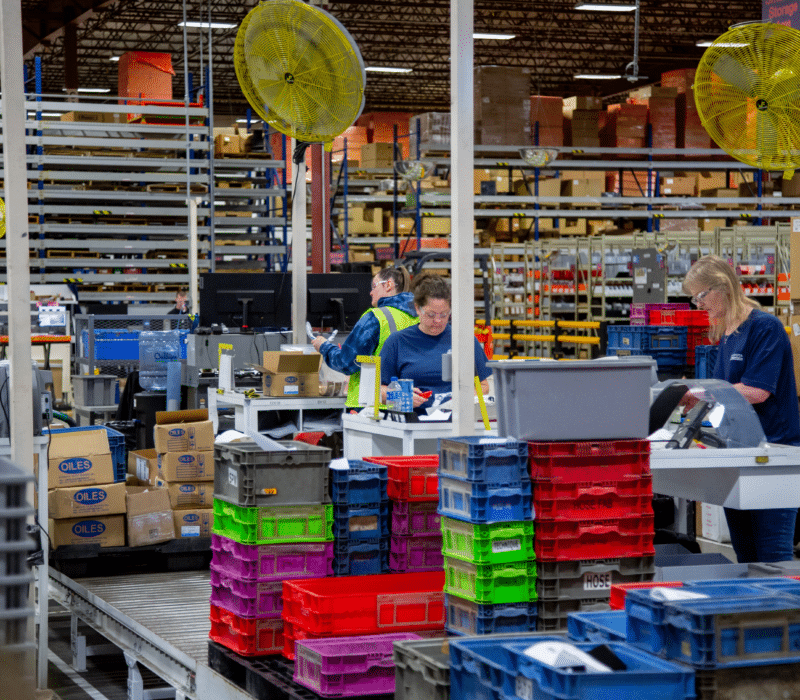
Key Learnings
Flexibility, ingenuity and automation have been key to adapting to an evolving workforce and marketplace.
“We didn’t want to do it the same way we’ve always done it.”
Toyota Material Handling’s workforce challenges certainly aren’t unique, but its three-part approach to addressing those challenges is. A key to success, Hahn said, is a willingness to look beyond typical hiring approaches and consider alternatives. It pays, she said, to take time to be creative, noting that the part-time-worker idea came from a brainstorming session she was involved in during a business trip. “We didn’t want to do it the same way we’ve always done it,” she said.
Taking a flexible view of what it means to be a part of the Toyota Material Handling team also has been essential, Hahn said, and the company has found success by making part-time workers feel as much a part of the operation as full-time employees while giving them the flexibility to work at times that are most practical for them. At the same time, she said, the company found real benefits from what she called “rigid flexibility” – an agreement between the company and part-time workers that, while they work reduced schedules, they keep the same schedules from week to week.
Toyota has also made progress by building on the success of one good idea to create another. In this case, recognizing the benefits of part-time workers led to further embracing the gig-worker marketplace. The company has benefited from working with partners to bring in those nontraditional workers, rather than trying to manage the different types of labor arrangements itself.
Finally, Hahn said, the company looks forward to complementing these innovative hiring approaches with warehouse automation that will allow it to use its space more efficiently without dramatically changing the skills required from its workforce.
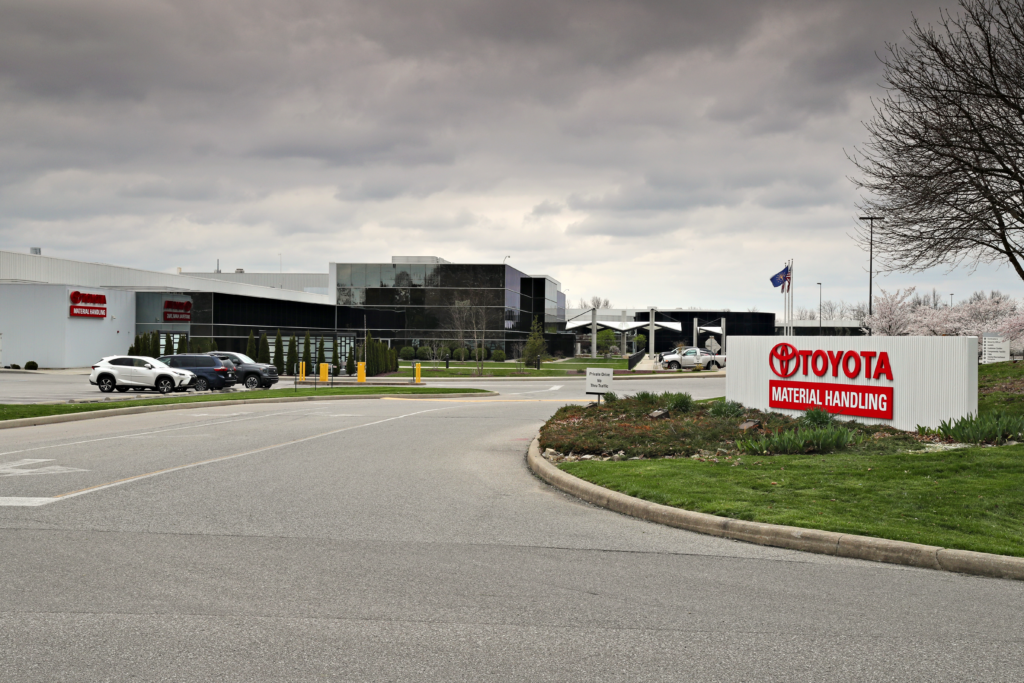